Projects
Application of Laser Welding In Enhancing The Performance of BIW
In the realm of automobile manufacturing, a significant application of laser welding lies in the welding of automobile BIW (body-in-white). One prime example of this is the welding of the automobile roof panel to the side body panel. Laser welding reduces the overlap width between the roof panel and the side body, thereby decreasing the amount of steel used while simultaneously enhancing the rigidity of the vehicle’s body structure. This laser welding technology for automobile body frames finds extensive application at FAW-VOLKSWAGEN. With the adoption of laser welding techniques, the stiffness of the vehicle body increases by approximately 30% compared to bodies manufactured using other processes, significantly elevating the overall safety factor of the vehicle.
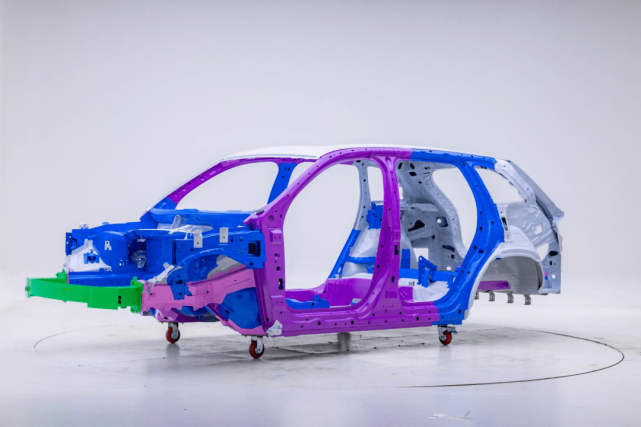
In laser welding, the focal diameter of the laser welding beam is merely 0.6mm, and the width of each laser weld seam is approximately 1 to 1.5mm. Laser welding joins only the minute regions of the sheet metal through melting, leaving other areas virtually unaffected. Furthermore, when laser welding is employed, the entire weld seam can be completed in an instant, with minimal thermal impact on the entire vehicle. For instance, the time required to complete a standard 25mm laser weld seam is only around 0.5 seconds. The rapid completion of the entire melting and joining process in an exceedingly brief timeframe, followed by swift cooling, has minimal impact on the structural integrity of the vehicle’s sheet metal.
Additionally, the use of laser welding technology minimizes deformation and alterations in the physical properties of the steel sheet, unlike other welding methods such as spot welding and MAG welding. This ensures the stiffness of the entire vehicle body. Moreover, the completion of each laser weld seam in just 0.5 seconds is an unmatched welding speed that significantly maximizes work efficiency and reduces costs, making it particularly vital for large-scale vehicle body production.
Laser-based online inspection technology has also been applied, starting with the Jetta model. Online inspection is utilized for real-time measurements of critical structural dimensions at 100% accuracy. By continuously measuring the dimensions of each subassembly and assembly in real-time, it identifies trends in dimension variations during the production process and alerts users to deviations beyond acceptable limits. This capability enhances rapid response and quality control within the production process.