Projects
The Development And Application Of Integral Laser Welding Hot-forming Door Rings
With the increasingly fierce competition in the automobile market, consumers’ demands for vehicles are also rising, especially in terms of fuel economy and overall vehicle performance. Therefore, automobile body design becomes particularly important., which needs to ensure sufficient strength and safety performance while avoiding excessive weight at the same time. This article introduces laser welding and hot-forming technology. Through optimization of materials and thickness, the application of laser-welding door rings enables a light weight of vehicle, as well as achieves an optimal collision performance and material utilization.
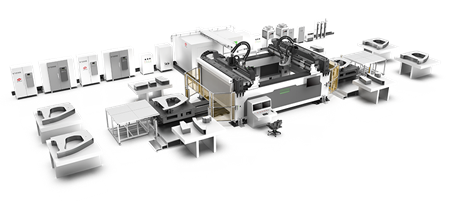
The hot-forming door ring is a single component that combines the conventional A-pillar reinforcement panel, B-pillar reinforcement panel, side reinforcement panel, and sill reinforcement panel into one using hot-forming steel (22MnB5). In today’s door ring technology, laser welding is more widely used instead of resistance spot welding (referred to as spot welding) to connect the components together. The position and quantity of welding seam, as well as the material thickness of each section, can be flexibly set according to performance and quality requirements, enhancing design flexibility.
In automobile design, reinforcing the door opening area is particularly crucial for minor offset collisions. This is because the front door opening area is the survival area for the front seat occupants, with only one door separating them from the collision. Therefore, it is necessary to ensure that the area where the door ring and the human body overlap has a high strength to prevent fractures from impacting the occupants, while also ensuring that the door can open in the event of an accident. Additionally, certain areas beneath the door ring require high toughness to absorb collision energy. Based on these principles, the entire door ring system needs to have a high strength, stiffness, and toughness. For metal materials, high strength and high toughness are generally not simultaneously achievable. Therefore, using laser welding technology to combine materials with different strengths and toughness is a very suitable choice.
Meanwhile, different thicknesses of steel plates can be welded together to achieve a good weight reduction effect by reducing the thickness of partial steel plates. However, reducing the thickness of the steel plates will inevitably decrease its stiffness. At this point, it is necessary to consider how to ensure the original stiffness requirements of the vehicle body. The integral laser welding hot-forming door ring combines several parts together to form an integral component, offsetting the stiffness decrease caused by the thinning of the steel plates. Additionally, if inadequacies in strength and stiffness are identified during the inspection process, partial reinforcement can also be used to enhance the strength and stiffness of specific places.
The forming process of the door ring includes uploading, laser welding, hot stamping forming, and laser cutting. Common materials for hot stamping include bare plate and aluminum-silicon coated plate. Laser welding of bare plate does not require additional processing. While before the laser welding of aluminum-silicon coated plate, some of the coating needs to be removed to avoid the aluminum elements in the coating affecting the performance of the welding seam.
After conducting 25% offset collision and MDB (Moving Deformable Barrier) collision simulation experiments on the door rings using traditional stamping welding process and the door rings using hot-forming laser welding, we find that when colliding, the intrusion and deformation of the car body using laser welding are relatively small, demonstrating superior safety performance.
Considering process, costs, and performance,the integral laser welding hot-forming door ring demonstrates its advantages and competitiveness in all aspects. It ensures the strength and stiffness of the vehicle body, meeting collision requirements. In terms of process, the door ring utilizes hot stamping and laser welding technology. Laser welding technology provides high precision and controllability, enabling the precise dimensions and shapes of the door ring, ensuring each door ring meets specification requirements. The combined use of these two technologies improves the forming quality of the door ring, while also achieving a light weight of the vehicle body. In terms of cost, laser welding is fast and efficient, suitable for mass production, reducing costs in design and manufacturing.
Whether it is a gasoline vehicle or a new energy vehicle, considering factors such as comprehensive performance, cost, and process, high-strength steel remains an important part of the future vehicle body material selection. The integral laser welding hot-forming door ring, as an important lightweighting method for steel components of the vehicle body, has gradually expanded its application from the initial SUV models to diverse models such as sedans, MPVs, and pickups. The application areas have also evolved from the initial A-pillar to B-pillar door rings, gradually progressing to B-pillar-C-pillar door rings, and even to A-pillar-B-pillar-C-pillar integral door rings. It has also gradually developed from only being used on initial outer panel door ring to the application of both inner and outer double door rings. In the future, with the increasingly stringent requirements for carbon emissions and safety performance, the application of integral laser welding hot-forming door rings will become more popular.