Projects
Characteristics Of Laser Welding Of Automotive Body
Non-contact machining
The most important advantage of laser welding in automotive manufacturing is reflected in the advanced non-contact processing method. Traditional processing methods such as screw fastening and adhesive connection cannot meet the requirements for precision and robustness in modern automobile manufacturing, and the application of new materials also makes traditional processing methods slightly inferior. Laser welding is non-contact, and during the processing process, laser precision welding can be achieved without touching the product. It has achieved leapfrog progress in the robustness, seamless, precision, and cleanliness of the connection, providing more possibilities for the advancement of automobiles.
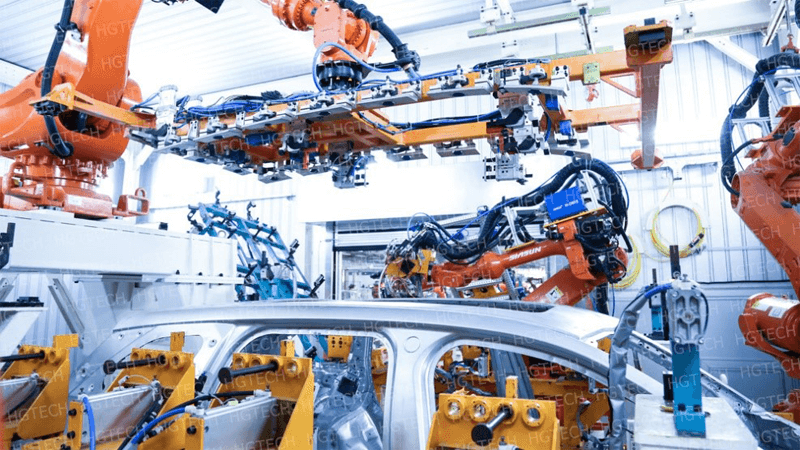
Laser welding enhances the lightweight of automobiles
The use of laser welding can replace cast parts with more stamped parts in automobile manufacturing, and continuous laser welding can replace scattered spot welds, reducing the overlap width and some strengthening components, reducing the volume of the body structure itself, thereby reducing the weight of the body and meeting the requirements of energy conservation and emission reduction in automobiles.
Improve the accuracy and stiffness of vehicle body assembly
There are hundreds or thousands of parts in a car’s body and chassis, and how to connect them together has a direct impact on the rigidity of the entire vehicle body. Laser welding can almost connect all metal materials of different thicknesses, grades, types, and grades together, greatly improving the welding accuracy and assembly accuracy of the body. The body stiffness is increased by more than 30%, thereby improving the safety of the body.
Laser hybrid welding enhances process stability
Compared with pure laser welding technology, the use of laser hybrid welding technology can greatly improve the connection ability of gaps in sheet metal parts, thereby making more full use of the process stability of arc welding during high-speed laser welding. In addition, the use of laser welding can also reduce stamping and assembly costs in the manufacturing process of automobile bodies, shorten production cycles, reduce the number of parts, and improve the integration degree of the body.
The high economic value of laser welding has a great temptation for automotive companies. In the future, laser welding technology will have great development space in automotive manufacturing and will gradually be applied to body welding to replace traditional welding processes. The highly automated and intelligent production lines are driving automotive companies to replace traditional welding processes, while also pushing automotive manufacturing into fully automated production.
Laser welding is not only used for welding structural components, but will also be gradually applied to the manufacturing of panel components with the improvement of technical level and the use of high-precision detection instruments. Reduce the development costs of molds and investment costs for automotive companies, creating more economic value for them.