Projects
Different Laser Welding Processes in New Energy Vehicles
Current Development Status of New Energy Vehicles
In 2021, the sales of new energy vehicles in China reached a historic breakthrough of 3.5 million units, with a growth rate of 157.5%. At the same time, the market share continued to increase, reaching 13.4% in 2021; New energy vehicles have become an important increment in China’s automotive industry, which is of great significance for the development of the automotive industry.
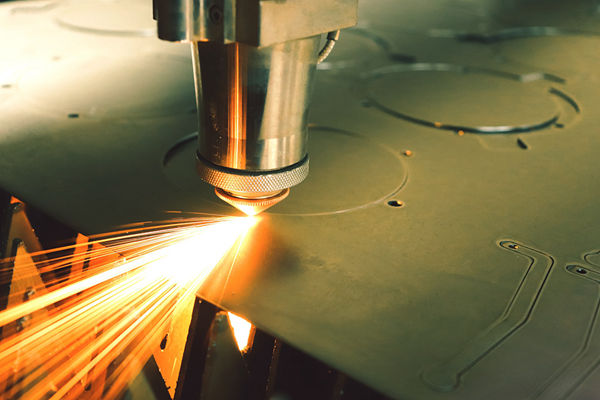
Against the backdrop of global energy conservation and emission reduction, many countries and regions have made the development of new energy vehicles one of their strategic emerging industries. As the core component of new energy vehicles, the power battery industry has been continuously gathering and developing rapidly in recent years. A certain industry report shows that driven by the dual core of new energy in the fields of transportation electrification and energy storage, it is expected that the global lithium battery shipment volume will exceed 14TWh by 2050, and the global lithium battery industry will maintain long-term high growth, forming a huge market size of over one billion yuan. After years of accumulation and precipitation, China has become a leader in the development of power batteries. At present, a complete power battery industry chain covering basic materials, cell monomer, battery system and manufacturing equipment has been formed. The system energy density of ternary lithium batteries and lithium iron phosphate battery is at the international leading level, and more than 10000 recycling service outlets have been built nationwide.
- Body welding
Laser welding is widely used in the automotive industry for the assembly and connection of stamped parts on vehicle bodies. The main applications include roof cover laser welding, trunk cover laser welding, and frame laser welding; Another important application of body laser welding is the laser welding of body structural components (including doors, body side frame, and pillars). The reason for using laser welding is that it can improve the strength of the vehicle body and solve the problem of difficult conventional resistance spot welding in some parts.
Laser self fusion welding refers to the process where two or more parts of a weld melt themselves to form a whole without the need for welding wires or other auxiliary materials. After multiple parts are welded, they self melt into a whole. Laser self fusion welding is mainly divided into two parts in the manufacturing of automotive body, body assembly welding and tailor welding.
Body assembly welding: The body assembly welding mainly includes the welding of the top cover and side wall pillars, tailgate, body bracket, and door. With the demand for product replacement, laser welding is increasingly widely used in the automotive field, and assembly welding has been accepted by most manufacturers. Currently, only Volvo still insists on using laser self fusion welding; In terms of side panels, Ford SUVs and sedans each use laser self fusion welding, and many Volkswagen models are also using it.
- Unequal thickness laser welded blanks
The use of unequal thickness laser welded blanks in car body manufacturing can reduce the weight of the car body, reduce the number of parts, improve safety and reliability, and reduce production costs;Tailored welded blanks are made by welding steel with different strengths, thicknesses, and coatings. Laser welding is widely used due to its fast speed, high accuracy, and small weld seams. Currently, most automotive tailor-welded blanks are made by laser welding.
Compared to the pure steel plate of the old car body, tailor-welded panels have three advantages: the body weight is light, and welding is used to make the panels thinner, thereby reducing the body weight; The overall strength is high, and after the body is composed of welded plates, the strength even exceeds that of the base material body, increasing the safety of the body; The cost is relatively low, and the welding strength and accuracy are higher than traditional materials, reducing the use of parts while ensuring performance. The application of laser welded blanks in car body manufacturing can reduce the number of parts, molds, and welding fixtures, reduce the weight and cost of the car body, and improve the market competitiveness of the product. The main application of tailor-welded blanks in the automotive body is mainly in covering parts, and some are also used in structural parts.
The welding seams of tailor welded blanks in automobiles are mainly divided into the following three types: 1. Single straight line welding seams; 2. Multiple linear welds; 3. Non linear welds. Among them, the single straight seam type is most commonly used, and the production process is also relatively simple. Non linear welds are the most complex and are generally designed based on the shape of the stamped part after forming, in order to improve the strength and stamping performance of the product.
Due to the subsequent stamping and forming of automotive welded blanks, the requirements for the quality and defect control of welded blanks are particularly strict. This mainly includes requirements for appearance (scabs, cracks, inclusions, holes, and scratches, etc.), weld formation (weld width, weld protrusion, effective depth of weld, back fracture, and weld misalignment, etc.), and mechanical properties (tensile, cupping, hardness, and bending tests are conducted on the weld). For example, it is required to fracture in the non weld area during tensile performance testing, and the cracked area during cupping testing cannot be in the weld or cupping value greater than the specified value.
- Welding of gears and transmission components
In addition, various parts of the gearbox can be welded and processed on this equipment, especially the differential case and drive shaft in the sedan gearbox, which are often formed by connecting and welding individual parts after production.
About HGSTAR: HGSTAR is is a sub-brand of HGTECH.HGTECH the pioneer and leader of laser industrial application in China, and the authoritative provider of global laser processing solutions. We have comprehensively arranged laser intelligent machine, measurement and automation production lines, and smart factory construction to provide overall solutions for intelligent manufacturing.