Laser cutting is a tremendously useful development that has occurred in the last half-century. Laser cutting, which projects extreme heat in an incredibly narrow stream, enables manufacturers and welders to cut custom pieces and parts out of metal with extreme precision. It, like so many other technologies, contributes to the increased slickness and dependability of many modern machine parts.
What is the maximum thickness that a 4000 watt laser can cut?
When it comes to laser cutting thick steel, the limits are primarily manifested in factors such as the materials that can be cut, the power of the lasers, and, as a result, the maximum thickness of metal that the lasers can handle.
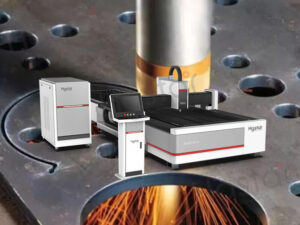
As a result, the maximum laser cutting thickness is determined by the specific laser and material used, among other factors.
We can combine a 6,000 watt laser with a metal such as stainless steel. In this case, the maximum thickness of the laser cutting would be approximately 2.75 inches.
However, the thickness is dependent on those specific variables. The same laser could probably only penetrate 1 5/8 inch of carbon steel, while a 4,000-watt laser could only penetrate 1 inch of stainless steel.
What Metals Can Be Cut by a Laser?
Lasers can cut through many materials, but they are most commonly used on a few types of metal, specifically carbon steel, mild steel, stainless steel, steel alloys, and aluminum.
Carbon steel: Steel is a combination of iron and carbon. Carbon steel is steel that contains a high concentration of carbon.
Mild steel: When compared to carbon steel, mild steel has a lower carbon concentration.
Stainless steel: To create corrosion resistance, stainless steel contains trace amounts of chromium.
Other steel alloys: Alloyed steel is strengthened by bonding it with one or more other elements.
Aluminum materials are useful because they are lighter than steel materials.
Material vs. Laser Cutting Power
When determining the maximum cutting thickness of a laser, two factors should be considered: laser power and material. A laser at one wattage will not be able to cut through as thick a material as another laser at a different wattage. Similarly, the same laser cannot cut through the same thickness of carbon steel as it can through aluminum.
3,500, 4,000, and 6,000 watts are some of the most common laser wattages encountered. Lasers with 6,000 watts are excellent for cutting through particularly thick or strong metals, but in many cases, lower wattages are more than adequate.
STRENGTH OF MATERIAL
The strength of a given metal can vary depending on factors like the ratio of different elements in the alloy, but there are still tendencies for certain types of metal to be stronger or weaker than others. Here’s a quick rundown of how the previously mentioned materials compare to one another, from hardest to easiest to cut.
Carbon steel: A metal with a high carbon content has an added layer of strength.
Mild steel: Because it contains less carbon than carbon steel, mild steel is easier to cut. Finished products made of mild steel are stronger and more resilient than those made with higher amounts of carbon, despite being more cuttable.
Stainless steel: The presence of chromium prevents rust but makes the material less ductile and more difficult to cut. It does not, however, have the same effect as carbon.
Aluminum: As anyone who has worked with aluminum foil knows, aluminum is a very ductile material. It is rarely a significant issue for lasers.
SPEED OF CUTTING
It is also important to consider speed. Lasers with higher cutting power can cut through thicker materials, but they can also cut through thinner materials in less time. Similarly, a laser can cut through weaker materials faster than stronger ones. Even if you’re not working with a particularly thick or strong metal, this can sometimes add value to using a high-wattage laser.
The use of gas in the process, on the other hand, has an effect on speed. Metal cannot be cut carelessly because this would result in burrs and other inconsistencies on the cut edges. Gas must be applied at high pressure while the cuts are being made to smooth out the issues. Stainless steel, for example, employs nitrogen, whereas carbon steel employs oxygen. The type of gas and the time required to properly apply it can affect the speed of the process, which is another way the process is affected by the material being cut.
when using fiber laser cutting aluminum machine,need gas to help cut,so how about the consumption of gases (nitrogen, oxygen) in liters/hour ? and which type of gas is best for which material?
When cutting carbon steel, the only auxiliary gas used is O2.
When cutting stainless steel, an auxiliary gas such as N2 or O2 can be used.
If O2 is used, the cutting edge will be oxydized, not smooth, and will show a black color.
When N2 is used, the cutting effect is excellent and very smooth.
Consumption of gases (nitrogen, oxygen) in liters per hour, dependent on metal thickness.
NOTE: As an example. One bottle of Liquid Oxygen costs $50 in China.
A standard oxygen or nitrogen gas bottle holds 40L.
40L/40minutes 1mm carbon steel
Carbon steel 2mm 40L/50minutes
Carbon steel 3mm 40L/60min
Carbon steel 4mm 40L/70minutes
Carbon steel 5mm 40L/80minutes
Carbon steel 6mm 40L/90minutes
In terms of carbon steel, The thinner the metal you cut, the less Oxygen pressure you need, because thicker metal sheets will be burned if you use a higher Oxygen pressure.
40L/30minutes 0.5-0.8mm stainless steel
40L/30minutes stainless steel 1mm
Stainless steel 2mm 40L/30minutes
In general, the higher the Nitrogen pressure required, the thicker the metal sheet.
For example, if you cut 1mm stainless steel, use 10kg Nitrogen. If you cut 4mm stainless steel, you’ll need 20kg of Nitrogen.
However, in order to maintain a high cutting speed for thin metal sheets, such as 1mm.
So we recommend that the client adjust the same pressure, all of which are 20kg, in order to ensure not only a high speed of cutting thin metal sheet, but also a high speed of cutting thick metal sheet.
AUTOMATION BY LASER
Automation for laser cutting machines can significantly reduce labor costs and usually allows you to run the laser metal cutting machine in “off” mode. You can significantly increase part production by using automatic loading (from one or more towers) and including automatic unloading / sorting / stacking functions, as well as waste disposal. Of course, this will increase the total cost of the machine, so careful analysis should be performed to determine your company’s optimal level of automation.