Laser welding is the primary method of high-end battery welding at the moment.
Laser welding is a method in which a high-energy beam laser irradiates the workpiece, causing the working temperature to increase significantly, the workpiece to be melted and rejoined to create a permanent connection, and the shear and tear strength to be reasonably strong. The electrical conductivity, strength, air tightness, metal fatigue, and corrosion resistance of battery welding are common assessment criteria for welding quality.
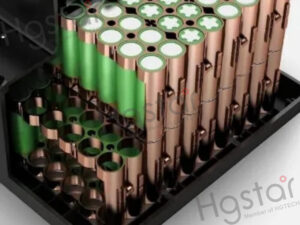
There are several elements that influence laser welding quality, some of which are exceedingly dynamic and unstable. The practicality of laser welding technology, an important issue of industrialization, is related to how to correctly set and control these parameters so that they can be controlled within a suitable range in the high-speed continuous laser welding process to ensure the reliability and stability of welding quality and weld formation.
The key elements influencing laser welding quality are separated into three categories: welding equipment, workpiece condition, and process parameters.
1. Welding equipment
The beam mode, output power, and stability are the most critical parameters for laser quality. The beam mode is the most important determinant of beam quality. The lower the beam mode order, the better the beam focusing capability, the smaller the spot, the higher the power density at the same laser power, and the bigger the weld depth and width.
In general, the basic mode or low-order mode is necessary; otherwise, meeting the criteria of high-quality laser welding is difficult. HGLASER’s laser beam quality and output power stability are now fairly high, and will not pose an issue in laser welding.
The focusing lens is the most critical component influencing welding quality in an optical system. The focal length ranges between 127mm and 200mm. A short focal length is useful for lowering the diameter of the concentrated beam waist point, but it is easily polluted and splashed during the welding process if it is too short.
The higher the absorption rate, the shorter the wavelength; usually, materials with superior conductivity have high reflectivity. Silver has a reflectivity of 96 percent in YAG lasers, aluminum has a reflectivity of 92 percent, copper has a reflectivity of 90 percent, and iron has a reflectivity of 60 percent. The greater the temperature, the higher the linear absorption rate; typically, covering the surface with phosphate, carbon black, graphite, or other materials can boost the absorption rate.
2. Workpiece condition
Laser welding necessitates the processing of the workpiece’s edge, high precision assembly, the spot and weld are tightly aligned, and the original assembly accuracy of the workpiece and spot alignment cannot be modified during the welding process owing to welding thermal deformation. This is due to the tiny size of the laser spot and the narrowness of the welding seam.
In most cases, no filler metal is used. If the gap is too great, the beam can pass through it without melting the base metal or causing noticeable undercut and depression, such as the deviation of the spot to the seam. If it is overly big, it may result in partial fusion or penetration.
As a result, in general, the plate butt assembly gap and deviation of the spot alignment should be less than 0.1mm, and the incorrect side should be less than 0.2mm. Laser welding technology is sometimes unable to be employed in actual production because these conditions cannot be satisfied. To achieve a successful welding effect, the allowed butt gap and overlap gap should be kept within 10% of the sheet thickness.
For maximum results, laser welding needs close contact between the substrates being welded, which necessitates careful tightening of the components. This is difficult to do on thin tab substrates, which are prone to bending misalignment, particularly when embedded in large battery modules or assemblies.
3. Welding parameters
(1) Effect on laser welding mode and welding seam formation stabilization The most essential welding parameter is the laser spot power density, which influences the welding mode and welding seam formation stability as the laser spot power density grows from small to large: Stable thermal conduction welding comes first, followed by mode unstable welding and stable deep penetration welding.
(2) The influence of welding parameters on penetration depth in the deep penetration welding range: in the stable deep penetration welding range, the higher the laser power, the greater the penetration depth, which is about 0.7 power; and the higher the welding speed becomes, the shallower the penetration.
When the focus is in the optimal location under particular laser power and welding speed, the penetration depth is the greatest; when it deviates from this position, the penetration depth drops and even becomes mode unstable welding or stable thermal conduction welding.
(3) Shielding gas influence, the main function of shielding gas is to protect the workpiece from oxidation during the welding process; to protect the focusing lens from metal vapor contamination and liquid droplet sputtering; to dissipate the plasma generated by high-power laser welding; and to cool the workpiece, reducing the heat-affected zone.
(4) Monitorability analysis of each parameter: Of the four welding parameters, welding speed and shielding gas flow are easy to monitor and keep steady, however laser power and focus location might change throughout the welding process and are difficult to monitor. parameter.
Although the laser’s output power is very steady and easy to measure, the laser power reaching the workpiece will fluctuate owing to losses in the light guiding and focusing systems, which are related to the optical workpiece’s quality, age, and surface pollution.
One of the welding characteristics that has a significant impact on welding quality and is the most difficult to monitor and manage is the position of the beam focus.