Uncategorized
Laser Tailor Welding Technology Ushers in a New Era of Automotive Door Ring Manufacturing
The door ring is a vital structural element in vehicle design, connecting the door to the body-in-white and forming the first line of defense during side impacts. Traditional manufacturing relies on welding multiple stamped steel parts, a process that introduces complexity, deformation, and inconsistency.
Laser Tailor Welding offers a transformative solution by using high-energy laser beams to precisely weld steel sheets of different thicknesses and materials in a single pass. This eliminates stress concentration caused by spot welding and achieves ultra-narrow weld seams—less than 1 millimeter wide. The technology reduces part count by over 70 percent and boosts structural rigidity by up to 30 percent, creating a lighter yet stronger door ring that enhances both safety and energy efficiency in collisions.
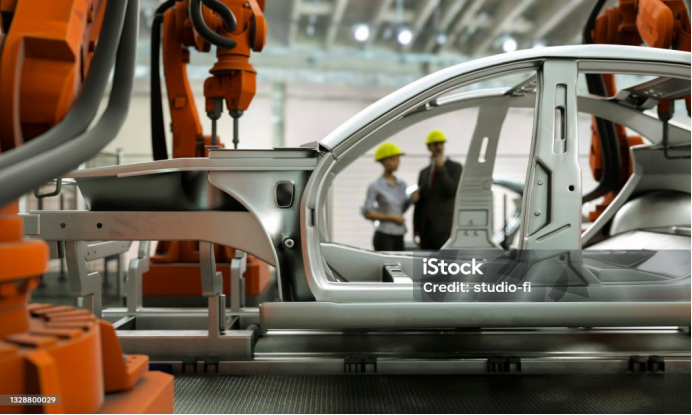
The Core Advantages of Laser Tailor Welding
Laser Tailor Welding excels in automotive applications due to its high energy density—reaching up to one million watts per square centimeter—and millisecond-level processing speed. This allows rapid, complete fusion of metals with minimal heat input. A defining advantage is the ability to limit the heat-affected zone to less than 0.5 millimeters, preserving the surrounding material’s properties and ensuring dimensional accuracy. In door ring production, where both strength and lightweight design are crucial, this technology enables seamless joining of sheets with different thicknesses.
For instance, a 1.2 millimeter inner panel can be continuously welded to a 1.8 millimeter reinforcement section in crash-critical areas. The process is digitally controlled, ensuring precise weld penetration across varying zones and reducing residual stress. Moreover, Laser Tailor Welding supports joining dissimilar materials—such as aluminum-silicon coated steel, hot-formed boron steel, and other advanced high-strength steels. This opens up possibilities for targeted structural functions, allowing corrosion-resistant zones and energy-absorbing regions to be integrated into one assembly. Unlike traditional spot or arc welding, this technique eliminates overlapping flanges, reducing overall part weight while increasing fatigue resistance and mechanical performance.
Toward Greener, Smarter Manufacturing
As demand for lightweight electric vehicles continues to grow, laser-welded door rings are expanding into mainstream models. The technology supports sustainable manufacturing by generating no spatter, eliminating fixture wear, and minimizing material waste. With high-power laser adoption—12 kilowatts and above—the industry is moving rapidly toward fully automated, intelligent, and precision-driven vehicle body production.
About HGTECH
HGTECH is the pioneer and leader of laser industrial application in China, and the authoritative provider of global laser processing solutions. We comprehensively layout the construction of laser intelligent equipment, measurement and automation production lines, and smart factories to provide an overall solution for intelligent manufacturing.
We deeply grasp the development trend of manufacturing industry, constantly enrich products and solutions, adhere to exploring the integration of automation, informatization, intelligence and manufacturing industry, and provide various industries with laser cutting systems, laser welding systems, laser marking series, laser texturing complete equipment, laser heat treatment systems, laser drilling machines, lasers and various supporting devices The overall plan for the construction of special laser processing equipment and plasma cutting equipment, as well as automatic production lines and smart factories.