Projects
Groove Cutting Technology In Detail
Introduction
Laser cutting technology plays an important role in groove processing due to its high precision and efficiency. Below, we will provide a detailed introduction to the specific cutting techniques for different types of grooves.
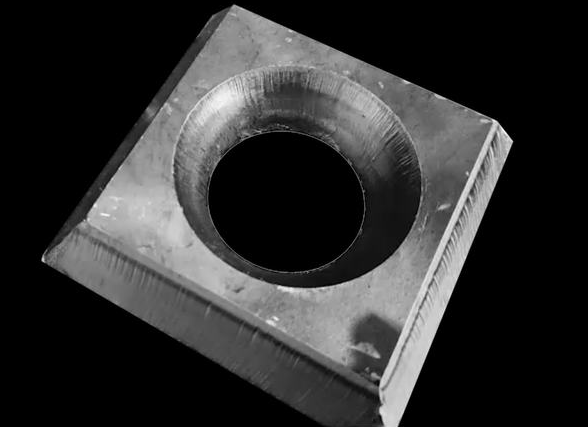
Detailed explanation of groove cutting process
Firstly, let’s explore the cutting technology of V-shaped grooves. When processing V-shaped grooves, laser cutting equipment precisely cuts the desired groove shape by adjusting the angle of the cutting head and the focusing position of the laser beam. The high-energy focusing characteristics of the laser beam make the cutting process fast and accurate, while reducing issues such as thermal deformation and oxidation, ensuring the quality of the groove. In addition, laser cutting can be flexibly adjusted according to the thickness and properties of the material to meet the needs of different welding processes.
Next is the cutting technique for U-shaped grooves. Compared to the V-shaped groove, the U-shaped groove has a deeper opening and smoother transition. In order to achieve this groove shape, laser cutting equipment adopts special cutting programs and cutting head designs. During the cutting process, the laser beam moves at a specific angle and speed, gradually cutting out the contour of the U-shaped groove. At the same time, the laser cutting equipment is also equipped with a precise control system to ensure the accuracy and consistency of cutting.
In addition to V-shaped and U-shaped grooves, laser cutting can also process other shapes of grooves. For example, the cutting technology of “J” groove requires laser cutting equipment to perform multiple cuts and movements during the cutting process to form a shape with a narrower bottom and wider opening of the groove. This requires cutting equipment to have a high degree of flexibility and accuracy. In addition, the cutting techniques for complex grooves such as “X” and “K” are more complex, requiring laser cutting equipment to perform precise operations based on preset cutting paths and parameters to achieve precise shaping of grooves.
In the process of laser cutting, it is also necessary to pay attention to some key factors to ensure the quality of the groove. Firstly, the control of laser power and cutting speed needs to be adjusted according to the properties and thickness of the material to avoid overheating or incomplete cutting. Secondly, the selection and use of cutting gases can promote the smooth progress of the cutting process, reduce thermal effects and oxidation. In addition, maintenance and upkeep of the cutting head are also important measures to ensure cutting quality and extend equipment life.
Epilogue
Overall, different types of groove cutting techniques have their own characteristics and need to be selected based on specific application scenarios and needs. With the continuous progress of technology and the expansion of application fields, laser cutting will continue to bring more innovation and breakthroughs to the mechanical processing and manufacturing industry in the future.