Projects
Automated Laser Welding: Application and Advantages of Laser Welding in Automotive Body-in-White
“Body in White” refers to the car body after welding but before painting. After painting, the Body in White, along with interior and exterior trim, electronic and electrical systems, powertrain, and chassis systems, forms the complete vehicle. Thus, the Body in White serves as the foundation for vehicle manufacturing.
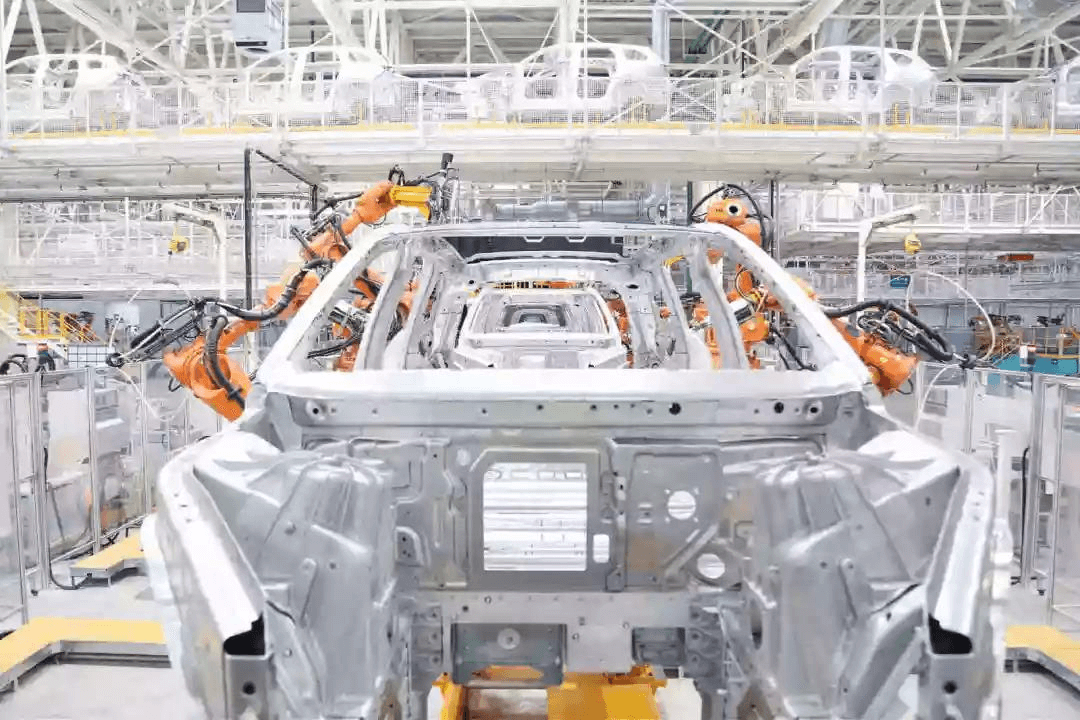
Meanwhile, laser processing has become an indispensable technology in modern automotive manufacturing. Internationally, renowned automotive companies are eagerly adopting laser welding technology in body construction to ensure product quality and technological advancement.
Body in White is a crucial part of the car, significantly affecting overall functionality. Generally, it can be divided into 20 major assemblies. The use of laser welding can reduce overlap widths and certain reinforcing components, as well as compress the volume of the body structures, thereby realizing lightweight body. Automated Laser welding is employed for welding the roof shell、body frame and the transmission converter cover plate. Controlled by CNC, the cycle time is approximately 16 seconds, with actual welding time as short as 3 seconds, allowing continuous operation 24 hours a day.
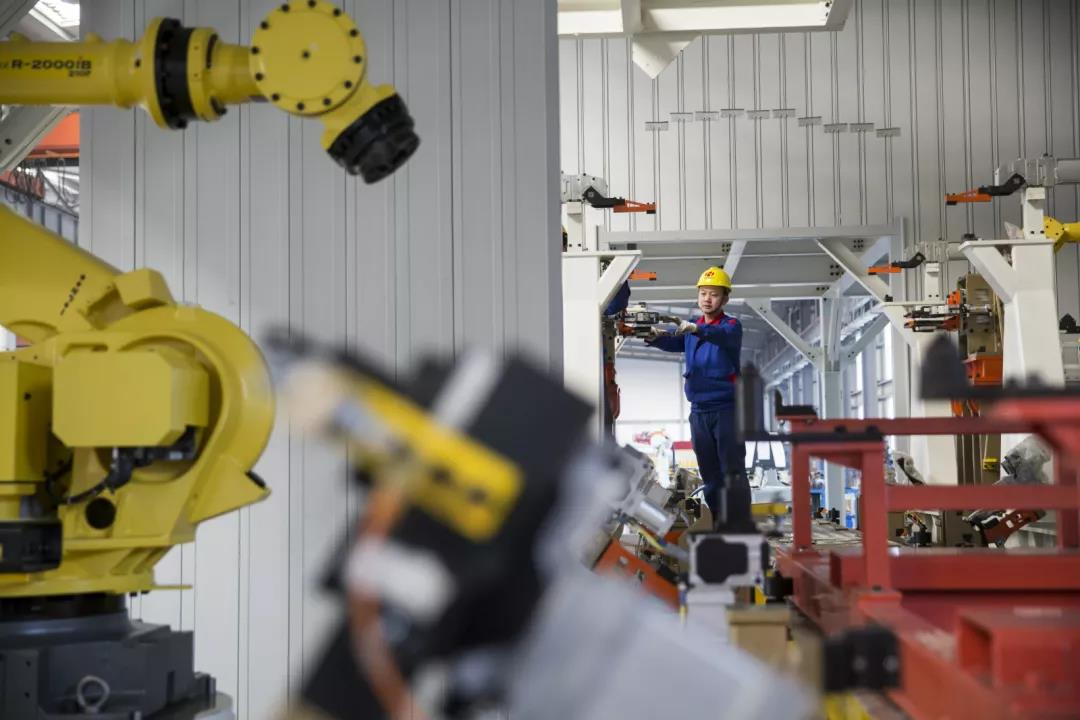
Online Body in White automated laser welding is primarily used for the welding of body frame structures, such as the welding of roof panels and side panels. Traditional resistance spot welding methods have gradually been replaced by laser welding. Laser welding technology can enhance product design flexibility and reduce manufacturing costs. The width of joints between workpieces can also be minimized, reducing material usage and increasing the stiffness of the vehicle body, thereby enhancing product competitiveness.
Furthermore, traditional spot welding often leads to issues such as water leakage around the roof seams during rainy weather, necessitating the addition of rubber seals to address these problems. In contrast, laser welding technology eliminates the need for rubber seals and mitigates potential water leakage caused by poor assembly quality.
From manufacturers’ perspective, traditional spot welding involves overlapping the two components, which increases the consumption of steel. Additionally, spot welding suffers from discontinuities; the joint area of the panels is noticeably less compared to the more continuous welds achieved by laser welding, thereby reducing the stiffness of the body. Another benefit of automated laser welding is the ability to reduce material usage, reduce costs and improve dimensional accuracy.
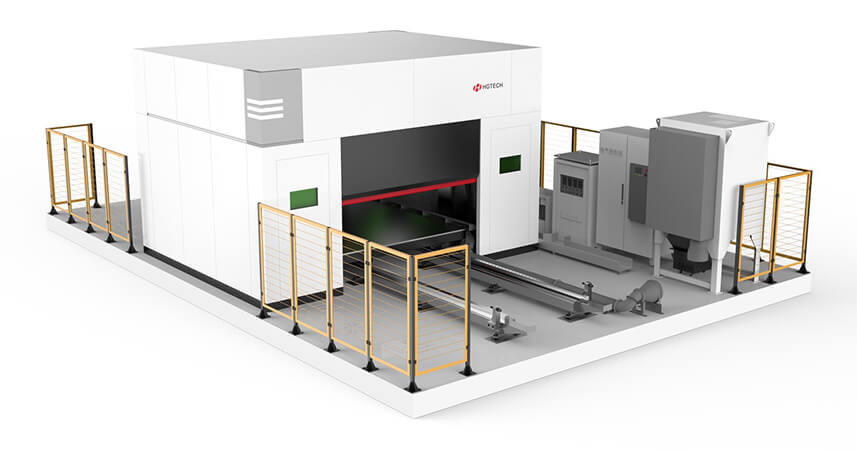
Currently, HGTECH’s independently-developed Body-in-White Automated laser Welding Production Line has achieved five major innovations and surpassed seven benchmarks in the history of global automotive manufacturing technology. It has been granted 26 invention patents, 40 utility model patents, and more than 20 software copyrights, marking a significant breakthrough in advanced laser manufacturing technology in the automobile manufacturing sector.
We are:
Faster
In mass production models: Laser brazing speed reaches 120 mm/s, laser flying welding speed reaches 180 mm/s, ranking first in efficiency in China.
Better
High equipment stability, excellent welding quality, low welding defects, with a qualification rate of over 99%, leading the industry.
Updating:
Currently, our equipment applications have expanded from traditional fuel vehicle manufacturers to include the field of clean energy vehicles.
Enhanced:
We have mastered the technical standards of various domestic and international automobile enterprises, providing customers with comprehensive systematic technological solutions and specialized process support services.
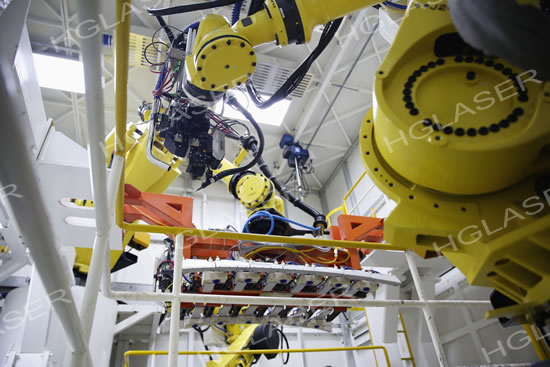
HGTECH welding technology has become more automated, intelligent, and flexible, evolving from being applicable to a single vehicle model to facilitating mixed-line production for multiple models. The advancement in technology reflects our determination to explore and our acute market sensitivity.