Projects
Coil Feed Laser Blanking Technology Of High-Strength Steel
Introduction
With the maturity of coil fed laser cutting technology, mainstream domestic and foreign car companies have begun to use coil fed laser cutting lines to produce inner and outer plate blanks. The coil laser cutting machine is particularly suitable for the cutting of high-strength steel automotive inner panels and the drilling and edge cutting after hot forming.
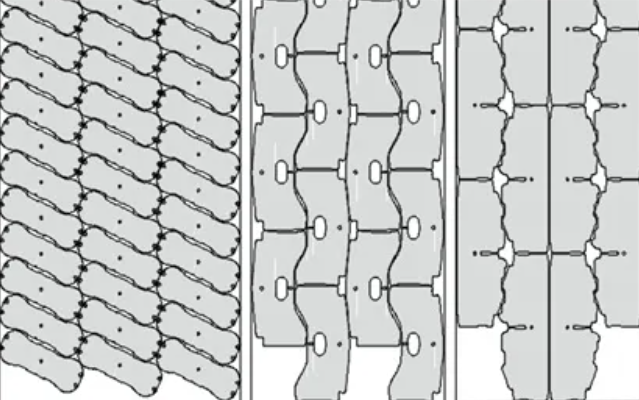
Basic process requirements for industrial laser material cutting
Traditional cutting machines use toothed nail plates to support steel plates, which sometimes hinder the cutting of debris and form slag lumps, and cannot guarantee 100% cutting. These problems rely on manual processing, so traditional cutting machines can only be used for small batch semi-automatic material production.
The most basic process requirement for industrial material cutting production is to provide reliable and stable production capacity guarantee for laser material cutting lines while meeting the quality conditions of material cutting. Only by ensuring the stability of the quality and output of the material, can the laser material cutting line gain a foothold in the automotive parts supply chain. Secondly, it is necessary to ensure that the production cost of laser cutting has advantages compared to stamping cutting, and to ensure the acquisition of production orders.
Material utilization rate and carbon emissions
The overlap of laser cutting is small, and the cutting parts can be flexibly mixed and nested without increasing production costs. Especially for automotive inner panels, laser cutting has the most advantageous material utilization rate. Referring to actual production layout examples, it is usually 5% to 10% higher than stamping cutting
The layout and cutting tool software equipped on the laser cutting line can quickly complete the layout and generate cutting production data. During the production process, users adjust the layout in a timely manner based on the actual board width of the purchased coil material, and production is not limited by the board width. During the procurement process of coil materials, the use of layout software can also optimize the selection of plate width in a timely manner.
Advanced cutting technology combining motion and stillness
Dynamic cutting refers to laser cutting while feeding, while static cutting refers to cutting without feeding. The length of the workpiece determines the feeding distance of the material belt. During the laser feeding process, the feeding operation usually takes 1-4 seconds. The dynamic cutting method saves feeding time and maximizes production efficiency. However, the feeding motion introduces mechanical errors in the feeding machine, which can lead to a decrease in cutting accuracy.
The use of a coil fed laser cutting system for dynamic cutting of high-precision contours and static cutting of high-precision contours can improve efficiency and ensure accuracy, making it an advanced laser cutting process.
Summary
The laser material cutting line has achieved fully automated material cutting production, with production efficiency about 4 times higher than ordinary cutting and approaching the efficiency of stamping material cutting. By further improving the configuration of laser cutting lines, the production capacity can reach or even exceed that of stamping cutting.