Projects
Laser Blanking From Coil Operation Process Introduction
Introduction
The coil fed laser punching line is a sheet metal processing equipment suitable for uncoiling, cleaning, oiling, leveling, feeding, and stacking surface covering plates in industries such as automobiles and steel plate distribution. It has been widely used among automobile manufacturers in developed countries.
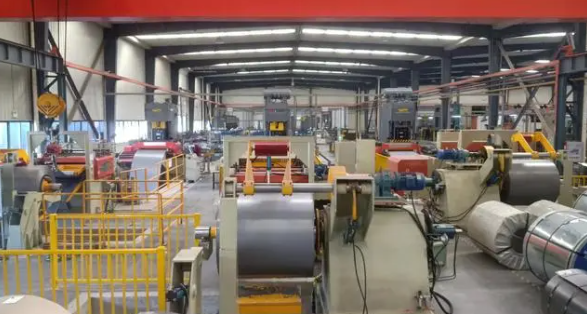
Production mode of laser uncoiling and material cutting
Laser cutting is a thermal cutting method that uses a focused laser beam as the main heat source. Due to the concentration of the laser beam in a very small area, the energy is highly concentrated, which can quickly heat up the local area and evaporate the processing area. In addition, due to the high concentration of energy, only a small amount of heat is transferred to other parts of the steel, resulting in minimal deformation. Laser can accurately cut complex shaped blanks, and the cut blanks do not require further processing. Complex shaped billets can be processed without the need for molds, with high flexibility.
There is a universal strip cutting equipment called flying shear, which works by tracking the cutting process during the strip movement to obtain a certain length of billet. Due to the fact that flying shear involves cutting in motion, it can greatly increase the cutting speed and is currently widely used. However, due to the straight nature of the cutting tool, only rectangular and trapezoidal blanks can be obtained, and its application range is limited.
The existing laser cutting equipment can cut various shapes. When combined with laser blanking systems, the sheet metal is stationary during cutting, and feeding and discharging cannot be carried out simultaneously, which affects the processing speed of the strip. The laser cutting and feeding line cleverly combines the working philosophy of the above two devices, that is, the laser cutting machine performs flying cutting (following cutting) during the belt movement process. Its purpose is to solve the problem of rapid cutting of continuous metal and non-metallic strips without molds, thereby reducing the investment in cutting equipment and mold consumption costs, and effectively improving material utilization.
Complete digitization of the entire line
All equipment on the laser feeding line is controlled by CNC technology, achieving complete digitization and automation of the entire line. The switching of feeding products is convenient and fast, and the status and data of equipment and production can be remotely called, seamlessly connecting to intelligent factories and digital factories. The market process design of the dropped parts can be completely offline through digital design, and online debugging can be completed within 1 hour. The control system can use digital means to drive and adjust all moving parts of the laser feeding line. The feeding products can be switched in a timely manner without the need for equipment adjustment preparation time, significantly improving production efficiency and automation level.
Summary
The coil fed laser cutting line can optimize the trial production process in terms of material savings, cost savings, and flexible procurement strategies.