Projects
Laser Cleaning Technology for Restoring the Natural Color of Metals
The original intention of laser cleaning is to restore the true color of the metal without damaging the substrate. Metal corrosion can easily cause significant losses. According to statistics, the scrap of steel equipment and materials due to metal corrosion each year accounts for about 30% of steel production, and the annual loss caused by metal corrosion in China can reach over 100 billion yuan. Therefore, metal rust removal has become a major problem that must be faced in the metal industry.
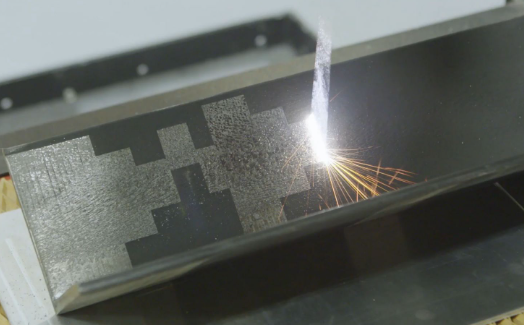
Traditional surface treatment uses mechanical, hydrocarbon, acid pickling, and other processes to clean, deburr, degrease, and remove oxide layers on the surface of the workpiece. During the treatment process, chemical solutions are used, resulting in a large amount of wastewater and exhaust gas, which seriously pollutes the environment.
With the rapid development of China’s economy, the demand for cleaning in industries such as mold, microelectronics, mechanical components, urban construction, and large-scale equipment is also increasing. Traditional cleaning processes (such as sand blasting, polishing, chemical agents, etc.) are highly polluting and inefficient, and are no longer sufficient to meet the needs of market development and environmental protection. Developing more efficient, environmentally friendly, stress free, and non-destructive laser cleaning technologies is imminent, and breaking through the bottleneck of laser cleaning core technology has become a top priority.
Laser cleaning is a new and efficient environmentally friendly cleaning technology, characterized by no grinding, non-contact, no thermal effects, and suitable for cleaning objects of various materials. It is considered the most reliable and efficient cleaning tool, and can remove all traces of residual grease. The traditional cleaning industry mostly uses chemical agents and mechanical methods for cleaning, often causing harmful effects on the environment. In order to reduce environmental damage and provide high-quality and efficient manufacturing processes, laser cleaning machines were born.
Principles of laser cleaning
The process of laser cleaning depends on the characteristics of the optical pulses generated by the laser, based on the photophysical reactions caused by the interaction between high intensity laser beams, short pulse lasers, and pollution layers. The physical principles can be summarized as follows:
The light beam emitted by the laser is absorbed by the contamination layer on the surface to be treated.
The absorption of large energy forms a rapidly expanding plasma (highly ionized unstable gas), generating shock waves.
The shock wave causes the pollutants to become debris and be eliminated.
The light pulse width must be short enough to avoid the accumulation of heat that can damage the treated surface.
Experiments show that when there are oxides on the metal surface, plasma is generated on the metal surface.
Plasma is only generated when the energy density is above a threshold, which depends on the contaminated or oxidized layer being removed. This threshold effect is important for effective cleaning while ensuring the safety of the substrate material. There is also a second threshold for the appearance of plasma. If the energy density exceeds this threshold, the substrate material will be destroyed. In order to effectively clean the substrate material while ensuring its safety, it is necessary to adjust the laser parameters according to the situation, so that the energy density of the optical pulse is strictly between two thresholds.
Each laser pulse removes a certain thickness of contamination layer. If the contamination layer is thick, multiple pulses are required for cleaning. The number of pulses required to clean the surface depends on the degree of surface contamination. An important result of the two thresholds is the self-control of cleaning. A light pulse with an energy density higher than the first threshold will continue to remove contaminants until it reaches the substrate material. However, because its energy density is lower than the damage threshold of the substrate material, the substrate will not be damaged.
Laser cleaning equipment is a new generation of high-tech intelligent products for surface cleaning, which can be cleaned without chemical reagents, media, dust, and water. Automatic focusing can be achieved, with the advantage of high cleaning surface cleanliness. Compared to traditional rust removal methods, laser cleaning has high efficiency and truly does not damage the substrate, making it a favorite in metal rust removal.
About HGSTAR: HGSTAR is is a sub-brand of HGTECH.HGTECH the pioneer and leader of laser industrial application in China, and the authoritative provider of global laser processing solutions. We have comprehensively arranged laser intelligent machine, measurement and automation production lines, and smart factory construction to provide overall solutions for intelligent manufacturing.