Projects
Application of Laser Cleaning Technology in Locomotive Brake Disc Maintenance
As China’s relevant legislation and regulations become more and more strict, environmental protection has become a very important consideration in industrial processing. It is difficult for traditional cleaning technology to meet the high requirements of environmental protection. As a new, green and efficient cleaning method, laser cleaning technology has gradually been widely concerned by the society.
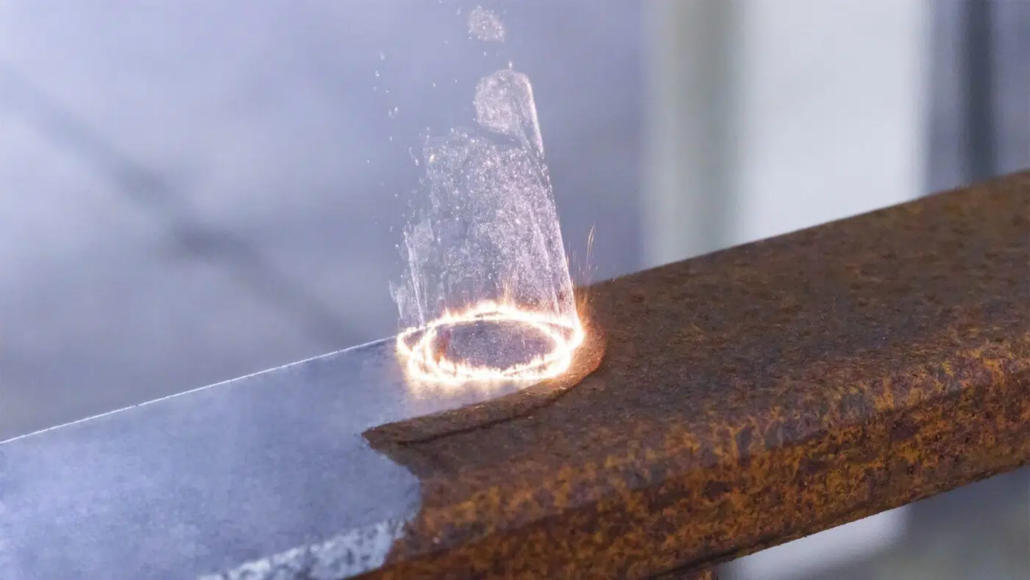
At this stage, the maintenance of brake discs depends on manpower, which is time-consuming and labor-intensive. The dust and noise generated during the mechanical grinding process cause great harm to personnel health. At the same time, the skills of the maintenance personnel are uneven, and it is very easy to cause incomplete cleaning or excessive grinding, resulting in excessive damage to the parts. In view of this, the locomotive brake disc adopts the automatic laser cleaning technology which can effectively reduce the labor force, reduce the labor intensity, and maintain a stable working state when working for a long time.
In terms of processing quality, the automatic laser intelligent cleaning machine for brake discs has uniform cleaning quality, strong consistency, almost no damage to the size of parts, and effectively improves the service life of brake discs; In terms of environmental protection, the cleaning system does not produce waste liquid, waste gas, noise and other pollution, which is conducive to environmental protection and physical and mental health of workers; In terms of social and economic benefits, the system can greatly reduce labor costs and reduce the consumption of consumables such as grinding heads. Although the cost of this equipment is high at one time, the economic benefit of laser cleaning will be far higher than that of manual polishing in the long run.
Cleaning equipment
The laser cleaning system used in the experiment consists of fiber laser, beam shaping system, robot, workbench and auxiliary equipment. The fiber laser cleaning machine used in the laser cleaning equipment has a built-in cooling system, which has good laser beam quality, long service life, stable performance and maintenance-free, and can be widely used in laser cleaning in many fields. In the process of laser cleaning, a dust collector is used to collect the stripped rust particles to prevent contamination of the material surface and ensure a good working environment.
Cleaning objects
The material used for the brake disc is Q345E. According to the national standard GB8923-88, the corrosion degree of the parts is judged. It is found that the steel surface has been rusted and some oxide scales have been rusted. Therefore, the corrosion grade of the parts is determined as Grade B. After taking the average value for many times, the average thickness of the rust layer is about 23um. Through the analysis of the corrosion degree of the material surface, it is found that the corrosion degree of the surface is uneven, which is caused by the different wear and corrosion degree of the brake disc surface during the operation.
Surface hardness test
The hardness of the substrate surface after laser derusting was tested by using the Huayin digital microhardness tester. Among them, the test force is 2.942N, and the load holding time is 15s. In order to ensure the accuracy of the test results, measure a point at different parts of each sample, and calculate the average value to measure the test results.The distribution trend of the hardness value of the substrate surface before and after cleaning was analyzed. The distribution trend of the hardness value on the surface of the base material after cleaning is relatively fluctuating, but the average hardness value is higher than the hardness value of the dry base material. It can be found that the microhardness of the surface after twice laser cleaning is about 8% higher than that of the base metal. Laser derusting can improve the hardness of the surface of carbon steel, which is of great significance to prevent the secondary oxidation and surface strengthening of carbon steel.
X-ray fluorescence element analysis
The element content on the surface of brake disc before and after laser cleaning was measured by X-ray fluorescence spectrometry. The measured data are shown in Table 1. The comparison shows that the oxygen element content on the rusted surface of brake disc before laser cleaning is as high as 15.302%, while that of laser cleaning. After cleaning, the content of oxygen element is only 3.340%, and the content is significantly reduced by 78.1%. It can be seen that laser cleaning has an obvious effect on removing oxygen and rust on the surface of brake disc.
Surface metallographic structure analysis
Before laser cleaning, the surface of the brake disc is covered with uneven rust. After the best laser cleaning process, the rust on the substrate surface is removed, the mutual weight is lit, and the important pits are formed on the surface, and the original rust area is cleaned. In addition, the surface after laser cleaning is magnified by 500 times, and it can be seen that the surface is covered by a round bright patch to form a circular cleaning area, and the rust layer in the middle of the pit is basically removed, and the uniform brightness appears. The edge part of the pit is dry with a ring-shaped convex shape, because under the intense impact of pulse laser, the metal in the middle of the pit flows to the moving edge and accumulates to form a ring. The ring-shaped part of the adjacent pit appears early and overlaps with incense. There is almost no rust in the day, and the surface is completely cleaned.
Epilogue
Through various experimental data, it is proved that the automatic laser cleaning equipment for locomotive brake discs can be used to remove rust, surface pollutants and oil stains on the surface of locomotive brake discs. The visual removal effect is good, and the cleaning has little impact on the performance of the parts itself, which can meet the needs of locomotive brake disc maintenance and repair.
Rail transit equipment is a large product composed of advanced technology, high-end equipment and system engineering. Technological progress is the driving force to continuously promote industrial development. Independent control of key core technologies is an important guarantee to maintain the security and stability of the supply chain in the face of complex international situations. Laser cleaning technology has greatly reduced the cost of rail transit equipment manufacturing, maintenance and repair, improved the level of intelligence, and conforms to the direction of green intelligent manufacturing. The efficient use of laser cleaning technology will help improve the competitiveness of the rail transit equipment industry chain and supply chain. With the deepening of research and application, laser cleaning technology will become an indispensable means to promote the upgrading and transformation of the rail transit industry.
About HGSTAR: HGSTAR is is a sub-brand of HGTECH.HGTECH the pioneer and leader of laser industrial application in China, and the authoritative provider of global laser processing solutions. We have comprehensively arranged laser intelligent machine, measurement and automation production lines, and smart factory construction to provide overall solutions for intelligent manufacturing.