Projects
Feasibility of Fiber Laser Welding In Aluminum Alloy
For automobiles, besides fuel efficiency, a lightweight all-aluminum alloy body can presents ultimate power and handling performance. Generally, with constant power output, lighter vehicles accelerate faster, offer a more sporty driving experience, and exhibit reduced body roll during cornering. Moreover, under equivalent strength conditions, lighter cars are safer. Heavier vehicles possess greater inertia, leading to more significant impact forces in the event of accidents and more severe consequences.
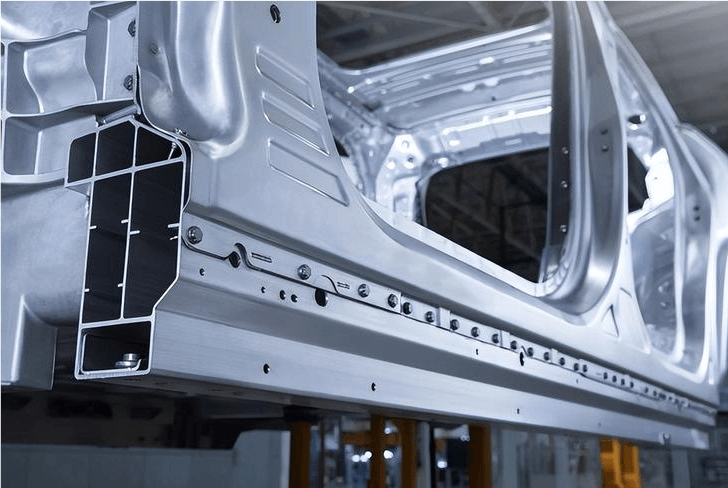
In terms of material usage in passenger cars, aluminum ranks second only to steel. Aluminum alloy is a relatively excellent material for achieving vehicle lightweighting. It has a low density, only one-third that of steel, yet it boasts superior machinability compared to steel. It also exhibits excellent corrosion resistance, high-performance strength, good thermal conductivity, and superior energy absorption characteristics compared to steel. Aluminum is easy to recycle, with 90% of aluminum being recyclable, making it the preferred choice for achieving vehicle lightweighting. It has found widespread applications, such as in the aluminum alloy suspension systems used by General Motors’ Cadillac and aluminum alloy brake discs adopted by Ford, which are two-thirds lighter than their cast iron counterparts, resulting in significant lightweighting effects. However, due to the challenges in machining and relatively poor formability of aluminum alloys, along with their excellent thermal conductivity but poor weldability, the manufacturing cost of aluminum alloys is much higher than that of steel materials. This limitation has constrained the extensive use of aluminum alloys in the passenger car industry.
Traditional welding methods like resistance welding, TIG, and MIG welding struggle to address these drawbacks. High-power density, high-performance laser welding technology, particularly fiber laser welding, has proven effective in controlling welding defects and deformation. Laser welding is one of the main directions for welding aluminum alloys in the future, with fiber laser welding technology being particularly promising in this regard.
Fiber laser systems offer exceptional beam quality, allowing for the configuration of small fiber core diameters. They can achieve high power density at relatively low power levels. Consequently, fiber laser welding is generally associated with deep penetration welding. The high energy density of fiber laser systems enables substantial welding depth with relatively low heat input, resulting in high-speed, high-quality welding processes. One of the most revolutionary features is their flexibility in use. They can be seamlessly integrated into multi-axis robotic systems and mirror-based systems, making them highly adaptable. Their compact design results in significantly smaller overall dimensions compared to traditional laser systems, enhancing their mobility. The outstanding beam quality of fiber lasers allows for the use of longer focal length focusing lenses, enabling remote welding. This is advantageous for welding stability and preventing contamination of optical components. In practical applications, this offers numerous benefits. For instance, a remote welding workstation using a fiber laser can complete the welding of an entire door panel. When integrated into a robotic system, it can accomplish the welding of an entire vehicle body through fillet or seam welding processes.