Projects
Analysis Of 3D Five Axis Laser Cutting Technology
In automobile manufacturing, producing ordinary cars requires 1000-1500 sets of stamping molds, accounting for approximately 40% of the molds required for vehicle production. The traditional direct stamping processing method has caused huge losses to the grinding tools. During the processing, frequent repairs or even replacements are required, resulting in low efficiency and high cost.
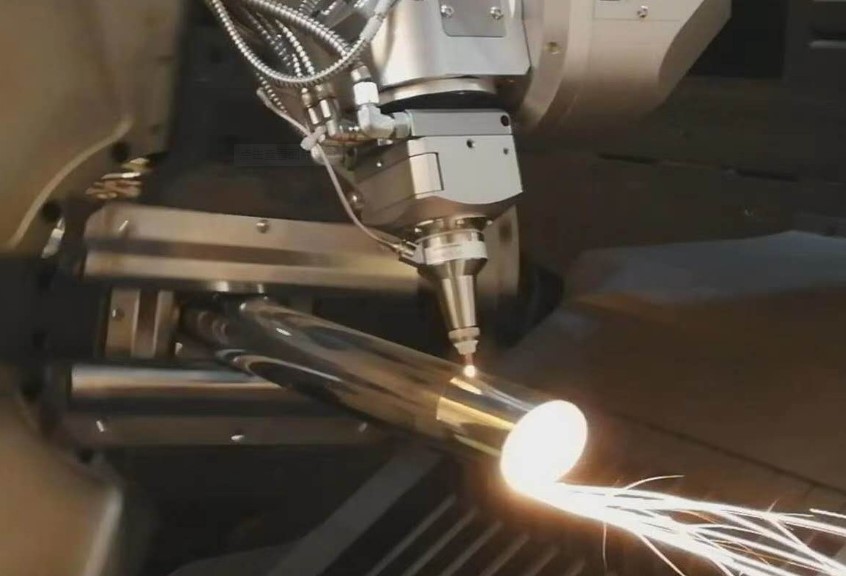
Laser, as an advanced processing method, can provide the minimum heat affected area and local deformation. The non-contact processing method has no force on the workpiece, the workpiece has no mechanical deformation, the tool has no machining wear, and the cutting ability is not affected by the cutting Hardness. Especially for automobile Thermoforming parts, the yield strength of high strength steel can reach 1500MPa, and traditional stamping is almost impossible to process. 3D laser cutting has become the most effective processing method, and has been applied more and more in the processing process.
With the development of light vehicles, energy conservation, environmental protection and safety have become the factors that must be considered in the process of Automotive design and production. Hot stamping ultra-high strength steel plates can reduce fuel consumption and increase important structural components such as B-pillars, A-pillars, front/rear bumpers, front/rear collision beams, thresholds, floor channels, roof longitudinal beams, roof side beams, window reinforcement bars, door panel reinforcement bars, lateral support frames, suspension fixing frames, longitudinal bearing beams, etc., suitable for 3D laser cutting. Compared to 2D laser cutting, 3D laser cutting machine tools and programming are more complex, but also involve auxiliary equipment such as tools. Body stamping laser cutting not only ensures cutting quality and accuracy, but also considers cutting efficiency. Taking China’s 3D five axis laser equipment as an example, share some skills in the cutting process.
1) Reliable rough workpiece
During the forming process, formed components may experience problems such as breakage, flipping, wrinkling, and rebound, resulting in a small amount of deformation and dimensional errors. The 3D five axis laser cutting machine can automatically compensate for these errors through a floating axis to ensure normal processing. If stamping parts with large dimensional errors are processed, the cutting quality and accuracy may be unstable, or even the 3D laser cutting head may collide, damaging the nozzle and Filter (aquarium)#Materials suitable for aquarium filtration. In order to achieve stable cutting quality and accuracy, qualified blank parts are required. A good mold is a prerequisite for stabilizing blank parts, and timely repair of worn molds to ensure the pressure of qualified parts.
2) Reliable tooling
The tool must be able to match the workpiece well and add light barriers in some laser cutting areas to prevent laser burning or burning the workpiece on the other side of the workpiece. For most multi production lines, special simulation tools are mostly used, which have good accuracy, small shape, good stability, and can be reused. Electric control fixtures and workpiece detection devices can also be installed on the tools, which helps to ensure the continuous and stable production of the equipment. Although grid temporary tools lack certain reliability and stability, they are simple, fast and low-cost, especially suitable for processing in Low rate initial production industry, and widely used in mold manufacturing and even some hot forming line industries.
3) Reasonable programming
Arrange a reasonable cutting sequence and rotate and swing the cutting head as little as possible to ensure complete cutting. Strive not to turn back on the main path, which can greatly save cutting time and improve production rhythm.
4) Optimize cutting actions
The cutting height is optimized, and the empty travel adopts a frog jump action, fully utilizing the effective stroke of the floating shaft. While ensuring the safe passage of the cutting head, it is as close to the surface of the workpiece as possible to save empty travel time.
5) Cutting parameters
The factors that affect cutting quality include parameters (power, speed, air pressure, focus), gas quality (usually using air or nitrogen cutting, requiring timely maintenance of air compressors and filtration devices to ensure stable cutting gas quality), intact nozzles, high tracking stability, and clean optical lenses.
In addition to the above factors, the cutting angle also has a significant impact on 3D laser cutting. Generally speaking, in flat plate machining, the laser cutting head is always perpendicular to the surface of the workpiece. However, in three-dimensional cutting, due to the workpiece being a three-dimensional irregular part, if the cutting head is always perpendicular to the surface of the workpiece, it may collide with the workpiece. We need to modify the angle of the cutting head and cutting surface in real-time to ensure the safety of the cutting head.
When the cutting enters the corner, the system speed will slow down. Therefore, if the same parameters are cut, it will lead to excessive combustion and suspended slag. In order to achieve good cutting quality, different parameters and straight lines AUTOBOT3015-3300W will be used.
The 3D five axis laser cutting machine can cut 1.2mm using a hot formed part as an example. Different parameters can be set according to the complexity of the workpiece to ensure consistent cutting quality.
The appearance of the overall door loop greatly improves the safety of cars. This large shaped component requires a larger three-dimensional five axis laser cutting machine. The general standard 3D five axis laser cutting machine has an amplitude of 3 * 1.5m, which can meet the laser cutting needs of the vast majority of automotive forming components. This type of overall door ring can be larger, such as 4 * 2m and 4 * 2.5m large format 3D five axis laser cutting machines that achieve overall processing without the need for secondary positioning, with better reliability and stability.
In recent years, China’s hot stamping forming technology and hot stamping production lines have developed rapidly, and market demand has grown rapidly. The cutting efficiency of the 3D and 5-axis laser cutting equipment produced by Huagong Laser is comparable to that of imported equipment, with a price only accounting for about 70% of the imported equipment. It has the advantages of short delivery time and low service cost. Compared with imported equipment, the localization of core unit cutting heads and light sources has saved over 1 million yuan, while the hot forming line requires 4-6 automotive hot forming 3D five axis laser cutting machines. A single line can save users nearly 1 million equipment investment costs. At present, it has been purchased in large quantities by Thermoforming enterprises.
The AUTOBOT3015 three-dimensional five axis laser cutting machine mainly solves the cutting and edge repair problems of formed components. Its characteristics are high precision, fast speed, good dynamic performance, and equipped with a high-performance rotating workbench, which can meet the high rhythm requirements of the automotive industry.
Product features:
- Stability: Adopting a gantry dual drive structure, it has good stability and can ensure long-term high-speed, high-precision stability
- High efficiency: The maximum synthesized positioning speed is 170m/min, the maximum synthesized acceleration is 1.7G, and the rotating workbench can complete a single displacement in 3s.
- Safety: The safety protection of the machine tool complies with CE international safety standards.
- Cost performance: The performance is no less than that of imported equipment, with short delivery time, low cost investment, and low maintenance costs.