Projects
How to Avoid Hidden Dangers In Laser Processing
Now the reliability and repeatability of laser processing have enabled manufacturers to produce higher quality with higher efficiency.
Quantity of parts. From sintering in additive manufacturing to parts processing in electric vehicles, the industry is developing new applications of laser technology every day. With the development of laser technology, laser processing becomes more stable, reliable and more common.
However, there are still many hidden dangers in the deployment, operation or maintenance of industrial lasers.
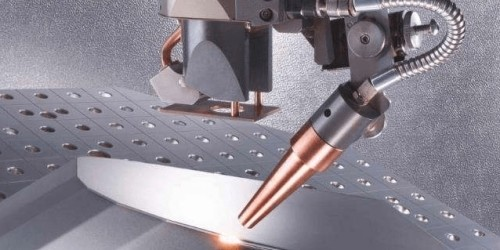
The laser operator may have a false sense of safety and develop bad habits for maintaining the consistency during laser processing. These hidden dangers can be attributed to several different problems, including understanding the behavior of laser in material processing applications, understanding the difference between current laser products and traditional laser products, and knowing when. Where to measure the laser performance. Distinguishing fact from illusion is the key to ensure high-quality laser processing.
Hidden danger 1
Don’t think that the current laser processing is so stable that it doesn’t need much monitoring. Shortly after the emergence of laser in the 1950s, the application of material processing has been developed.
Carbon dioxide (CO2) laser can produce 10.6 um laser. With its powerful power, relatively low operating cost and easy maintenance, CO2 laser has always been the backbone of laser manufacturing. Thanks to the operation and maintenance specifications developed by a large number of laser operators, there are still hundreds of thousands of CO lasers in use.
Now the laser system has become more high-quality and reliable, which leads users to ignore the following points: the laser system is still composed of physical parts with physical characteristics. The mechanical and electrical components in the laser system will gradually degrade or fail after a period of use. The harsh industrial environment is full of processing waste, which will only increase the possibility and frequency of degradation and failure of these components; As a result, the efficiency of the laser system is reduced and the operation cost is higher. Although the laser system designers have achieved innovation in the management of processing waste, if there is no systematic
Hidden danger 2
Many times, relying solely on others to solve their own laser problems may have to pay a high price. It is particularly important for manufacturers to maintain good relations with industry experts such as application engineers and system integrators. These experts continue to improve their methods and transform processing requirements into tools to help manufacturers continue to produce high-quality parts. But laser processing may also have problems. When working with invisible tools, it is always difficult to determine the source of the problem. When the laser measurement product is not in the troubleshooting range, it needs to spend more time and money to restore the system.
In this case, the cost can be recovered quickly by using the laser solution. These solutions can be used not only to determine the reference performance of the laser in the system, but also to find the problem of the laser, so that the system can recover to the reference performance more effectively. Integrated laser measurement products help to determine the change of laser status, that is, to detect the change trend of laser performance, to help operators develop more effective maintenance programs, and to help troubleshoot when problems occur.
Hidden danger 3
If the laser does not work as required, just adjusting the power can not really solve the problem. As mentioned earlier, this situation often occurs in CO and laser applications. Laser operators understand that “time is money”, and their work performance is often linked to the number of qualified parts produced. When the performance of the crystal clear is poor, the laser operator usually takes the fastest measures to restore the system to normal.
Analyzer allows users to adjust their Laser technology, in order to achieve a precise laser intensity that is sufficient to complete the task, and at the same time ensure that the intensity is not too large to cause overheating of the workpiece and cannot achieve the best processing effect. The current laser measurement scheme can help users better understand the laser performance, and also make the operation and maintenance of the system more efficient than before.
Hidden danger 4
Many people believe that the return on investment of laser measurement system is very low. This is mainly due to a misunderstanding in people’s minds: the laser measurement scheme is not only expensive, but also difficult to set up and use. There is also a mentality that although it is good to have laser equipment, it may not provide useful information for applications.
It is true that the cost of purchasing laser measurement system is very high in the past. But now, with camera technology and optical components. Network. With the progress of communication, computing power and software, laser measurement products have become smaller, faster and cheaper, and can provide very useful laser information.
Hidden danger 5
Without a laser measuring system, it is impossible to manage the laser processing process. In some cases, the development of a laser application. Deployment and implementation will simply assume that the performance of the laser is consistent: this assumption will not be ruled out until processing problems occur.
Hidden danger 6
Not all traditional laser measurement technologies have passed the test of time and can provide sufficient information about the laser.
Some laser system maintenance personnel are still using very simple tools for maintenance and troubleshooting. With the development of Industry 4.0, feedback information from processing tools is very valuable for improving industrial processing. Laser processing system is no exception. Now laser measurement products. Laser characteristic information can be provided in several different ways.
About HGSTAR: HGSTAR is is a sub-brand of HGTECH.HGTECH the pioneer and leader of laser industrial application in China, and the authoritative provider of global laser processing solutions. We have comprehensively arranged laser intelligent machine, measurement and automation production lines, and smart factory construction to provide overall solutions for intelligent manufacturing.