Projects
Uncover the Truth of High Power Fiber Laser Cutting
It is obvious that people want to make money with laser cutting machines. Many people believe that increasing the power of lasers will increase their income – sometimes it is, but sometimes it is not. If we consider how increasing power will affect income, then we should discuss this issue in detail. When the power range is relatively low, any increase in power is directly reflected in the overall efficiency. With the increase in power, the cutting speed will also increase proportionally. However, when the parts are small, the cutting speed that can be achieved by laser power may not be fully utilized.
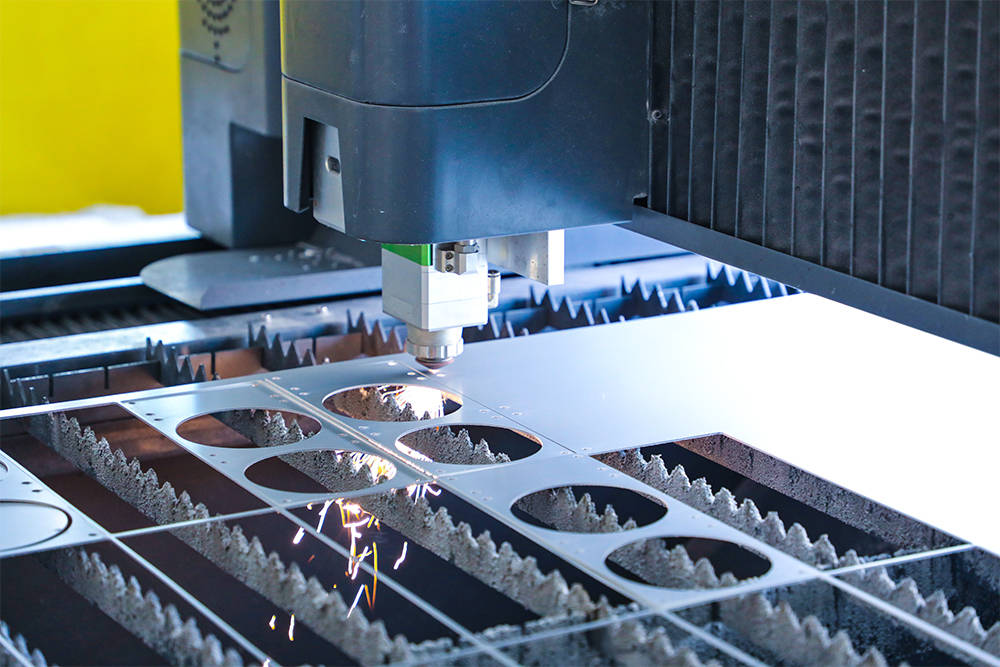
Increasing power on small parts is no longer effective. So when cutting thin plates and small details, it is meaningless to increase power. All these considerations are applicable to cutting in nitrogen; After the material to be cut reaches a certain thickness, it must be transferred to oxygen cutting. However, when cutting with oxygen, the cutting speed is much lower, and this speed does not increase with the increase of power. This means that increasing power is only meaningful for plates with medium thickness.
High laser power is only meaningful when cutting materials of medium thickness. For thin plates, high power cutting cannot be used because it is limited by machine power; for thick plates, cutting speed will be limited by oxygen cutting technology. Therefore, if most of the cutting tasks are metal plates with a thickness of 8 mm, a laser with a power of at least 8 kW should be used; If the thickness is 12mm, a laser with a power of 12kW should be used, and so on.
The above dependence shows that further increasing the power, such as to 15kW or 20kW, should almost completely eliminate the cutting of thick plates in oxygen. Laboratory research has confirmed this, but is the industry ready to use such high power?
The challenge of using high power cutting
In recent years, the rapid development of fiber laser sources has led to the emergence of high power products of 20kW or even 30kW on the market. However, it has proved that it is not so simple to apply these high-power lasers to cutting equipment. Providing extremely high power looks great in advertising, but can its high purchase cost really be paid off?
The biggest problem is the energy absorption and loss of the cutting head, which will cause the optical elements to overheat. The higher the laser power, the more harmful the thermal effect.
In order to make the cutting process run normally. Many parameters of the process must be controlled, one of which is the height of the focus, which must be accurately preset for each type and thickness of cutting material.
At low power, the exposure of an optical element will not damage adjacent elements. However, at high power, the damage speed of optical elements will be so fast that it may cause pin reaction. Before the operator can react, all parts of the laser head, including optical fiber, have been damaged.
The above phenomenon means that many companies have decided to purchase lasers with very high power collimation, hoping to greatly improve efficiency, but they cannot fully utilize such high power.
Facts have proved that overheating and numerous failures of optical elements will cause huge costs and long downtime. Users of this type of laser often have to reduce the power of the laser to the level that the laser can work stably. Usually, the actual power used is even half of the power they pay.
It should also be remembered that although the linear cutting speed can reach twice when the power is doubled, this cannot be converted into double the total production efficiency.
In addition to limiting the capacity under high power due to the thickness of the plate, as mentioned above, increasing the power cannot linearly increase the number of parts produced in a shift. Increasing the laser power cannot shorten the rapid weighing between parts, shorten the time for changing trays or preparing for activities, or shorten the lunch break time of operators.
If you choose a 15kW laser instead of a 6kW laser, the price of the laser may double. However, considering the entire material thickness range. According to the number of components cut, the average production efficiency of the whole machine will only increase by about 30%.
Therefore, it has been proved that the production efficiency of two 6kW lasers purchased with the same amount can be increased by 100%. It should also be remembered that if two lasers are stopped, the other laser can continue to cut and ensure the continuity of production.In short, providing very high laser power will indeed cause people’s excitement and “exclamation” effect. However, this cannot be directly translated into the expected results, just as a 1000-horsepower car will not cross a city faster than a 100-horsepower car.
We have analyzed which factors will limit the efficiency of fiber lasers. It is found that for thinner plates, the maximum limit of efficiency is not the power of the laser source, but the dynamics of the machine movement, which is also proved by the fact. The control systems used by many laser manufacturers are mainly designed for milling machines and lathes. Due to the need to slow down in complex shapes, the speed is too slow, wasting the potential of fiber lasers.
An error-free positioning laser control system with dynamic vector analysis function can use very high power on thin plates. This is a breakthrough solution based on breaking linear drive. Allows users to achieve extremely high work dynamics, even on small parts with complex shapes. Through the use of innovative cutting head monitoring system, the limitations related to high-power laser optical elements have been solved.
Nevertheless, the rationality of purchasing lasers with very high power should always be analyzed separately. Because in many cases, it may be found that high power will greatly increase the purchase and use costs, but not necessarily improve production efficiency.
About HGSTAR: HGSTAR is is a sub-brand of HGTECH.HGTECH the pioneer and leader of laser industrial application in China, and the authoritative provider of global laser processing solutions. We have comprehensively arranged laser intelligent machine, measurement and automation production lines, and smart factory construction to provide overall solutions for intelligent manufacturing.