Projects
Comparative Analysis of Laser Cutting And Plasma Cutting
At present, there are two main methods for cutting metal plates: plasma cutting and laser cutting. Plasma cutting can be traced back to the 1950s, when it emerged as a substitute for flame cutting. The working principle of plasma cutting is: spray the overheated ionized gas (plasma) from the nozzle to the workpiece at high speed, and then form an arc in the gas. This arc ionizes some gases, forming a conductive plasma channel in the process. When the power from the self-cutting plasma is transmitted along the plasma, it will generate enough heat to melt the workpiece, Subsequently, plasma and compressed gas blow away the hot molten metal, resulting in workpiece separation.
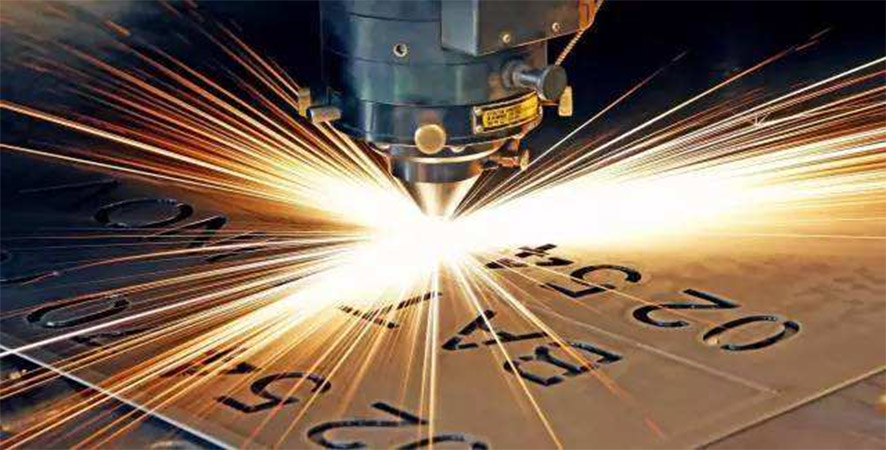
Laser cutting mainly uses two types of lasers; CO laser with operating wavelength of 10.6um and solid state laser with operating wavelength of about lum (disc laser and fiber laser). CO lasers are cheaper, but they are not suitable for cutting copper, brass and aluminum because CO2 lasers cannot work on reflective surfaces. In contrast, solid state lasers have higher processing speed in addition to higher energy/electro-optical conversion efficiency and can process a wider range of materials, because the absorptivity of the above materials to – lum laser is higher than that of~10um laser.
Of course, each cutting method has its own functions and benefits, and each cutting method also has its own applicable fields. In general, the main advantage of laser cutting is its non-contact. It uses heat to cut materials and is more accurate; The main advantage of plasma cutting is that it is suitable for cutting different types of metal.
There are several key differences between laser cutting and plasma cutting:
(1) Cutting technology: plasma cutting uses gas mixture with arc, while laser cutting uses focused beam.
(3) Capital investment required: plasma cutting is relatively low, while laser cutting is relatively high.
(4) Cutting speed: plasma cutting machine is relatively slow; The laser cutting machine can usually cut metal faster than the plasma cutting machine, with less energy consumption, and is a more environmentally friendly metal cutting method.
(5) Cutting thickness: plasma cutting machine can generally cut any type of metal, with thickness up to 80mm. Laser cutting machines can only cut materials up to 25 mm thick.
In the current laser cutting market, the power of fiber laser is increasing, which greatly improves the applicability and productivity of laser cutting technology, and makes laser cutting technology more competitive than mechanical cutting and plasma cutting.
About HGSTAR: HGSTAR is is a sub-brand of HGTECH.HGTECH the pioneer and leader of laser industrial application in China, and the authoritative provider of global laser processing solutions. We have comprehensively arranged laser intelligent machine, measurement and automation production lines, and smart factory construction to provide overall solutions for intelligent manufacturing.