Projects
Wide Prospects for Laser Precision Manufacturing
In recent years, consumer electronics products such as mobile phones and tablets have shown explosive growth, with huge growth rates and more stringent quality requirements driving technological innovation in manufacturing processes. In this context, laser technology, which has obvious advantages, has become a new favorite in the manufacturing industry, and this seemingly high-end technology has embarked on the pace of industrialization.
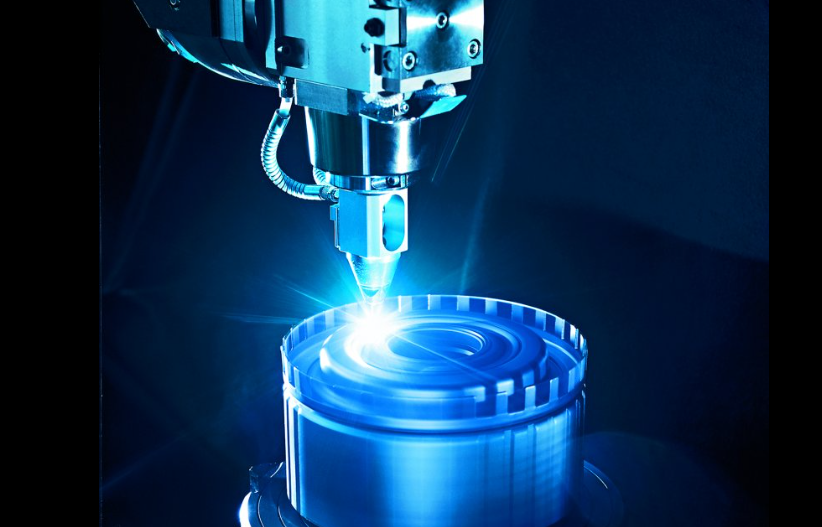
Although laser processing has great advantages in many fields, the overall industrialization time is not long. Compared with traditional machining processes that have experienced precipitation for more than 200 years and have already penetrated various industries, the share of laser processing is still very small. This article discusses the application of laser technology in the micro machining market.
Currently, the share of lasers in the micro processing market is small, mainly due to two reasons. On the one hand, there are operating costs. Traditional processes can achieve batch synchronization, such as using a punch to punch holes. A mold can have four, six, or even more holes simultaneously, while lasers must cut one by one. In contrast, laser efficiency is lower and production costs are higher. On the other hand, there is investment cost. The price of laser equipment is far higher than traditional machining equipment, and the single investment is too high and the return expectation is insufficient. Therefore, most processing enterprises do not choose laser equipment as their main productivity.
With the application of picosecond and femtosecond lasers, many problems existing in laser cutting in the past have been alleviated or resolved, including cracks, edge collapses, and blackening of the cutting surface. At the same time, electronic products are gradually moving towards miniaturization and miniaturization, and the accuracy requirements for small areas are also higher. Traditional machining processes are increasingly difficult to meet the requirements, while small laser spots can easily complete high-precision processing tasks. For example, small apertures below 50 microns are where lasers can display their skills.
Although the current proportion of precision laser processing applications is not large, this trend is bound to be positive. For example, Apple’s 5G antenna is currently all using picosecond laser cutting. In fact, laser and traditional technology are complementary rather than completely substitutive. For example, in the removal of large quantities of materials, traditional machining processes can be completed with a knife at once, while laser cutting one by one is too inefficient. However, laser processing has unparalleled advantages in processing small areas that require high dimensional accuracy. Therefore, although the current market share of laser is small, there is definitely room for large-scale growth in the future.
Starting with the most difficult processing of medical devices, with the accumulation of high-precision tube cutting technology and high-efficiency planar cutting technology in the medical industry, precision laser processing has become more and more comfortable after entering the field of electronic device processing. Currently, precision laser processing has entered the fields of 3C industry, automobile industry, military industry, and other fields, including personalized opening feature molding processing such as mobile phones, laptops, stylus, electronic cigarettes, smart speakers, engine valve cores, and shaped tubes. These fields also require high-speed and high-precision precision laser processing system solutions, and precision laser processing has great advantages in this regard.
The market prospect of precision laser processing is still very broad. Although the current cost and batch efficiency of precision laser processing equipment do not have advantages compared to traditional machining equipment, with the acceleration of the localization process of laser core components, laser application technology is becoming more mature, and intelligent and automated technologies are integrated. precision laser processing will develop towards a direction of lower cost, higher efficiency, and less labor. In the future, laser technology and traditional machining processes will complement each other and jointly assist the development of the manufacturing industry.
About HGSTAR: HGSTAR is is a sub-brand of HGTECH.HGTECH the pioneer and leader of laser industrial application in China, and the authoritative provider of global laser processing solutions. We have comprehensively arranged laser intelligent machine, measurement and automation production lines, and smart factory construction to provide overall solutions for intelligent manufacturing.