Projects
Application of Laser Welding in New Energy Vehicles
Laser welding belongs to melting welding, which uses the laser beam as the energy source to impact on the weldment joint. Laser welding is non-contact welding, which does not need to be pressurized during operation, but inert gas is required to prevent oxidation of the molten pool, and filler metal is occasionally used. Laser welding can carry out precise energy control, so it can realize the welding of precision micro devices, and it can be applied to many metals, especially to solve the welding of some hard-to-weld metals and dissimilar metals.
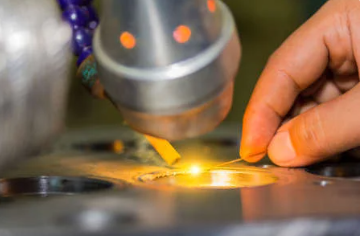
As laser welding is fast and easy to realize remote control and automatic production, it is widely used in industries with high degree of automation such as automobile manufacturing and new energy battery production. With the development of new energy vehicle market in recent years, it also drives the market demand for laser welding equipment. The data shows that the market size of laser welding equipment in China increased from 1.56 billion yuan to 10.13 billion yuan in 2019. The main application processes in the automobile industry mainly include laser tailor-welding of plates with different thickness, laser assembly welding of body assembly and sub-assembly, and laser welding of automobile parts. In the field of power battery, laser welding is the best process for sealing welding of explosion-proof valve, pole lug welding, soft connection welding, spot welding of safety helmet, sealing welding of battery shell, module and PACK welding. The application of laser welding technology on the automobile body can reduce the weight of the body to achieve the purpose of fuel saving; The firmness and lightness of laser welding technology can improve the integration of vehicle body; Laser welding technology has the characteristics of high precision and efficiency, which can improve efficiency in production and ensure its safety and stability. When the car is driving, due to the bumps and squeezing of the ground, each component and structure is subject to different degrees of impact, which requires that the overall structural precision strength of the car be very high. Using the current laser welding technology, its dynamic and static stiffness can be increased by more than 50% compared with other welding processes, reducing the noise and vibration during driving, improving the ride comfort, and improving the safety performance of the car.
Advantages of laser welding automobile body
- The most important advantage of non-contact processing laser welding in automobile manufacturing is reflected in the advanced non-contact processing method. The traditional processing methods such as screw fastening and adhesive connection cannot meet the requirements of precision and robustness in modern automobile manufacturing, and the application of new materials also makes the traditional processing methods slightly inferior. Laser welding is non-contact. In the process of processing, precision welding can be realized without touching the product. It has achieved leapfrog progress in the process of connection robustness, seamless, precision and cleanness.
- Laser welding can improve the lightweight of automobile. Laser welding can replace casting parts with more stamping parts in automobile manufacturing, and continuous laser welding can replace scattered spot welding, which can reduce the overlap width and some strengthening parts, reduce the volume of the body structure itself, thereby reducing the weight of the body, and meet the requirements of energy conservation and emission reduction of automobiles.
- Improve the assembly accuracy and rigidity of the body. There are hundreds of thousands of parts in the body and chassis of a car. How to connect them together has a direct impact on the rigidity of the whole car body. Laser welding can be used to connect almost all metal materials of different thickness, brand, type and grade together. The welding accuracy and assembly accuracy of the body are greatly improved, and the body rigidity is increased by more than 30%, This improves the safety of the car body.
- Compared with the pure laser welding technology, the laser hybrid welding technology can greatly improve the connection ability of the seam of the sheet metal parts, so that enterprises can make more full use of the process stability of the arc welding during laser high-speed welding.
Nowadays, the application of laser welding to the production of automobile body has become a trend. Using laser welding can not only reduce the volume of the body and improve the assembly accuracy of the body, but also greatly enhance the strength of the body, providing users with higher safety protection while enjoying comfort. The laser welding machine for auto parts is a kind of laser equipment that uses robot intelligent operation, collimates the parallel light through the collimator, and focuses on the workpiece for welding. With a simple universal instrument, the flexible transmission non-contact welding can be carried out for the welding precision parts that are difficult to access by large molds, which has greater flexibility and operability.
About HGSTAR: HGSTAR is is a sub-brand of HGTECH.HGTECH the pioneer and leader of laser industrial application in China, and the authoritative provider of global laser processing solutions. We have comprehensively arranged laser intelligent machine, measurement and automation production lines, and smart factory construction to provide overall solutions for intelligent manufacturing.