Projects
Application of Laser Cleaning in Petrochemical Field
Laser cleaning is a surface engineering technology that uses the high energy characteristics of laser to remove the attachments on the surface of the substrate. At present, it has been demonstrated and applied in the fields of mold, shipbuilding, machining and aerospace. As a pillar industry of the national economy, most manufacturers of laser cleaning industry have paid attention to the application and promotion of laser cleaning technology in this field.
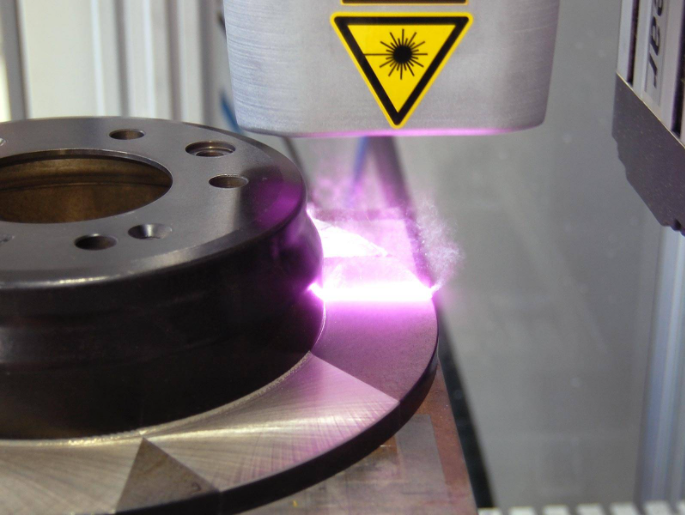
Laser cleaning is a surface treatment technology that can obtain high-energy laser beam through optical system and remove attachments on the substrate surface by vibration and ablation. Laser cleaning has many advantages, such as: laser has high energy characteristics, which can effectively remove micron and nanometer particles; Laser cleaning has no mechanical contact, will not cause unexpected mechanical damage to the cleaning object, and there is no wear problem; Laser cleaning does not require chemical solvents, which saves the waste liquid treatment steps, and avoids unnecessary chemical corrosion to the equipment, and does not require drying operation after cleaning; The waste from laser cleaning is mainly solid debris and powder, which is small and easy to handle, and does little harm to the environment and human beings; Compared with ultrasonic cleaning, its noise is lower; Laser cleaning can be used for selective cleaning; It can realize remote operation; The laser cleaning operation mode is diverse, which can be operated manually and is easy to be controlled automatically.
At present, the cleaning technologies of petrochemical equipment at home and abroad are mainly divided into chemical cleaning, physical cleaning and environmentally friendly microbial cleaning technologies.
Chemical cleaning uses chemical reagents and their aqueous solutions to remove dirt on the surface of objects, and chemical cleaning solutions are being prepared for workers. To clean some parts of the equipment, it is necessary to remove the parts and soak them in chemical reagents, or apply chemical reagents to the parts on site. Although acid, alkali, neutral and other chemical reagents are effective, they will produce waste liquid and waste water and cause great environmental pollution; Before discharge, it is usually necessary to treat the waste liquid and wastewater, including chemical treatment, which increases the cost and is easy to cause secondary pollution.
Physical cleaning was first used to poke, brush, grind, shovel, etc. Its labor intensity is high, and its efficiency and quality depend on the proficiency of workers, which is generally low, and it is difficult to deal with places that are difficult to reach. With the technological innovation and development, PIG cleaning technology and jet cleaning technology (such as sand blasting cleaning, shot blasting cleaning, dry ice cleaning, high-pressure water jet cleaning, etc.) have emerged successively. The former is only applicable to the internal cleaning of pipes and equipment, while the latter may cause unexpected mechanical damage and wear to the cleaning object, leading to equipment failure. In addition, most of these cleaning equipment need to be stored with cleaning agent, which is not easy to carry and move. For chemical equipment with high position, it can not be cleaned directly, and it is often necessary to dismantle the chemical equipment to the ground. In addition, there is ultrasonic cleaning technology. The noise pollution generated is harmful to human health. After cleaning, drying and other processes are required.
Microbial cleaning is only applicable to specific dirt, and its market share is very small due to the scale type.
The requirements for cleaning technology in modern petrochemical industry are increasing. It is necessary to reduce cleaning costs, improve cleaning efficiency and quality, and be environmentally friendly. Obviously, chemical cleaning technology and traditional physical cleaning technology cannot fully meet these new requirements. Due to the complex structure of petrochemical equipment, it is often necessary to control the cleaning area, and different areas have different requirements for cleaning efficiency and quality. For example, it is difficult to have defects in the continuous area of the container body and the requirements for surface quality are not high, so quick cleaning can be selected. For the joints and welds that may have defects, it is required that the cleaning process cannot expand the defects. This requires reducing the cleaning speed and improving the cleaning quality. At this time, the delamination cleaning method can be used to complete the cleaning without damaging the substrate as much as possible. However, neither chemical cleaning nor traditional physical cleaning can accurately control the cleaning area and quality.
Compared with traditional cleaning technology in petrochemical field, laser cleaning technology has the following characteristics:
1) No or only a small amount of solution is needed;
2) There are many kinds of attachments and substrates that can be cleaned;
3) It can effectively remove the surface attachments and the substrate damage is small;
4) It can control the cleaning area and quality;
5) It can be made portable with good mobility;
6) Easy to realize automatic operation;
7) The service life of the equipment is long, the operation only consumes electricity, and the overall cost is low.
In contrast, laser cleaning has obvious advantages and applicability. The petrochemical industry is the pillar industry of China’s economy, and the promotion and application of laser cleaning technology is expected to bring considerable economic and social benefits. As we all know, the petrochemical industry is one of the important sources of industrial pollution. The adoption of more environmentally friendly laser cleaning technology instead of traditional technology can reduce the emissions of three wastes, effectively save enterprises and national pollution control investment, and meet the requirements of the national green development strategy. In addition, chemical cleaning is harmful to the health of workers. Even if the treatment is improved, few people are willing to do this work. Laser cleaning technology can reduce the health cost for workers and the difficulty and cost of recruitment for enterprises.
It is believed that in the future, convenient, efficient, green, safe and reliable laser cleaning technology will become the main force in the application of petrochemical industry.
About HGSTAR: HGSTAR is is a sub-brand of HGTECH.HGTECH the pioneer and leader of laser industrial application in China, and the authoritative provider of global laser processing solutions. We have comprehensively arranged laser intelligent machine, measurement and automation production lines, and smart factory construction to provide overall solutions for intelligent manufacturing.