Projects
Classification Of Laser Composite Welding
Laser self fusion welding
Laser self fusion welding: It belongs to deep fusion welding and is mainly used for top covers, side walls, car doors, etc. Laser remote welding: using robots and galvanometers for remote beam positioning and welding. Its advantages lie in significantly shorter positioning time and higher efficiency compared to traditional laser processing. Currently, it has gradually been promoted in Europe and America.
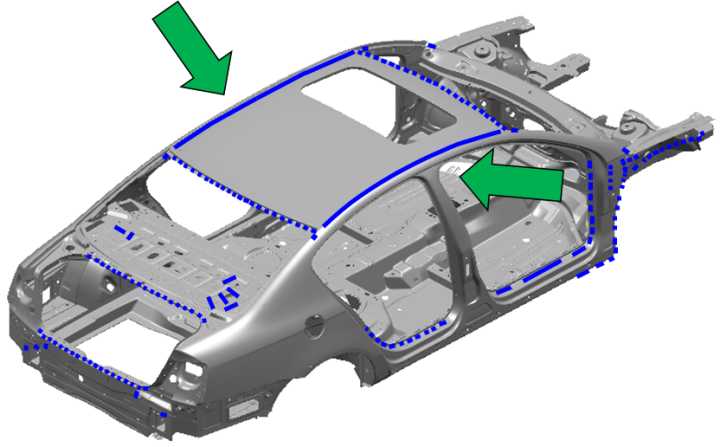
Laser self fusion welding refers to two or more parts that need to be welded, which melt, cool, and then condense into a whole to achieve the purpose of welding. This welding method does not require the addition of flux during use, and the entire process relies on the physical properties of the workpiece itself to achieve the goal of fusion. When the laser power density reaches a certain value, the temperature on the surface of the workpiece rapidly rises and reaches its boiling point in a short period of time, causing the metal to vaporize and form a slender hole. When the recoil pressure of the metal vapor reaches an equilibrium value with the surface tension and gravity of the liquid metal, the elongated hole no longer deepens, ultimately forming a stable and deep hole. When the small hole is closed, the weld seam is formed, and laser deep penetration welding is completed.
In the process of automobile manufacturing, laser self fusion welding is mainly used in body assembly welding, tailor welding, and component welding. According to the type of welding seam, it can be classified into multiple types, such as single straight seam, complex straight seam, non straight seam, etc. Among them, the production process of single welding seam type is relatively simple, so its application range is relatively wide.
Laser hybrid welding
Compared with pure laser welding technology, the use of laser hybrid welding technology can greatly improve the connection ability of gaps in sheet metal parts, allowing enterprises to more fully utilize the process stability of arc welding during high-speed laser welding.
The use of laser welding can also reduce stamping and assembly costs in the manufacturing process of automobile bodies, shorten production cycles, reduce the number of parts, and improve the integration degree of the body. Laser welding of components, with almost no deformation at the welding site, is fast and does not require post weld heat treatment. Currently, laser welding of components is widely used, commonly found in transmission gears, valve tappets, door hinges, etc.
Laser arc composite welding
Arc welding utilizes the electrical phenomenon of “arc discharge”, which refers to a type of gas discharge phenomenon that generates current in the air. Applying voltage to two mutually independent electrodes in space disrupts the insulation of the air, generates current between the two electrodes, and emits strong light and high heat. The arc shaped light generated at this time is called “arc”, and the welding method of using arc heat as a heat source is “arc welding”. Specifically, it is divided into submerged arc welding, plasma welding, and gas electric vertical welding (EGW).