Projects
Advantages of Laser Cleaning Application in Electronic Components
During the use of electronic circuit boards, small particulate pollutants attached to them can cause short circuits or performance degradation in integrated circuits, and even damage components. Traditionally, water washing and ultrasonic cleaning methods are used, but water washing cannot remove particles of several microns, and ultrasonic waves are prone to damage components. With the development of laser technology, laser cleaning technology was born. After a large number of tests, laser cleaning has been proven to be the best method for cleaning electronic components at present, and has been widely used in the cleaning of electronic masks.
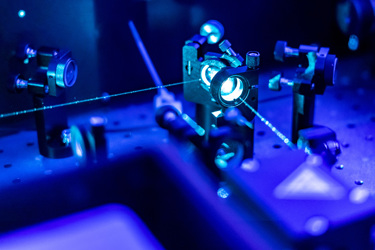
Small pollutants on electronic circuit boards can reduce electronic efficiency and cause damage to electronic circuit boards. With the development of science and technology, semiconductor industry and microelectronic devices are becoming smaller and smaller, and the particles that need to be cleaned are becoming smaller and smaller, making cleaning difficult. Traditional water cleaning and ultrasonic cleaning have their own shortcomings. Laser cleaning brings new hope and becomes the best cleaning method.
In the cleaning of electronic components, the substrate material is mostly semiconductor, and the pollutants that need to be cleaned are mostly sulfur, copper, tungsten, silicon dioxide, rubber particles, etc., with dimensions ranging from tens of nanometers to hundreds of microns. After determining the substrate material and contaminants, it is also necessary to accurately select other laser parameters. Before cleaning operations, it is necessary to clarify these technical parameters to ensure the cleaning effect. Including: laser energy density, laser beam‘s wavelength, pulse width, pulse number, laser incidence angle, etc.
Polyimide film is an important material in electronic components. It is a dielectric material for the internal link structure of multilayer packaging films for high-speed and high-density electronic components. However, it is often covered with some particulate pollutants, including titanium particles, chromium particles, tungsten particles, nickel particles, etc. These pollutants need to be cleaned to ensure the normal operation of the polyimide film. The laser derusting machine company once conducted an experiment to clean polyimide films. Using an excimer laser, a laser with a wavelength of 235 nanometers was selected, with a pulse of 20 ns and a laser energy density of 80 mj/cm2. Using an automated robot operation method, the cleaning efficiency was extremely high. After cleaning, it was found that the cleaning effect was excellent. Using a spectrometer, it was detected that the pollutant removal rate was above 95%, which had reached the required standard and the cleaning efficiency was high. “Why not 100% decontamination? Why is there still 5% left? Can’t it be removed?” “Indeed, there are still 5% left that cannot be removed, but this does not mean that it cannot be removed. The main reason is time and efficiency. In a complete decontamination process, 95% can be removed within 50% of the time, and the remaining 5% can be removed within 50% of the time. In actual operations, cleaning efficiency and cleaning cost are more important.” This indicates that there is a certain gap between theory and practice, In practical applications, there is always a delicate balance among efficiency, effectiveness, and cost. Generally speaking, ordinary electronic components can remove 95% of the pollutants, which is already an excellent cleaning effect.
There are many applications of laser in the cleaning of electronic components, such as the cleaning of electronic circuit boards, silicon wafers, integrated circuits, soft circuits, and photoelectric devices. With the development of science and technology, these materials have improved integration, increased pins, and smaller holes. Traditional cleaning methods are difficult to work effectively. Laser cleaning is highly accurate, easy to automate, and parameters are adjustable The advantages of high cleaning efficiency effectively remove dust, grease, oxides, and other particles from the surface of electronic components, effectively improving the durability of electronic components. Laser cleaning provides an effective and reliable technology for devices in the microelectronics industry that are small in size and difficult to clean with fine particles. At the same time, laser cleaning does not have any wear and corrosion on the substrate material, and meets environmental requirements. It can be operated in a narrow space, which is unparalleled by any other cleaning process.
Laser cleaning meets environmental requirements and sustainable development needs. As the cost of laser cleaning becomes lower and lower, laser cleaning of electronic components is accepted by more enterprises. Before 2016, the cost of laser cleaning electronic components was 20 times that of traditional water and chemical cleaning. With the development of laser technology and significant price reductions in laser cleaning equipment in recent years, the cleaning cost is now close to traditional costs, and prices are continuing to decline.
About HGSTAR: HGSTAR is is a sub-brand of HGTECH.HGTECH the pioneer and leader of laser industrial application in China, and the authoritative provider of global laser processing solutions. We have comprehensively arranged laser intelligent machine, measurement and automation production lines, and smart factory construction to provide overall solutions for intelligent manufacturing.