Projects
Dust Removal of Laser Pipe Cutting Machine
Application of Pipe
With the development of science and technology, pipe parts have been widely used in industrial sectors such as aircraft manufacturing, engineering machinery, transportation, petrochemical industry, agricultural and animal husbandry machinery, etc. In production, pipes have the advantages of low production cost, good processability, light weight of structural parts, and material saving. Therefore, pipe cutting plays an important role in the industrial field. Since the shapes, sizes and uses of pipes are different, and the cutting of pipes is restricted by the processing quality. Therefore, it is very important to choose reasonable processing equipment, processing methods and process measures.
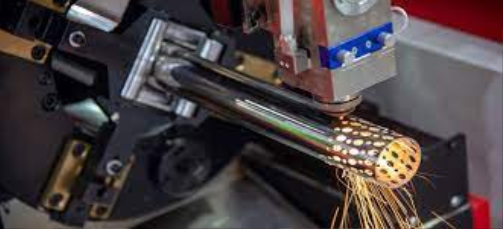
Importance of Pipe Laser Cutter
Traditional pipe cutting methods mainly rely on manual sawing, saw cutter, roller extrusion, grinding wheel cutting, gas welding cutting, etc. These processing methods have the disadvantages of low cutting efficiency and high labor intensity for workers. Pipe laser cutting is widely used in industrial fields due to its advantages of fast processing efficiency and good processing effects. It emits a high-energy laser beam to melt or vaporize the material to be processed after being irradiated by the laser beam, thereby achieving the purpose of cutting.
Generation of Waste Residue
When a laser cutting machine cuts carbon steel, the laser emitted by the laser irradiates the surface layer of the carbon steel. The high temperature generated instantly, under the action of the auxiliary gas, quickly reacts with the silicon, manganese, sulfur, phosphorus, etc. contained in the carbon steel. The elements react, oxidize, melt and vaporize them to penetrate the carbon steel, and then the laser displacement is controlled by CNC to achieve the purpose of cutting.
However, when cutting with a laser pipe cutting machine, the cutting light spot is irradiated on the surface of the pipe to be cut. The surface temperature will reach the melting point or boiling point in a very short time, causing a small hole to be formed inside the pipe at the cutting end, and the auxiliary gas following the cutting light spot will be blown away. Molten material around the holes, and then forming dust. For workpieces that require a clean inner wall of the pipe, these waste residues need to be manually removed later, resulting in a time-consuming and labor-intensive process and low production efficiency.
Generation And Treatment of Carbon Steel Pipe Dust
Generally speaking, the amount of dust produced when cutting ordinary carbon steel pipes is greater than that of pipes made of stainless steel and other materials. This is because ordinary carbon steel is susceptible to environmental influences and is prone to rust and corrosion in a short period of time. A large amount of dust is produced during cutting. dust. Moreover, most ordinary carbon steel has a high carbon content. When it is cut, oxygen is mostly used as an auxiliary gas, but oxidation reactions easily occur on the cutting surface. Although this improves cutting efficiency, it also leads to an increase in dust. Therefore, when cutting carbon steel pipes, the surface of the pipe can be derusted first to reduce the corrosion of carbon steel pipes by oil stains, water stains, etc.