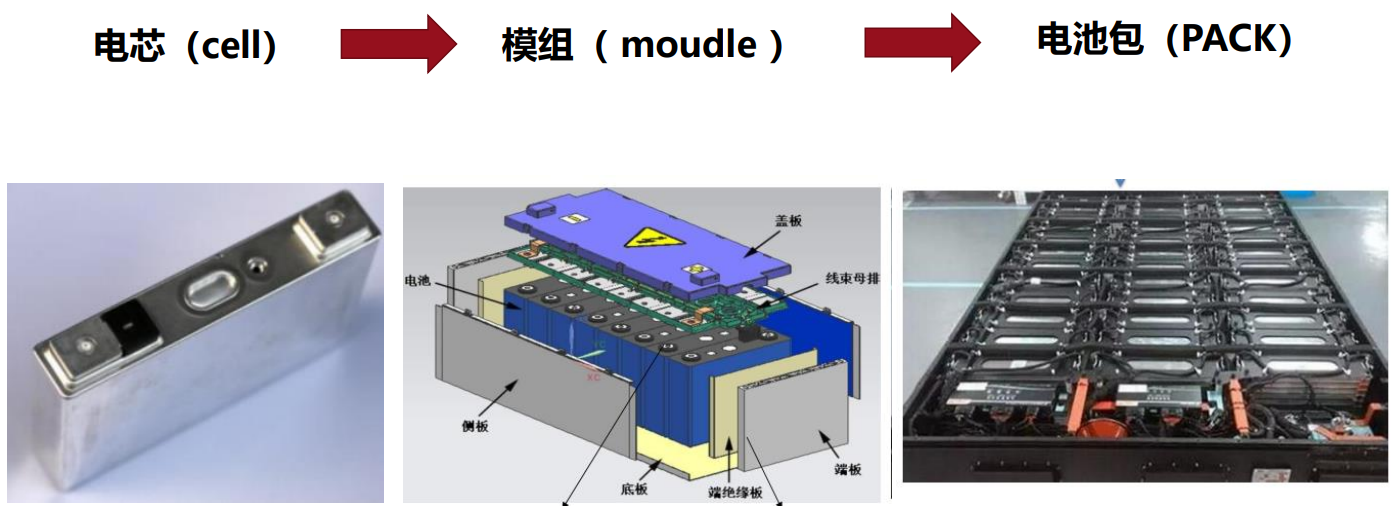
The rapid growth of the electric vehicle market has made power battery production and assembly integral to automotive manufacturing. Battery MODULE and PACK laser welding lines are crucial, performing tasks such as cell assembly, interconnection, testing, and packaging. Their efficiency directly affects battery quality, production speed, and cost control.
What Are Battery Module and PACK Welding and Assembly Line ?
The Battery Module is an intermediate step in the production of power batteries. Its primary task is to combine multiple cells (such as cylindrical, prismatic, or pouch cells) into modular units through a series of precise assembly processes. The stability and consistency of the module are critical for the subsequent PACK assembly process. Typical processes in module production include: cell loading, OCV testing, plasma cleaning, glue application, laser welding, module stacking and strapping.
PACK (Battery Pack) is the process of integrating and completing the modules by assembling them with the cooling system, electrical connection components, casing, and other elements to form the final battery pack. This is the last stage for battery production, ensuring it meets all functional and safety standards. Key processes in BATTERY PACK assembly include: module fixation, liquid cooling system integration, EOL (End-of-Line) testing, accessory installation and airtightness testing.
The technological evolution of battery MODULE and PACK welding and assembly lines is driving the overall advancement of battery manufacturing for electric vehicles. Assembly lines are increasingly moving toward high levels of automation to meet the rapidly growing market demand. In addition, the widespread application of laser technology is playing a critical role in improving process precision and reliability, further supporting the high standards required in modern battery manufacturing.
HGTECH, with years of technological expertise, offers customized solutions for prismatic battery module welding and PACK welding and assembly lines to meet diverse customer needs and drive industry growth.
Battery Module Laser Welding Solutions
- High-Precision Laser Welding: Welding speed 60-100 mm/s, BUSBAR pull force ≥1000N, ensuring stable quality.
- Plasma Cleaning & Adhesive Application: Improves cell surface cleanliness and adhesive bonding for reliable assembly.
- Multi-Function Automation Platform: Features a 6-axis robot, laser cleaner, and 3-axis module, compatible with various cells and modules.
- Comprehensive Testing System: Supports OCV, polarity, and post-welding cleanliness tests to ensure module performance.
Prismatic Battery PACK Line Solutions
- Liquid Cooling System Integration: Automates adhesive application, gas tightness testing, and assembly to ensure high-quality integration.
- EOL & Gas Tightness Testing: Thoroughly tests PACK performance and safety to ensure compliance with industry standards.
- Flexible Automation Design: Dual-layer high-speed conveyors and modular equipment layout enable quick model switching, enhancing production flexibility.
- Intelligent Control & Remote Support: Use MES for data tracking and production management, with remote support for streamlined maintenance.
Application and achievement
HGTECH’s battery MODULE and PACK line solutions have been widely used in the field of electric vehicle battery manufacturing, providing efficient and reliable production support for many leading enterprises. By increasing the degree of automation and detection accuracy, the customer’s production efficiency is increased by more than 20%, and the scrap rate is significantly reduced.
Future outlook
With the growing market of electric vehicles, the demand for battery MODULE and PACK production lines will continue to rise. HGTECH will remain committed to technological innovation, providing customers with smarter, more efficient, and flexible solutions to support green manufacturing and sustainable development in the industry.