Projects
What Are the Key Factors Influencing the Laser Lap Welding of BIW Parts? (2)
Factor2: Overlap Joint Gap Between Two Panels
During the stamping process of vehicle body components, springback deformation is prone to occur, resulting in a certain gap between the overlapping joints of the two components even under a specific clamping force. Due to the impact of zinc vaporization in galvanized steel plates used for the vehicle body, the requirements for weld seams in the form of overlap joints are relatively high in terms of body dimensions and welding fixtures. Particularly, the gap between the overlapping sheets needs to be reasonably controlled to facilitate the escape of zinc vapor. Otherwise, a significant number of welding defects may arise during the welding process, leading to a decline in the quality of the weld seam. The gap has a considerable influence on the formation of the weld seam.
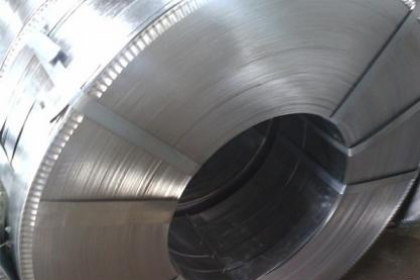
When the overlap gap is appropriate, the welding process remains stable, resulting in a more uniform weld seam formation without quality defects such as porosity and spattering. In the laser welding process, when the gap between the sheets is small, a portion of rapidly expanding zinc vapor escapes through the gap, while another portion escapes through small holes formed due to the molten pool and keyhole effects in the weld seam. The expansion of zinc vapor can easily cause defects like splatter depressions and pores. If the gap is too large, the two components cannot fuse together. Therefore, the mating gap between the overlapping joints of the components to be welded is one of the critical influencing factors in the vehicle body welding process.
In cases where a larger gap exists between the panels, resulting in molten welding connection between the upper and lower panels with surface depressions and root shrinkage defects in the weld seam, improvements in weld seam formation can be achieved by optimizing other process parameters. Firstly, while keeping other parameters constant, optimizing the focal point position can help rectify defects arising from a larger gap between the panels. When there is significant depression on the upper and lower surfaces of the overlap joint weld seam due to a substantial gap between the panels, improving the weld seam formation can be achieved by reducing the welding speed. Compared to the method of optimizing the laser beam’s focal point position to enhance surface quality, the speed reduction approach is more suitable for industrial production. This is because measuring the precision of the beam’s focal point position for different welding positions on the vehicle body requires high accuracy, and visual estimation can result in significant errors, making it challenging to precisely determine the focal point position. Additionally, the impact of the focal point position on weld seam formation is substantial. Therefore, when the gap between the panels of the vehicle body welding area is large, and the weld seam exhibits severe surface depressions or the two panels cannot be effectively fused, the speed reduction approach is generally employed to enhance welding quality.
For sheet materials of the same composition and thickness but with different melt widths on the weld seam surface, the influence of the panel gap on the joint’s tensile-shear load-bearing capacity should also vary. When the weld seam’s surface melt width is relatively large, the gap cannot be too small, or else the mechanical performance of the joint would deteriorate. This is primarily due to the fact that with an increase in the weld seam’s melt width, the volume of high-temperature molten material increases. The substantial expansion of zinc vapor, when hindered by a very small gap, cannot escape promptly. This can lead to the formation of zinc pores within the joint or uneven surfaces on the weld seam, subsequently resulting in a decrease in the joint’s mechanical performance. Therefore, when performing laser lap welding on sheet materials with a zinc coating, it’s not a one-sided assumption that a larger weld seam width equates to better mechanical performance of the joint. For vehicle body components with larger overlap gaps in the welding area, achieving a larger melt width on the weld seam through improved process parameters can fulfill the mechanical performance requirements of the joint.