Projects
Application Of Laser Cleaning Technology In the Field Of Silent Tire Texturing
Laser cleaning is a surface treatment technology that obtains a high-energy laser beam through an optical system and removes attachments on the substrate surface through vibration, ablation, and other actions. Laser cleaning has many advantages, such as: laser has high energy characteristics, which can effectively remove micron and nanoscale particles; Laser cleaning has no mechanical contact, does not cause unexpected mechanical damage to the cleaning object, and does not have wear issues; laser cleaning does not require chemical solvents, eliminating the waste liquid treatment steps, while avoiding unnecessary chemical corrosion to the equipment, and eliminating the need for drying operations after cleaning; The waste materials from laser cleaning are mainly solid debris and powder, which are small and easy to handle, and pose little harm to the environment and human beings; Compared to ultrasonic cleaning, its noise is lower; laser cleaning allows selective cleaning; Using a fiber laser can achieve remote operation; laser cleaning can be operated in a variety of ways, both manually and automatically.
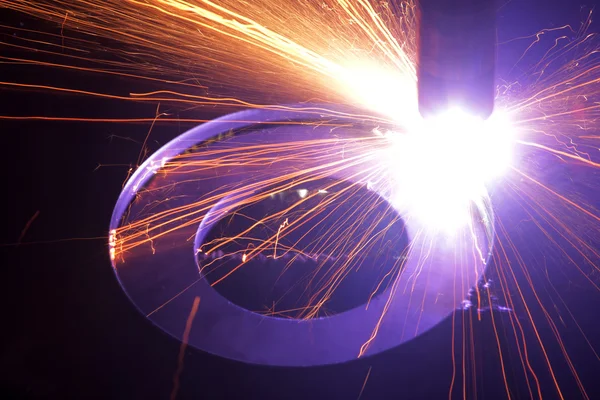
Due to the above advantages, laser cleaning has been rapidly applied in many production fields, such as removing glue from patterns inside molds, removing dust and dirt from ancient buildings and stone cultural relics, removing rust from the surface of ship plates, removing paint from aircraft metal skins and composite components, and removing paint from high-speed iron surfaces. It is necessary to explore the application of laser cleaning technology in petrochemical industry and provide technical reserves for the replacement and upgrading of traditional cleaning technologies, with a broad prospect.
New energy vehicles are quieter than conventional internal combustion engine vehicles, and the development of new energy vehicles also puts forward stricter requirements for tire noise control. New energy vehicle tires can be better adapted to the needs of new scenarios by improving their rubber formula, tire height to width ratio, tire volume, tread material, and tread pattern.
As a “green” cleaning process, laser cleaning technology has a good application in the production and manufacturing of silent tires. It uses a focused high-energy laser beam to irradiate the surface of organic polymer materials, causing physical and chemical changes on the material surface, thereby changing its performance. It can effectively improve the tire quality and production process, improve the matching between the tire and the vehicle body, and improve the overall performance of the entire vehicle. By coating the inner wall of the tire with a soft solid colloidal polymer composite material, the functions of explosion prevention, puncture prevention, and leakage prevention are achieved. At the same time, a layer of polyurethane sponge is pasted on the surface of the leakage prevention adhesive to achieve sound insulation and insulation, and the mute effect of absorbing cavity noise is achieved.
Laser cleaning can effectively remove the residual isolation agent on the inner wall of the tire, improve the coating of composite materials and the adhesion of polyurethane sponge. The cleaning process requires no consumables, does not cause damage to the tires, has high efficiency, and good consistency, enabling automated cleaning.
Evaluate the sample by selecting pulsed laser equipment and formulating a reasonable process flow. The surface tension values under different parameters were obtained through the Dyne pen test. The results show that different process parameters (laser energy density, processing efficiency) can have an impact on the surface tension of the inner wall of the tire, and it is necessary to reasonably formulate process parameters for the production process of silent tires. Through testing, the laser cleaning is uniform and meets the requirements for substrate damage. After cleaning, the internal friction coefficient increases by>37 mN/m, and the surface tension reaches 40 dyne/cm.
Use a roughness tester to test the surface after laser treatment. The area is S1-S4, corresponding to different process parameters. The test standard is ISO 1997, the curve is R, and the filter is GAUSS. The results show that different parameters have different degrees of impact on the surface roughness. In the figure, the roughness in the S3 area is the largest, consistent with the Dyne pen test results, and the laser treatment greatly increases the surface roughness.
When observed at 1000 times, it was found that a large number of commonly distributed small pits appeared in the area irradiated by the laser, with particle sizes reaching the micron level. When the laser strikes the surface of the material, it will destroy the rubber chain structure, producing this irregular concave feature, and improving surface roughness.
The technology of laser cleaning tire molds has been widely used in the tire industry. Although the initial investment cost is high, the benefits obtained by saving standby time, avoiding mold damage, operating safety, and saving raw materials will be quickly recovered.
About HGSTAR: HGSTAR is is a sub-brand of HGTECH.HGTECH the pioneer and leader of laser industrial application in China, and the authoritative provider of global laser processing solutions. We have comprehensively arranged laser intelligent machine, measurement and automation production lines, and smart factory construction to provide overall solutions for intelligent manufacturing.