Projects
Coil-Fed Laser Blanking Lines Empower The Automotive Industry
Laser processing technology for automotive applications
The automotive industry is one of the most widely used fields for laser processing. In developed industrial regions such as Europe and America, 50% -70% of automotive components are manufactured using laser processing technology. In industrialized countries, there are over 30000 laser processing equipment used in the automotive industry worldwide, and hundreds of laser processing equipment are put into use every year.
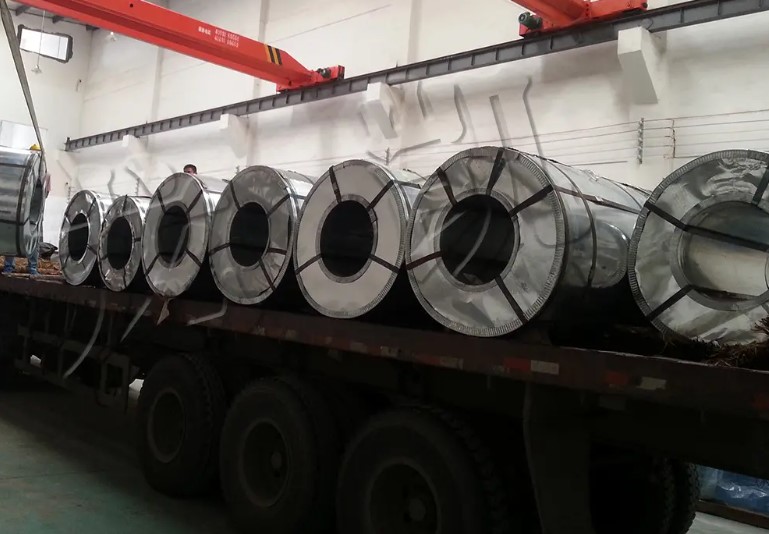
The impact of lightweight trends
Automobile lightweighting has become a hot topic pursued by market consumers, and an important trend in future development is body lightweighting. With the development of lightweight vehicles, new materials, structures, and processes continue to emerge, and laser processing technology will ignite a new wave of enthusiasm.
In the production process of car roof covers, engine and luggage compartment covers, ABCD pillars and other components, if traditional stamping technology is used, each model requires at least one set of cutting molds, which has a long mold opening cycle and high investment cost. And market demand is constantly changing, on the one hand, the acceleration of car model updates and the increasing demand for small-scale production; On the other hand, with the demand for lightweight new energy vehicles, the proportion of aluminum alloy materials used is increasing. This type of material has a sensitive surface and is prone to damage during the material dropping process. The falling of aluminum shavings may leave traces on the mold, leading to component scrapping. The use of HGTECH laser uncoiling and material cutting production line to process aluminum alloy sheets almost does not produce waste, which can meet the high-quality needs of the automotive industry.
High quality coil feeding laser punching line
One HGTECH coil feeding laser blanking line can complete the traditional four processes of uncoiling, leveling, manual feeding, shearing, and cutting in one step, saving time and cost. When cutting, synchronous feeding can be achieved, allowing one person to operate one or more feeding lines, greatly reducing labor costs.
Regarding the upgrade of the coil fed laser cutting system, HGTECH has independently developed a multi head laser nesting software for the automatic production line of multi head laser uncoiling and material cutting, which can achieve automatic layout and improve material utilization; Equipped with a laser measurement device, it can effectively prevent sheet metal from deviating; It can also be configured with an automatic sorting and palletizing system to reduce manual labor and improve production efficiency; In addition, the laser coding system can meet the needs of production information management.
Summary
Laser has become an indispensable tool in the field of automotive lightweight manufacturing, and to some extent, it has become an industrial standard. Its non-contact laser dynamic processing and high processing accuracy characteristics can make the sheet metal free of burrs, scratches, good cutting effect, and also facilitate subsequent processing.