Projects
Unlocking the Full Potential of 3D Five-Axis Laser Equipment: Tips for Maximizing Cutting Efficiency
The development of automotive lightweighting has made energy efficiency, environmental friendliness, and safety essential considerations in the automotive design and production process. High-strength hot stamping of steel plates can reduce fuel consumption and improve passenger comfort while ensuring automotive safety performance. Currently, it is mainly used to manufacture important structural components such as B-pillars, A-pillars, front/rear bumpers, front/rear door impact beams, thresholds, floor-through channels, roof longitudinal beams, roof side beams, window reinforcement ribs, door panel reinforcement ribs, cross braces, suspension mounting brackets, and longitudinal load beams in cars, making it suitable for processing using three-dimensional laser cutting methods. Compared to two-dimensional laser cutting, three-dimensional workpiece laser cutting involves more complex machine tools and programming, as well as auxiliary devices such as fixtures. Laser cutting of automotive body stampings needs to ensure both cutting quality and precision while considering cutting efficiency.
Below, using HGTECH’s 3D five-axis laser cutting equipment as an example, we will share some tips for the cutting process.
- Reliable Blank Workpieces
During the forming process, workpieces may experience issues such as fractures, burrs, wrinkles, and springback, resulting in slight deformations and dimensional errors. 3D five-axis laser cutting machines can automatically compensate for these errors through floating axes to ensure proper processing. Processing heavily distorted stamped parts with significant dimensional errors may lead to unstable cutting quality and precision. In severe cases, it can even cause collisions with the 3D laser cutting head, resulting in damage to the nozzle and ceramic ring. To achieve stable cutting quality and precision, it’s essential to start with qualified blank workpieces. Furthermore, having high-quality molds is a prerequisite for stable blank workpieces. Timely repairing worn-out molds is necessary to ensure the production of compliant components.
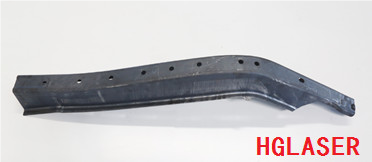
- Reliable Fixtures
Fixtures must align well with the workpieces and incorporate light shields in certain laser cutting areas to prevent the laser from burning or penetrating the workpiece on the other side. For most mass production lines, dedicated conformal fixtures (Figure 2) are commonly used. These fixtures offer high precision, minimal deformation, excellent stability, reusability, and the option to install electronic clamps and workpiece detection devices, which contribute to ensuring continuous and stable equipment production. On the other hand, grid temporary fixtures (Figure 3), while lacking some reliability and stability, are simple and quick to produce, cost-effective, and particularly suitable for processing in small-batch prototyping industries. They are widely used in mold manufacturing and even in some hot-forming production lines.
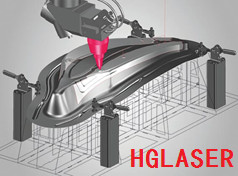
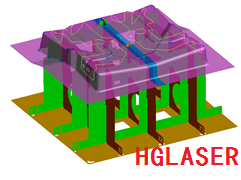
- Proper Programming
Arrange a rational cutting sequence, aiming to minimize the rotation and swing of the cutting head while ensuring the completion of the cutting process. The primary goal is to minimize unnecessary retracing of paths, which can significantly save cutting time and improve production efficiency. For example, in Figure 4, the cutting of a certain A-pillar is shown. In Figure 5 and Figure 6, two different toolpath sequences are illustrated. Figure 5, with fewer swinging movements of the cutting head, is faster in cutting the same workpiece than the program shown in Figure 6.
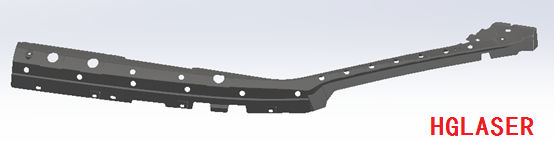
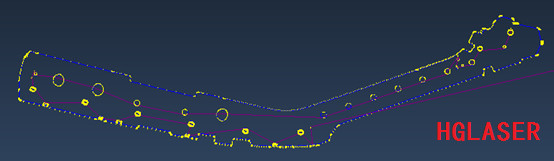
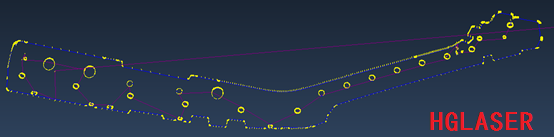
With HGTECH’s exemplary 3D five-axis laser cutting equipment serving as our guiding example, we’ve already uncovered valuable insights into reliable blank workpieces, dependable fixtures, and proper programming. In the chapters that follow, we will discuss the optimization of cutting actions, the precise setting of cutting parameters, and the selection of large-sized workpiece cutting formats, among other important considerations. Stay tuned for an in-depth exploration of these critical facets, as we continue our journey toward precision, efficiency, and excellence in laser cutting technology.