Uncategorized
Laser Cutting for In-Car Central Control Screen: Precision Manufacturing Leading the Future
Efficient laser processing
With the development of automotive intelligence, in-car central control screens have become an essential component for enhancing the driving experience. Whether for traditional gasoline-powered vehicles or new energy vehicles, an increasing number of models are equipped with larger, higher-resolution screens, including curved and custom-shaped displays, to meet the demands of driver assistance, entertainment, and interaction. However, traditional mechanical cutting and die-stamping processes face numerous limitations when processing these high-precision, complex screens, such as insufficient processing accuracy, severe edge burrs, and low production efficiency. As a result, the industry urgently needs more efficient and precise manufacturing methods to meet the dual market demands for screen quality and production capacity.
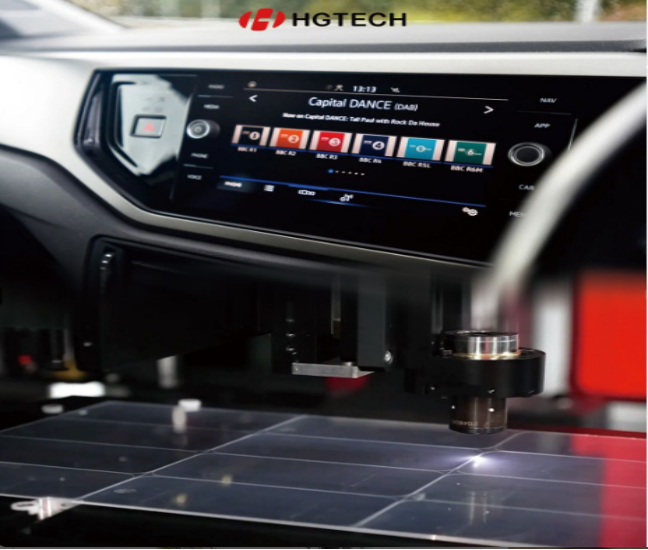
Principle and Advantages of Laser Cutting for In-Car Central Control Screen
Laser cutting is a non-contact processing technology that utilizes a high-energy-density laser beam to cut materials with exceptional precision. The principle involves using the thermal effect of the laser to melt or vaporize the material, enabling high-accuracy cutting. Compared to traditional cutting methods, laser cutting offers the following key advantages in the manufacturing of automotive infotainment displays:
· High Precision and Consistency: Laser cutting achieves micron-level accuracy, ensuring that each in-car central control screens meets the strict dimensional requirements for seamless integration into modern vehicle interiors.
· Non-Contact Processing, Reduced Damage: The laser beam does not physically touch the material, eliminating mechanical stress on automotive glass or polymer display panels, thereby enhancing product durability and reliability.
· Smooth, Burr-Free Edges: Unlike mechanical cutting, which often causes microcracks and burrs, laser cutting delivers clean-cut edges, minimizing post-processing and improving production efficiency.
· Precision for Complex and Custom Shapes: Laser cutting enables the precise fabrication of curved, edge-to-edge, and freeform display designs, meeting the increasing demand for curved in-car central control screens and non-rectangular form factors in modern vehicles.
· High Efficiency and Cost Reduction: Compared to traditional die-cutting and CNC machining, laser cutting eliminates frequent tooling changes, enhances manufacturing flexibility, and supports small-batch, high-mix production, significantly reducing production costs.
Epilogue
As market demand for in-car central control screens continues to rise, laser cutting technology is set to become a key process widely adopted by automakers and supply chain manufacturers. With ongoing breakthroughs in laser processing, in-car central control screens will gain greater flexibility, empowering the automotive industry to move toward a smarter and more user-centric future.
About HGTECH
HGTECH is the pioneer and leader of laser industrial application in China, and the authoritative provider of global laser processing solutions. We comprehensively layout the construction of laser intelligent equipment, measurement and automation production lines, and smart factories to provide an overall solution for intelligent manufacturing.
We deeply grasp the development trend of manufacturing industry, constantly enrich products and solutions, adhere to exploring the integration of automation, informatization, intelligence and manufacturing industry, and provide various industries with laser cutting systems, laser welding systems, laser marking series, laser texturing complete equipment, laser heat treatment systems, laser drilling machines, lasers and various supporting devices The overall plan for the construction of special laser processing equipment and plasma cutting equipment, as well as automatic production lines and smart factories.