Uncategorized
Precision Revolution: Laser Processing for Silicon Steel Sheets
Current Industry Landscape: The Rise of Laser Processing
With the accelerating global electrification trend, industries such as new energy vehicles (NEVs), high-efficiency motors, and smart grids are driving an increasing demand for silicon steel sheets. As a core material for motors and transformers, the processing precision of silicon steel sheets directly impacts the energy efficiency and performance stability of electrical equipment. However, traditional mechanical punching and shearing processes struggle to meet market demands for high precision, low core loss, and flexible manufacturing. Against this backdrop, laser processing has emerged as a breakthrough solution due to its high precision, non-contact nature, and minimal heat-affected zone (HAZ). In recent years, with the advancement of fiber laser technology, laser cutting and laser micromachining have been increasingly applied to silicon steel sheet processing, providing a high-performance and cost-effective solution for the industry.
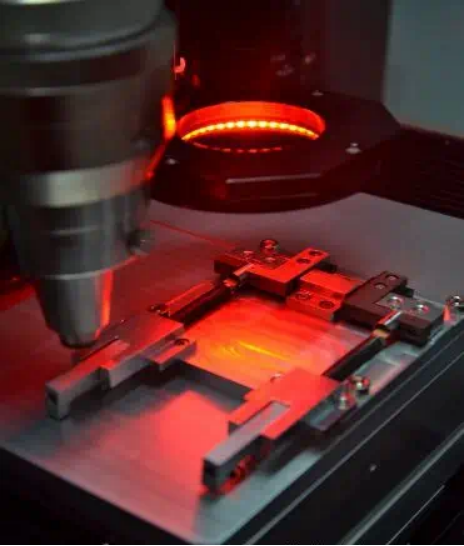
Challenges in Traditional Processing and the Superiority of Laser Technology
Traditional silicon steel sheet processing methods, such as punching and mechanical shearing, involve direct tool contact, which leads to edge burrs, microcracks, and residual stress, negatively impacting magnetic permeability and increasing core loss in motors and transformers. Additionally, progressive die stamping has limited tool life, requiring frequent maintenance and replacement, which increases operational costs. Furthermore, with the rise of NEVs and high-efficiency motors, manufacturers require customized silicon steel laminations with complex geometries. However, conventional stamping dies struggle to adapt to small-batch, multi-specification production, limiting manufacturing flexibility.
In contrast, laser processing offers significant advantages in silicon steel sheet manufacturing:
High Precision, No Mechanical Stress: Laser cutting eliminates mechanical deformation, providing smooth edges, reducing burr formation, and minimizing core loss, which significantly enhances the efficiency of stators and rotors.
No Need for Tooling: Unlike traditional stamping dies, laser processing enables direct digital control, supporting variable production and on-demand manufacturing, making it ideal for NEV drive motors and high-efficiency transformers.
High Automation and Intelligent Manufacturing: Laser processing integrates CNC control, real-time monitoring, and AI-assisted optimization, reducing human intervention, improving consistency, and lowering production costs.
Recent advancements in ultrafast lasers and precision laser micromachining have further expanded the potential of laser processing for silicon steel sheets. For instance, ultrashort pulse lasers (USP lasers) enable high-precision microprocessing of thin-gauge silicon steel, reducing HAZ and ensuring superior magnetic properties. Additionally, by integrating machine vision, AI-driven process optimization, and real-time monitoring, laser processing achieves higher efficiency and adapts to rapid model switching, meeting the stringent demands of next-generation electric machines. With continued advancements in laser technology, its applications in silicon steel processing will become even more widespread, driving the transformation of motor and transformer manufacturing.
Epilogue
As NEVs, renewable energy systems, and smart grids continue to grow, the demand for high-performance silicon steel laminations will increase significantly. Laser processing will play a crucial role in improving manufacturing efficiency and product quality. With advancements in fiber lasers, ultrafast lasers, and intelligent manufacturing, the cost-effectiveness and scalability of laser cutting will continue to improve. Moving forward, laser-based processing will become the standard for silicon steel lamination manufacturing, providing high precision, high efficiency, and lower operational costs, ultimately supporting the global shift toward energy-efficient electrical systems.
About HGTECH
HGTECH is the pioneer and leader of laser industrial application in China, and the authoritative provider of global laser processing solutions. We comprehensively layout the construction of laser intelligent equipment, measurement and automation production lines, and smart factories to provide an overall solution for intelligent manufacturing.
We deeply grasp the development trend of manufacturing industry, constantly enrich products and solutions, adhere to exploring the integration of automation, informatization, intelligence and manufacturing industry, and provide various industries with laser cutting systems, laser welding systems, laser marking series, laser texturing complete equipment, laser heat treatment systems, laser drilling machines, lasers and various supporting devices The overall plan for the construction of special laser processing equipment and plasma cutting equipment, as well as automatic production lines and smart factories.