Projects
Observation | Application of Laser Processing in Automotive Manufacturing
The automotive industry is one of the largest applications of laser material processing. According to data from McKinsey’s Future Mobility Center, the automotive sector accounted for approximately 7% of the EU’s GDP in 2019.
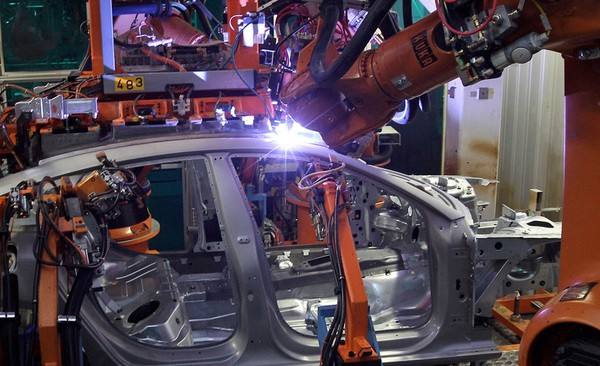
At present, the supply chain restrictions caused by the COVID-19 epidemic have not been completely lifted, and the automobile production has not yet recovered to the pre epidemic level. However, the growth of the European automotive industry is showing a continuous upward trend. In the first nine months of 2022, the EU produced nearly 8 million passenger cars – an increase of 5.8% compared to the same period in 2021.
For a long time, lasers have played an important role in optimizing automotive manufacturing. For most vehicles, almost every area (whether internal or external) contains laser treated components. Laser processing provides excellent versatility and repeatability, and a single laser device can process various automotive components with extremely high accuracy and speed.
Laser equipment is a highly automated, low-cost, and low-maintenance tool that can be used in automotive production lines for cutting, welding, brazing, marking, surface treatment, drilling, 3D printing, and cladding applications. Laser can be used to process various complex 2D/3D automotive parts, which may be made of materials such as metal, plastic, glass, rubber, and textiles.
White body manufacturing
One of the main stages of laser based automotive production, especially in cutting, welding, and brazing, is known as body in white (BIW) manufacturing – this is the stage where the steel frame components that make up the basic structure of road vehicles are cut and connected together.
The body, doors, and frame components are usually made of different grades of pressure quenched steel, such as stainless steel, low-carbon steel, high-strength steel, high and low steel, or galvanized steel. Aluminum can also be used for certain components, and due to its lightweight, it can help improve the fuel economy of vehicles. According to statistics, the thickness of most steel body panels is approximately 0.6-0.8 millimeters, while the thickness of aluminum body panels is generally 0.8-1.8 millimeters.
Laser welding has been used in body in white manufacturing for decades. In 1991, Volvo became the first European automaker to introduce it into the main production line of the body workshop. BMW also adopted this technology at about the same time, using this technology to connect roof components on its sub assembly line.
Laser brazing can also be used for body in white components, with the difference being that welding mainly involves melting the substrate of two connecting components, while brazing involves melting the filler metal as it flows between the connecting components to form a bond. Laser brazing is commonly used at the connection between car doors and roofs to form a seamless, high-strength bond, and can be easily coated.
Due to the low operating cost, most of the laser welding/brazing tasks in BIW manufacturing can be completed by fiber laser. They can be used to form high-quality welding between similar and different materials, such as avoiding defects such as cold cracking, porosity, and splashing when welding steel and aluminum. In addition, fiber lasers can be easily integrated into robot technology in automotive production lines, as their beams can be transmitted along the robotic arm to the processing head through flexible fibers.
Laser cutting, trimming, and perforation have always been a part of the manufacturing of white body. As early as 1983, Austin Rover Group installed a five axis system to trim pre produced body panels. In addition, columns, frames, antenna holes, bushings, and holes for fixing external components are common components that can be cut or perforated with laser. Fiber lasers are often the preferred tool for this application.