Projects
What Are the Key Factors Influencing the Laser Lap Welding of BIW Parts? (1)
As a highly advanced welding technique, laser welding is generally preferred for application in parts where stringent welding quality is required. In such parts, if spot welding is chosen, the limited welding space would lead to intricate process arrangements, resulting in subpar welding quality and an inability to achieve the desired visual quality effects in line with the design. For instance, areas such as the roof and rear door sections of a vehicle possess elongated welding zones and also require considerations for the vehicle’s sealing integrity. The side panel area presents complexities due to both its elongated form and intricate shape. The door opening zone’s elongated and flat welding space, offering ample room, lends itself to laser welding as a substitute for spot welding, enhancing the effectiveness of door seal strip sealing.
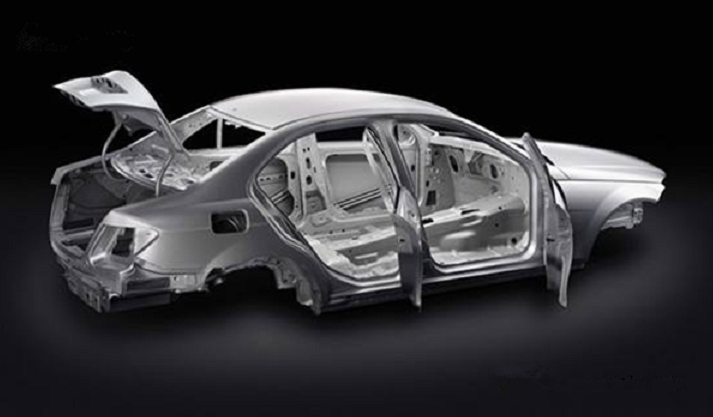
Factor 1: Incident Angle
Body-in-white consists of an array of intricately structured components. However, in certain welding positions between these components, space limitations pose challenges when employing laser welding. What can occur is that the interference between the welding joint and the workpiece, or the obstruction of the laser beam by other parts of the workpiece or nearby fixtures. In such situations, it becomes necessary to deflect the welding joint at an angle before welding can commence. This change disrupts the ability to maintain the laser beam’s perpendicular incidence onto the workpiece surface during the welding process, giving rise to an incident angle of the beam.
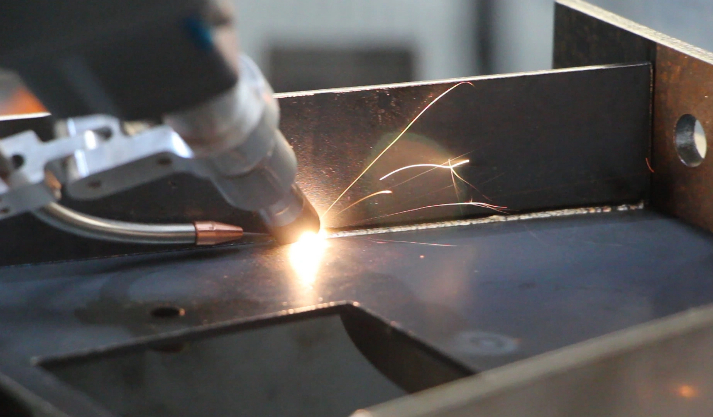
This transition of the welding joint from a perpendicular orientation to an angled one represents a shift in the laser beam from vertically incident to obliquely incident on the workpiece surface. As the angle of inclination increases, with the beam entering the surface at a certain angle, the effective area of the light spot on the workpiece surface enlarges. This results in an expanded welding area, accompanied by an increase in energy loss due to reflection, consequently exerting a certain influence on the welding quality.
For joints with the same material but varying plate thicknesses, deflecting the incident angle of the beam has a more pronounced impact on the formation of weld seams on thicker plate surfaces compared to their effects on thinner plate surfaces. This is primarily due to the enlargement of the incident angle, transforming the circular laser spot into an elliptical shape, which enlarges the welding area. The decrease in laser power density applied to the workpiece due to the larger welding area and angle of incidence leads to reduced laser penetration capability. Furthermore, due to inclined incidence, the effective thickness of the actual welded plate increases.
Additionally, with an increase in the beam’s deflection angle, the energy loss due to reflection also rises. Particularly when welding thicker plates, maintaining process stability becomes challenging. Once energy loss reaches a certain threshold, it affects the surface formation of the weld seam. Moreover, further increasing energy loss due to higher deflection angles can prevent the plates from achieving complete penetration. In contrast, when welding thinner plates, the influence of energy loss on process stability is relatively minor compared to thicker plates, resulting in a slightly smaller impact on weld appearance and performance. After the laser beam is deflected at an angle and inclined onto the plate surface, the Gaussian-distributed laser energy within the focused spot enters the plate’s interior at varying depths. For thin plates, sufficient melting and solidification of the joint can occur to form a weld seam. However, for thick plates, due to energy loss, the welding process becomes less stable, leading to potential welding defects. Regardless of whether dealing with thin or thick plates, as the incident angle increases, a portion of the focused energy gradually penetrates deeper into the workpiece, thus causing an enlargement of the fusion width between the two plates.
Concerning joints with the same thickness but varying material, the influence of the incident angle on weld seam formation also varies, predominantly determined by the ease or difficulty of welding the respective materials.