Projects
How effective are aluminium laser welding machines
Aluminum can be a challenging material to weld. Contamination and porosity issues can arise as a result of oxidation issues. However, when properly cleaned and handled, aluminum welds well with a laser.
The Difficulties of Welding Aluminum Aluminum has properties that make it more difficult to weld than other metals. Because of its relatively high thermal conductivity (approx. 209 W/m K) and low melting point (1,221°F/660.3°C), it can only be welded using fusion welding processes.
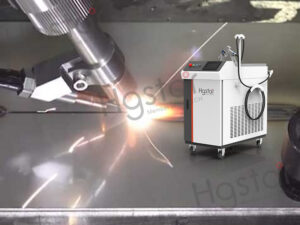
MIG, TIG, Laser, and Electron Beam fusion welding processes generate intense heat in a small area to melt the material in the desired weld area. This small heat affected zone is critical because the high thermal conductivity of aluminum causes heat to travel throughout the work piece, melting too much material or deforming the entire part.
The amount of heat applied, as well as the location to which it is applied, must be precisely controlled. To control these factors, manual welding processes such as MIG and TIG rely on operator skill and heat sinking. Welding processes that rely on visual judgment of material readiness can be unreliable because aluminum does not change appearance as it approaches its melting point. Automated methods, such as Laser and Electron Beam, offer more precise and consistent weld quality by using computers to control feed rate, power, and weld location.
Aluminum Oxidation
Another difficulty in welding aluminum is the formation of an oxide film on the work surface. Aluminum oxide has a melting point that is approximately three times that of pure aluminum, which can result in particles of aluminum oxide contaminating the weld and causing porosity issues. Prior to welding, the oxide film must usually be removed mechanically or chemically. Aluminum oxide can interfere with laser welding because it changes the reflectivity of the part’s surface, reducing the amount of laser energy that reaches the base metal.
Hydrocarbon Contamination
Hydrocarbon contamination of aluminum during storage and preparation can cause welding issues. Prior to welding, aluminum parts are frequently formed, sheared, sawed, and machined. If a lubricant is used during any of these pre-weld operations, it must be completely removed prior to welding to avoid bad welds. Prudence dictates that aluminum parts that are to be welded be pre-weld processed in such a way that minimal to no lubricants are used — sawing and machining of aluminum should be done dry, if possible, and thoroughly cleaned if not.
Aluminum Laser Welding Laser beam welding is one of our most popular aluminum welding services. The method is ideal for producing quick, clean welds. The heat affected zone is reduced, and weld penetration in aluminum can reach up to 0.25″. When combined with an appropriate filler material such as 4032 or 4047 aluminum, laser beam welding can be used with crack sensitive materials such as the 6000 series of aluminum alloys. There are several types of lasers that work well with aluminum, and using a cover gas is often recommended.
Pre-Weld Preparation
The amount of pre-weld preparation required is largely determined by the condition of the aluminum parts to be welded, which is generally determined by storage conditions and the cleanliness of the machine procedures used to produce the part thus far.
Aluminum that will be laser welded must be thoroughly cleaned to avoid oxide films and hydrocarbon contamination. To remove any oxides, this is frequently accomplished mechanically by using stainless steel wire brushes, grinding, filing, or scraping. Chemical cleaning methods that use immersions in caustic solutions and water, on the other hand, are effective at removing aluminum oxide.
In general, acetone or alcohol-based solvents can be used to remove hydrocarbon residue from aluminum parts. When heated, chlorinated solvents can produce toxic gases, so avoid using them in the welding area. Before abrading the surface to remove aluminum oxide, hydrocarbon contamination must be removed.
Joint Preparation
The fabrication of the joint is a critical aspect of welding aluminum. Because aluminum is softer than most metals, special care must be taken during machining and assembly. Contaminates are easily transferred to a part and then pushed beneath the joint surface.
Avoid machining methods that leave a ground or smeared surface. A band saw, for example, will smear metal along the path of the blade. This issue can be solved by filing or machining the joint edge after it has been cut.
If at all possible, avoid the grinding process. If grinding is unavoidable, use a coarse disk.
Use a clean cloth, such as cheese cloth or paper towels, when cleaning a surface with solvents. Shop rags that have been contaminated with oil residue should not be used.
Avoid using compressed shop air to clear debris from the joint area. Moisture and oil contaminates are present in compressed air. If you need to blow off a part, use a bottled gas like nitrogen or argon.
Only use a stainless steel wire brush to clean a joint after it has been cleaned with solvent. Prior wire brushing may have imbedded hydrocarbons and other contaminants in the aluminum.
To clean a joint, always use new or recently cleaned stainless steel brushes. Older brushes on a workbench may contain oils and other contaminants. Brushes used on other metals should not be used because metal flakes can be carried on the bristles and imbedded under the surface of the aluminum during brushing.
Brush any etched metal surface with stainless steel wire. Etching by-product residuals can change the chemical composition of the weld pool.
Clean all wire brushes and cutting tools frequently.
Fixturing
Laser welding necessitates a relatively precise joint in order to maintain allowable gap and mismatch. A good weld fixturing is required to accurately place the laser beam. Laser welding and cutting are thus inherently machine guided processes.
Joint Types
Butt Joint:
It is preferable to have a fit-up tolerance of 15% of the material thickness.
Sheared edges can be used as long as they are straight and square.
Part misalignment and out-of-flatness should be less than 25% of the material thickness.
Lap joint (seam weld or burn-through):
Weld penetration and/or feed speed are severely limited by air gaps between the pieces to be Lap Joint welded.
No gap can be tolerated for round welds in aluminum unless inert gas coverage is maintained over the entire weld area.
Fillet Joint:
Because of the high shrinkage rate of aluminum, this joint configuration is ideal.
Square edges and a good fit are also required.
All of these technologies can produce high-quality aluminum welds, and the method chosen is frequently determined by operational costs rather than weld quality. However, because each process has slightly different characteristics, some types of lasers may be preferable for specific applications, joint configurations, and aluminum alloy combinations.
Laser Welding Modes of Operation
Laser beam energy can be applied to the work piece in a variety of ways, including as a series of pulses, a continuous beam, or as a laser stir weld. The choice of method is determined by the application, the properties of the materials, and so on.
Pulsed Laser Welding
A pulsed laser is exactly that: the beam is switched on and off at a very high rate (10-1000 hz), resulting in a series of separate bursts of energy being applied to the work piece. Each pulse melts a small area of the work piece, which is then moved slightly and another pulse is applied, resulting in a series of overlapping welds that form a continuous bead.
Each weld area created by a pulse cools quickly, reducing the amount of heat in the surrounding material and, as a result, limiting how hot the part can become, reducing melting and distortion of the part. Due to the high thermal conductivity of aluminum, a pulsed laser is generally the best way to laser weld aluminum when a low thermal input is required.
Continuous Wave Laser Welding
Continuous wave laser welding, also known as keyhole welding, is used for deep penetration welds. A constant laser light beam is directed at the work piece, which is then moved beneath the beam. As the trailing edge of the laser beam cools, the material on the leading edge melts. To avoid overheating the parts, continuous wave lasers typically feed at speeds ranging from 25 to 100 inches per minute. Continuous wave welding may be better suited for some of the more crack sensitive aluminum alloys because heat is applied at a constant rate and the part is not subject to the constant heating and cooling of a pulsed laser.