Projects
Application Of Laser Tailored Welding Technology In The Automotive Industry
Laser welding has significant advantages such as high efficiency, convenient energy transfer, post weld joint denaturation, less deformation, and smooth surface, which can be widely used in automotive components.
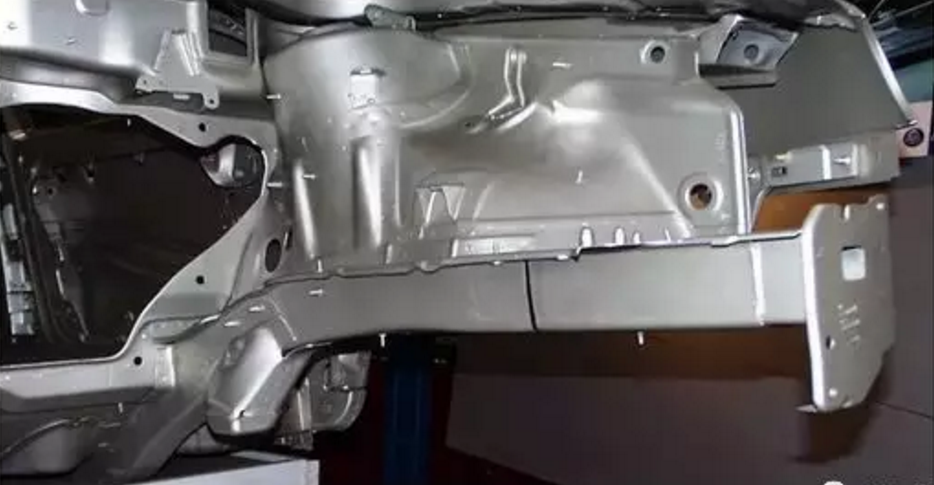
01. Laser welding of car door inner panel
On the basis of structural analysis, the laser welded door inner plate directly welds steel plates with different thicknesses or strengths together, utilizing the different material characteristics of each part to optimize the strength and quality of the parts compared to a single plate.
This design scheme simplifies the production process and improves the side impact resistance, with a rigidity increase of about 40%, further reducing the internal noise of the car during driving.
02. Laser welding of automotive pillars
In order to ensure functional requirements, the column must have a certain degree of rigidity and cushioning performance to ensure personal safety during lateral impact. By using welding technology, two steel plates with different thicknesses can be welded together to form a complete plate, and then stamped into shape.
This can achieve the goals of improving side impact performance, eliminating reinforcing ribs to reduce vehicle weight, improving assembly tolerances, simplifying production processes, and reducing costs.
03. Laser welding of the front longitudinal beam of automobiles
In order to ensure functional requirements, the front longitudinal beam must have a certain degree of rigidity and energy absorption, as well as a certain degree of strength to ensure that the thin steel plate absorbs a certain amount of energy during head-on impact and can buffer it. The thick steel plate can resist the impact of residual force without deformation or a small amount of deformation, ensuring personal safety.
By using laser welding technology, three steel plates with different thicknesses can be welded together to form a complete plate, and then stamped into shape. This can achieve the goal of improving the shockproof performance at the joints, reducing independent components, reducing vehicle weight, simplifying production processes, and reducing costs.
04. Laser welding of automobile wheelhouse
The application of laser welded blanks on wheel housings also reduces weight and number of components due to the built-in shock absorption structure, eliminating spot welding overlap, spot welding materials, and spot welding processes, resulting in tangible cost reductions; At the same time, the sealing material was removed, saving manpower.
05. Laser welding of automotive flooring
In order to improve collision performance and component stability, laser welded blanks technology has also been applied to car floors, and can also achieve the goal of eliminating overlapping joints, sealing materials, reducing vehicle weight, and making it more conducive to recycling.
In addition, laser welded blanks have been widely used in the trunk reinforcement plate, trunk inner plate, shock absorber support, bumper, roof, frame, instrument panel crossbeam, etc. of car bodies.