Projects
How To Avoid Burrs When Laser Cutting
Preface
There are countless application cases of laser cutting machines in metal material processing. Due to their high work efficiency and high cutting quality of finished products, they have become standard equipment in metal sheet processing stations. But some customers may experience slight burrs on the front and back surfaces of the sub materials when using laser cutting technology. This situation is usually caused by improper operation. Next, we will discuss the reasons for burrs generated by laser cutting and the solutions.
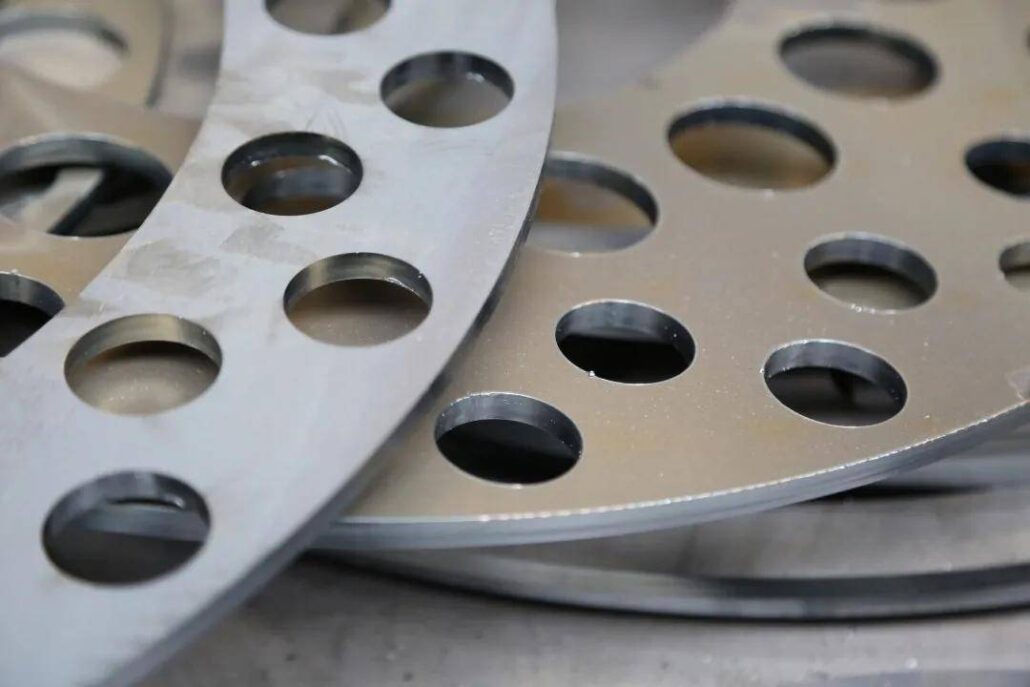
The reasons for burrs generated by laser cutting
The auxiliary gas purity of laser cutting equipment does not meet the required standards, which can also cause burrs on the workpiece.
The output power of laser cutting equipment is insufficient, and the metal cannot evaporate effectively, resulting in a large amount of slag and burrs.
The working time of laser cutting equipment is too long, resulting in unstable working conditions and burrs.
The deviation of the laser beam focus generated by the laser cutting system results in incomplete energy concentration on the workpiece, incomplete vaporization of the workpiece, increased amount of slag generated, difficulty in blowing off, and easy generation of burrs.
Solution to Burrs Caused by Laser Cutting
It is necessary to equip an air compressor and use auxiliary gas for laser cutting process, with high gas purity. It is possible to switch to a gas supplier with better quality, and it is best not to use steel cylinder gas because the purity is poor after two rounds of filling, which wastes gas.
When laser cutting stainless steel materials, it is recommended to use nitrogen as an auxiliary gas. In the process of laser cutting, nitrogen, as a flame retardant gas, can not only prevent the explosion point phenomenon of laser cutting, but also the heated end face will not instantly oxidize, making the cutting end face smoother. The auxiliary gas should be adjusted to a pressure of 12-15 kilograms. The nitrogen under this pressure will not completely prevent combustion and can quickly blow away waste, achieving the effect of deburring.
Some parameters of the laser cutting system can also affect the appearance of the slag, leading to burrs in the metal laser cutting machine. Therefore, professional operators are needed to debug the parameters of the metal laser cutting machine. The cutting parameters should be adjusted to the best, and the air pressure, flow rate, focal length, and cutting speed should be adjusted multiple times. By adjusting the appropriate parameters, exquisite workpieces can be cut.
Epilogue
Laser cutting equipment is a precise machine, and operation is also a delicate task. Usually, a data error can cause its work to run abnormally. Therefore, errors should be reduced and avoided in laser cutting operations. Adjusting the equipment, gas, and parameters to the optimal level can improve the cutting quality of the laser cutting machine.