Projects
Ultra Large Laser Cutting Machine To Help Manufacturing
Introduction
Laser cutting technology, as one of the high-tech industries in modern manufacturing, is often applied in conjunction with the raw materials of sheet metal in the manufacturing industry. The steel structure industry, shipbuilding industry, automobile body manufacturing, mining machinery industry, rail transit industry, iron tower industry, agricultural equipment and other industries have particularly obvious applications for sheet metal cutting. In order to improve processing efficiency, it is very important to rely on high-power and high configuration large format laser cutting machines. The advantage of ultra large laser cutting machines is that they are not afraid of long and thick plates, and can achieve maximum efficiency and top cutting quality.
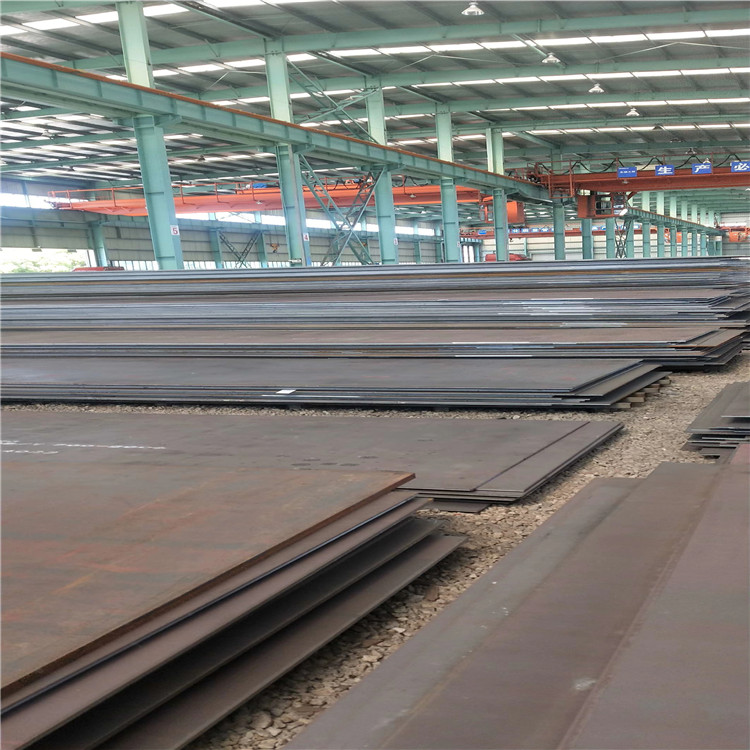
Four major advantages of large format laser cutting machines
The large format laser cutting machine has the advantages of high electro-optical conversion efficiency, good beam quality, high energy density, wide modulation frequency, high reliability, and long service life. Therefore, the use of large format laser cutting machines for cutting ships, tracks, and other plates mainly has four major advantages:
(1) Narrow cutting seam, high precision, good roughness of cutting seam section, small taper, material cutting usually does not require subsequent processing
(2) Laser cutting, due to its high energy density, high cutting efficiency, and short thermal action time, has a small heat affected zone, small thermal deformation, and low thermal stress, making it particularly suitable for cutting thin plates
(3) Laser has a high degree of automation, can be fully enclosed for processing, is pollution-free, has low noise, and is safe and environmentally friendly
(4) The optical system and control system are stable and reliable, with low maintenance costs and stable cutting quality
Limitations of traditional cutting techniques
Mainly including traditional cutting methods such as water cutting, flame and plasma cutting, which have certain thickness limitations and cannot guarantee cutting accuracy. The cutting effect of medium and thick plates is not very good, and most require secondary processing; The traditional cutting method has a certain range of cutting width, and if it exceeds a certain size, it cannot be operated and needs to be cut separately. It cannot achieve the overall processing of ultra long and ultra large size parts, and the efficiency is not high. Traditional cutting methods often contain harmful gases such as smoke and dust during the cutting process. Environmental protection always falls short of the standard range, resulting in safety hazards for operators and inadequate inspections by environmental protection departments, which consumes more manpower and material resources.
Summary
With the development of the times and the continuous improvement of manufacturing technology, the demand and design of manufacturing materials have also changed with the changes of the times. Therefore, large-area laser cutting opportunities have been applied to the air vents of thick plates in large-area cutting, giving them a trend to rise with the wind!