Projects
High Speed Three-Head Coil Fed Laser Blanking Line Hits The Pain Points
The laser cutting technology is cleverly combined with the coil unwinding and feeding technology, and the “three-head linkage technology” of the system controlling the laser cutting head is used to perform dynamic flight cutting on the laser cutting platform, replacing the traditional press and mold, and realizing the cutting of metal strips. Automatic blanking, and breaks through the process bottleneck of the original laser cutting equipment that can only cut a single plate. It has the characteristics of integration, intelligence, flexibility, energy saving and environmental protection, and can be widely used in automobiles, ships, bridges, home appliances and other fields.
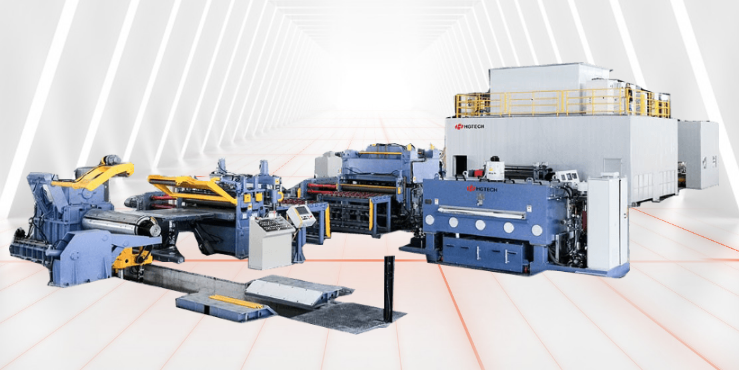
In the production process of car roof covers, engine and trunk lids, ABCD pillars and other parts, if the traditional stamping process is followed, each model requires at least one set of blanking molds, which requires a long mold opening cycle and high investment costs.
The market demand is constantly changing. On the one hand, the replacement of automobile models is accelerating and the demand for small-volume production is rising. On the other hand, under the demand for lightweight new energy vehicles, the proportion of aluminum alloy materials used is increasing. This material has a sensitive surface. It is easy to cause damage during the blanking process. The falling aluminum chips may leave marks on the mold and cause the parts to be scrapped. The use of coil fed laser blanking lines to produce aluminum alloy sheets will hardly produce any waste chips, which can meet the high requirements of the automotive industry. quality requirements. Faced with the high procurement cost of foreign blanking production line equipment, how to save costs while improving production efficiency and product quality has become a pain point for the automotive industry.
The high-speed three-head coil fed laser blanking production line independently developed by HGTech directly hits the “pain point” of the industry. It can directly perform flying cutting (i.e. follow-up cutting) blanking on the moving coil. It only needs to import the product CAD graphics, and it can be processed through the company’s self-developed software control system realizes the automatic distribution of the cutting work of the laser cutting heads. The cutting program can be flexibly customized and modified according to the needs, enabling small batch production without molds and greatly improving production efficiency.
The coil fed laser blanking line represents the future of manufacturing. Its advanced technology and integrated design have many benefits compared to traditional manufacturing methods. As companies look for ways to increase efficiency and reduce costs, coil fed laser cutting lines are becoming an increasingly popular option.
In the future, we can expect to see more advanced laser production lines offering greater efficiency and precision. As technology continues to evolve, we can expect to see more businesses embrace these new manufacturing methods and reap the benefits they bring.
The laser cutting technology is cleverly combined with the coil unwinding and feeding technology, and the “three-head linkage technology” of the system controlling the laser cutting head is used to perform dynamic flight cutting on the laser cutting platform, replacing the traditional press and mold, and realizing the cutting of metal strips. Automatic blanking, and breaks through the process bottleneck of the original laser cutting equipment that can only cut a single plate. It has the characteristics of integration, intelligence, flexibility, energy saving and environmental protection, and can be widely used in automobiles, ships, bridges, home appliances and other fields.
In the production process of car roof covers, engine and trunk lids, ABCD pillars and other parts, if the traditional stamping process is followed, each model requires at least one set of blanking molds, which requires a long mold opening cycle and high investment costs.
The market demand is constantly changing. On the one hand, the replacement of automobile models is accelerating and the demand for small-volume production is rising. On the other hand, under the demand for lightweight new energy vehicles, the proportion of aluminum alloy materials used is increasing. This material has a sensitive surface. It is easy to cause damage during the blanking process. The falling aluminum chips may leave marks on the mold and cause the parts to be scrapped. The use of coil fed laser blanking lines to produce aluminum alloy sheets will hardly produce any waste chips, which can meet the high requirements of the automotive industry. quality requirements. Faced with the high procurement cost of foreign blanking production line equipment, how to save costs while improving production efficiency and product quality has become a pain point for the automotive industry.
The high-speed three-head laser intelligent uncoiling and blanking production line independently developed by HG Tech directly hits the “pain point” of the industry. It can directly perform flying cutting (i.e. follow-up cutting) blanking on the moving coil. It only needs to import the product CAD graphics, and it can be processed through the company’s self-developed software control system realizes the automatic distribution of the cutting work of the laser cutting heads. The cutting program can be flexibly customized and modified according to the needs, enabling small batch production without molds and greatly improving production efficiency.
The coil laser cutting machine blanking line represents the future of manufacturing. Its advanced technology and integrated design have many benefits compared to traditional manufacturing methods. As companies look for ways to increase efficiency and reduce costs, coil fed laser cutting lines are becoming an increasingly popular option.
In the future, we can expect to see more advanced laser production lines offering greater efficiency and precision. As technology continues to evolve, we can expect to see more businesses embrace these new manufacturing methods and reap the benefits they bring.