High-performance display glass components are foundational to strategic industries like next-generation information technology. They play a crucial role in major economic sectors, including smartphones, electric vehicle displays, and flat-panel displays.

As the smartphone, electric vehicle, and flat-panel display industries grow rapidly, the demand for high-performance display glass with superior optical, mechanical, and geometric properties continues to rise.These demands place significant strain on manufacturing technologies and equipment worldwide, particularly in achieving low-damage cutting, precise shaping, and robust yet flexible bonding of hard, brittle, transparent amorphous materials—critical issues faced by the industry globally.
The high technical barriers and substantial investment required for high-performance display glass manufacturing have led to a long-standing dominance by a few global companies over core technologies and equipment. High-end machinery is essential for critical processes like cutting, hot pressing, and bonding, making it challenging for the global electronics industry to advance high-end display technologies independently. This reliance limits innovation and constrains further growth across the sector.
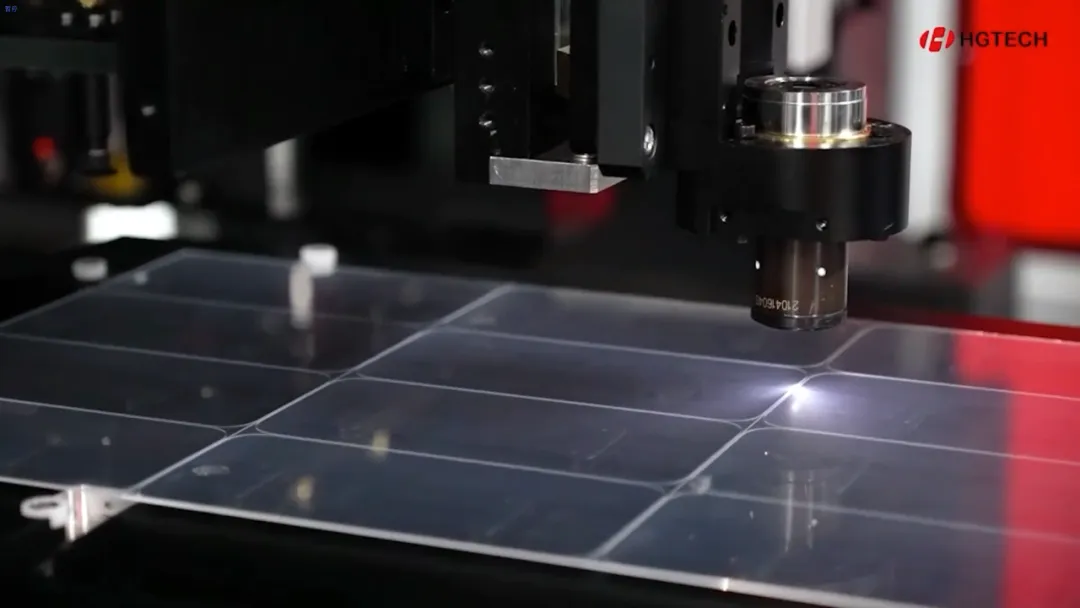
Focusing on critical industry technologies, a project team led by HGTECH, in collaboration with Huazhong University of Science and Technology and other institutions, has successfully tackled a series of technical challenges in display glass component manufacturing after more than a decade of joint efforts. These challenges include precision forming of hard, brittle materials, low-damage cutting of enclosed contours, and flexible bonding of thin films on curved surfaces.
The team has developed three main categories of advanced equipment: large-curvature ultra-thin glass hot-press forming equipment, ultrafast laser precision cutting systems for hard and brittle materials, and flexible bonding systems for functional films—comprising a total of 38 models. These systems meet key international performance standards and are now widely adopted by leading companies across various industries. They have also been exported to countries such as the United States, South Korea, and Japan, delivering significant economic benefits, enhancing technology standards in global electronics manufacturing, and driving innovation in high-end equipment development.
HGTECH will continue to accelerate the innovation and practical application of core technologies, further advancing collaborative integration across industry, academia, research, and application. These efforts aim to foster the deep fusion of “laser + intelligent manufacturing”.