Projects
Application of Laser Cladding in Chemical Industry
Laser cladding uses a high-energy laser as a heat source and alloy powder as a cladding material. By irradiating the alloy powder with laser beam and simultaneously acting on the surface of the workpiece, it quickly melts to form a molten pool, and then rapidly solidifies to form a dense, uniform, and controllable thickness metallurgical bonding layer. Improving the wear resistance, corrosion resistance, high temperature resistance, and oxidation resistance of metal parts can not only restore the use of failed parts, but also significantly extend the service life of new parts.
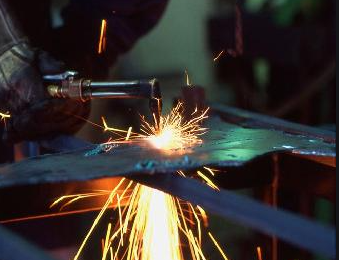
Modification and repair of new parts
Laser technology can improve the surface performance of the workpiece by cladding a layer of coating with special properties on the surface of the designated area of the workpiece, making important components have ultra-wear-resistant and anti-corrosion characteristics, and greatly improving the service life of the components.
After the production of chemical industry ball valves, the surface modification of the cladding layer is required to be 1.2 mm thick, free of defects such as pores and cracks, with high corrosion resistance requirements, and the hardness of the cladding layer is above 55 HRC.
Laser repair of old parts
In the petrochemical industry, equipment has been exposed to harsh working environments for a long time, which can easily cause severe corrosion and wear of components, and even lead to the complete scrapping of large and expensive components. While laser cladding technology is possible to repair some expensive parts and parts that are not easy to replace, the strength of the repaired parts will be twice that of the original parts, and it saves enterprises the cost of new parts.The components that often cause problems in chemical equipment include valves, pumps, impellers, large rotor journals, discs, bushings, and so on. After the failure of ball valves and shaft parts in the chemical industry, the coating is repaired. The coating thickness is 1mm, without defects such as pores and cracks, and has a certain degree of corrosion resistance. The hardness of the cladding layer is above 50HRC.
Advantages of laser cladding:
1.During laser cladding, the heat affected zone on the substrate is small and the workpiece deformation is small.
2.Metallurgical bonding can be achieved between the cladding layer and the base material, and the dilution ratio of the cladding material is low.
3.The melted summer layer has fine grains and dense microstructure, which can achieve high hardness, wear resistance, and corrosion resistance.
4.Selective partial minor repairs can be achieved, effectively reducing maintenance costs.
5.The adaptability of the powder material system is relatively high, and most conventional and special metal powder materials can be coated onto the surface of metal parts.
Difficulties in the application of laser cladding technology in the repair of chemical equipment:
1.The process parameters of the cladding process are uncontrollable factors.
The technological parameters of laser cladding technology play a decisive role in the mechanical properties and microstructure of the cladding layer. The main technical parameters during the cladding process include laser energy, spot size, cladding speed, preheating temperature, overlap size, powder feeding method, and powder feeding speed., Moreover, many technical parameters interact and restrict each other. Currently, the parameters used by various research and production institutions are mainly based on empirical data, lacking theoretical basis.
2.Crack defects in the cladding layer
In the process of laser cladding, the cladding zone rapidly melts under the action of laser light and then solidifies rapidly. Due to the slight difference in the physical shrinkage properties between the cladding powder and the base material, when the cladding area is rapidly cooled, the cladding layer is limited by the inherent elements of the cold substrate, resulting in endogenous tensile stress. When the endogenous tensile stress exceeds the limit that the cladding layer can withstand, cracks will occur on the cladding surface, which is an important indicator affecting the quality of cladding.
Summary:
Laser cladding can also be applied to other industries such as iron and steel metallurgy, automotive industries, engineering machinery, mold manufacturing, and shipbuilding, with a very broad application prospect. With the continuous promotion of the “Made in China 2025” development plan, laser cladding technology will definitely be accepted by the majority of users in the I industry, bringing more benefits and value to industrial production.
About HGSTAR: HGSTAR is is a sub-brand of HGTECH.HGTECH the pioneer and leader of laser industrial application in China, and the authoritative provider of global laser processing solutions. We have comprehensively arranged laser intelligent machine, measurement and automation production lines, and smart factory construction to provide overall solutions for intelligent manufacturing.