Projects
Laser Cutting Follows The Trend of Advanced High Strength Steel Industry
The focus on vehicle lightweighting has ushered in the introduction of new materials and metal grades, which has increased the use of advanced high-strength steels (AHSS) with tensile strengths of 750MPa and above. Forecasts show that high-strength steel will account for 40% of body materials around 2025.
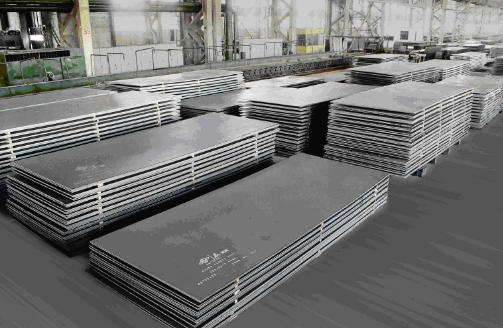
AHSS allows automakers to reduce vehicle weight compared to other lightweight materials while still meeting today’s highest crash standards. However, problems often arise with these materials in existing production processes.
For example, although AHSS can be processed with traditional mechanical stamping equipment, it usually requires large-tonnage equipment. This will have a negative impact on the mold, such as causing the mold or even the stamping machine to break. When the maximum tonnage of the stamping machine is limited, high-strength steel may cause the punching operation to be transferred to a large-capacity stamping machine for processing to obtain the same cutting effect. As a result, while improving productivity, the cost of cutting tools also increases significantly, and the purification speed of the tools is accelerated.
In addition, due to the increased hardness of steel, there is a possibility of micro cracks appearing along the cutting edge during mechanical blanking operations. These micro-cracks develop slowly during the molding stage, eventually leading to cracking problems.
- Compared with shearing or stamping machining methods, the coil laser blanking system does not produce micro cracks.
It minimizes changes in hardness of the cutting edge and produces much less debris than the burrs common with mechanical cutting. In most cases, debris will not appear on thin materials. This high quality significantly improves the molding quality, increases tear resistance, and the cut edges can be directly laser welded.
- Laser cutting also provides the flexibility of rapid batch change and can quickly adapt to changes in automobile production.
The traditional stamping process requires a long mold production time. It usually takes half a year to a year to develop an original forming mold. Including testing and correction time, after the testing is completed, it takes another 14-16 weeks to produce the final cutting mold, making the entire process very long and expensive.
- Laser processing no longer requires special molds, because materials can be ordered and programming completed in less than a day.
Sometimes it only takes a few hours. If a rigid mold is used, even minimal changes can result in a lot of work. When using laser cutting, a simple two-dimensional CAD software correction program can be used. Expensive changes that once took days to complete now cost almost nothing and can be easily done in 5 minutes.
With these advances, coil fed laser cutting is no longer just an option for niche production, it can be considered a reliable and flexible production alternative in any production operation and has proven itself in batch sizes of 100,000 pieces. In any case, this technology is particularly suitable for overcoming the difficulties encountered in processing advanced materials, handling complex shapes and delivery issues, making it an excellent choice to meet the challenges of today’s industry.