Projects
Laser Welding To Ensure The Quality Of Pressure Vessels
Welding of pressure vessels
Laser welding machine is an important equipment for ensuring the quality of pressure vessel production.
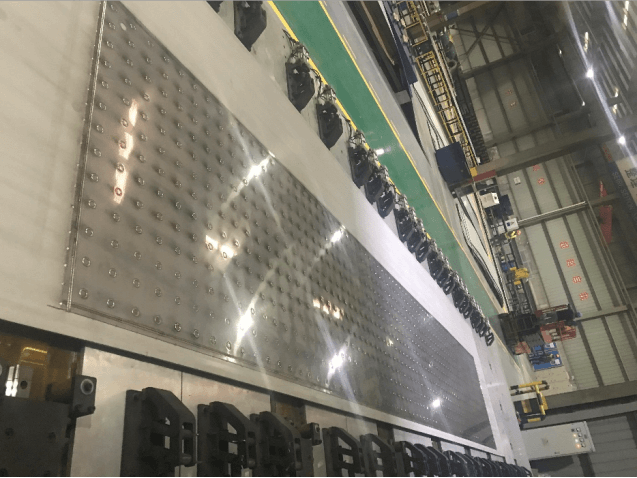
The traditional welding methods for pressure vessels mainly include electrode arc welding, submerged arc automatic welding, gas shielded welding, etc. Although these methods meet the production needs of pressure vessels to a certain extent, they also have some shortcomings and problems, such as:
2. The welding quality is unstable and prone to defects such as poor weld formation, cracks, and pores, which affect the strength and sealing of pressure vessels.
3. During the welding process, a large amount of smoke, noise, and electromagnetic radiation are generated, which are harmful to the environment and personnel health.
4. Welding operations require highly skilled workers with high requirements for the site and equipment, and are not suitable for pressure vessels with complex shapes and positions.
In order to overcome the shortcomings of traditional welding methods and improve the manufacturing level and competitiveness of pressure vessels, laser welding technology has been widely applied in pressure vessel manufacturing in recent years. Laser welding uses a high-energy density laser beam as a heat source to instantly heat the welded material to a molten or vaporized state, and after cooling, forms a solid connection.
The advantages of laser welding mainly include the following:
High fusion strength: Laser welding can generate a high-strength fusion zone, enabling good bonding of materials at the welding site.
Wide welding range: Laser welding can weld various materials, including metals, plastics, glass, and other materials.
Fast speed: Laser welding is fast and can improve production efficiency.
High degree of automation: Laser welding can achieve automation, ensuring the quality and consistency of welding.
Energy conservation and environmental protection: During laser welding, there is no smoke or noise generated, which has a small impact on the environment and also saves energy.
In short, laser welding of pressure vessels is an advanced welding technology with advantages that traditional welding methods cannot compare, and is an important innovation in the field of pressure vessel manufacturing. With the continuous development and improvement of laser technology and equipment, laser welding of pressure vessels will play an important role in more fields and occasions.