Uncategorized
From Sheets to Systems: Understanding the Future of Intelligent Sheet Metal Production Lines
Sheet Metal Production Lines: The Intelligent Engine of Metal Processing
In today’s manufacturing landscape, sheet metal processing is widely used across industries such as automotive, home appliances, electronics, electrical systems, and machinery. As market demands for higher product quality, production efficiency, and customization increase, traditional manual sheet metal work can no longer keep pace. This has led to the rise of automated sheet metal production lines. A sheet metal production line refers to a fully automated system that processes metal sheets through a series of operations, including laser cutting, punching, bending, welding, and more. With CNC equipment and digital control platforms at its core, the line reduces manual intervention, enhances consistency, and boosts production rates—making it a key enabler of smart factories and manufacturing upgrades.
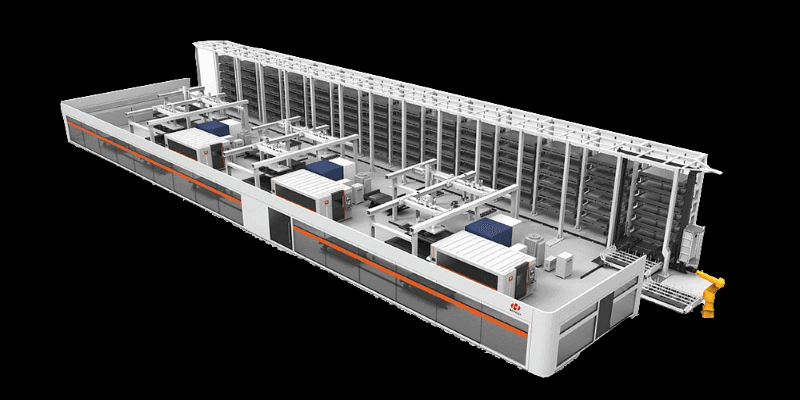
Structure and Core Technologies of Sheet Metal Lines
A modern sheet metal production line typically begins with material storage, where metal sheets are automatically identified and loaded into the processing unit. The sheets are then passed through laser cutting, CNC punching, bending, and welding stages. Finally, an automated sorting system takes over to dispatch finished parts to designated storage. Throughout this process, programmable logic ensures real-time coordination across machines, enabling high-speed data exchange and seamless workflows. Laser cutting is the central operation, favored for its non-contact nature, concentrated energy delivery, and minimal thermal distortion. It has largely replaced traditional shearing and stamping methods, particularly for complex contours and batch production. With intelligent nesting software, laser systems also optimize material usage, reducing scrap rates and lowering costs.
One of the most vital characteristics of sheet metal lines is flexibility. As orders become more diversified and batch sizes shrink, automation at a single workstation is no longer enough. Instead, modular design allows manufacturers to build adaptable production lines that can switch between products or workflows with minimal reconfiguration. Digital control systems act as the “central nervous system” of these lines. Most setups integrate MES (Manufacturing Execution System), ERP (Enterprise Resource Planning), and WMS (Warehouse Management System) platforms, enabling real-time equipment communication, task scheduling, process tracking, and quality control—ultimately forming a closed-loop, data-driven production model.
With the advancement of industrial connectivity and AI, sheet metal lines are evolving toward higher levels of intelligence. Some advanced systems now incorporate IoT sensors to collect real-time data from each station, using AI algorithms to optimize throughput, predict maintenance needs, and reduce energy consumption. Operators can monitor line performance through intuitive dashboards, while digital twin models allow for remote diagnostics, process simulation, and productivity analysis. In practice, intelligent sheet metal lines can reduce manual intervention by more than 70%, increase equipment utilization by over 20%, and significantly cut per-unit energy costs—becoming a key driver of competitive advantage.
Some Chinese companies, such as HGTECH, have built early capabilities in this space, delivering solutions that combine flexible cutting, automated loading/unloading, and centralized control. In select applications like automotive structural parts and electromechanical enclosures, their sheet metal systems have achieved impressive results. However, it’s important to note that there is no one-size-fits-all solution—the layout and components of each line must be tailored to the specific needs of the customer and the industry. That’s why modular, reconfigurable line design remains a central theme in system development.
The Future of Sheet Metal Lines: Green, Smart, and Global
The future of sheet metal production lines will be shaped by three major forces: green manufacturing, intelligent transformation, and global-local integration. First, under increasing environmental regulations, production lines will place greater emphasis on energy efficiency and emission control. Equipment will be expected to meet higher energy standards, while systems for fume filtration, scrap handling, and heat recovery will become standard components. Second, smart technologies will continue to expand their role. From real-time monitoring to full-process traceability and AI-based adaptive machining, future sheet metal lines will not just produce parts—they’ll act as intelligent, learning systems that support decision-making and continuous improvement.