Projects
Application of Laser Processing in the Production of Electric Vehicle Batteries and Motors
Motor Vehicles are Being Electrified
In recent years, with the enhancement of environmental awareness and the improvement of technological level, the automotive manufacturing industry is facing tremendous changes and challenges. In this context, electrification has become one of the most important development trends in the automotive manufacturing industry.
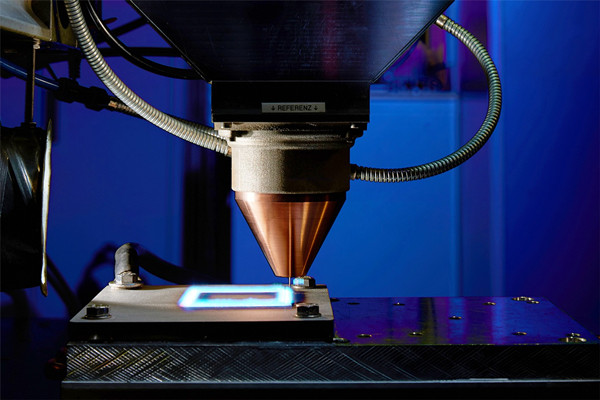
Laser Processing Has a Wide Range of Applications In the Field of Electric Vehicles
The laser industry has responded to this call, and in the past decade, many light sources and systems have emerged specifically for this application field. In the manufacturing of electric vehicle batteries alone, lasers have over 30 applications. For example, welding lasers can be used to weld the foil and busbar of battery cells, seal the battery casing, weld labels to the battery casing, and weld fixtures in the motor. They can also be used to cut copper anodes and aluminum cathode foils for batteries.
In new laser solutions, especially blue (450nm) and green (515nm) lasers, they excel in handling many copper components used in batteries and motors. This is because their visible light wavelengths are particularly well absorbed by copper (blue absorption 65%, green absorption 40%), while the absorption rate of infrared fiber lasers (1070nm) is only 5%.
Laser Processing Has Many Advantages
Visible laser can therefore avoid the challenge of using higher fiber laser power to overcome material reflectivity, which may lead to welding defects such as voids and splashes, increasing electrical resistivity. Although fiber lasers can be equipped with technologies such as variable beam modes or swinging welding heads to help alleviate these defects, it is evident that lasers can achieve high-quality copper welding at lower power levels without the need for these measures.
Blue laser is also an ideal choice for welding different metal combinations, such as copper and stainless steel or copper and aluminum. In the past, due to the reduction of the integrity of welded joints due to the generation of intermetallic phases, combinations such as copper and stainless steel were often difficult to weld using fiber lasers.