News
Laser welding solves medical industry pain points
Pain Point “New Therapy” in the Medical Industry, Ultrafast Laser Incarnation “Lancet”
Why are UDI codes and strings on medical devices unaffected by pickling and corrosion? How are the extremely small parts of artificial organs tightly welded together?
Today, Laser Jun will demonstrate the magical power that lies behind these fine and tiny “medical miracles” – laser.
HGLASER was invited to take part.
The “Fourth Ultrafast Laser Processing Technology and Industry Summit Forum”
Delivered a speech titled “Ultrafast Laser Applications in the Medical Field.”
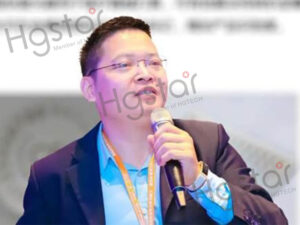
The medical industry is pushing the gas pedal.
The “post-epidemic era” has seen an increase in the construction of the public health system, disease control systems, and primary medical care, as well as a rapid increase in the localization of medical devices. The medical device market has grown at a rate of more than 20% in recent years, and the market needs to be thoroughly researched and expanded.
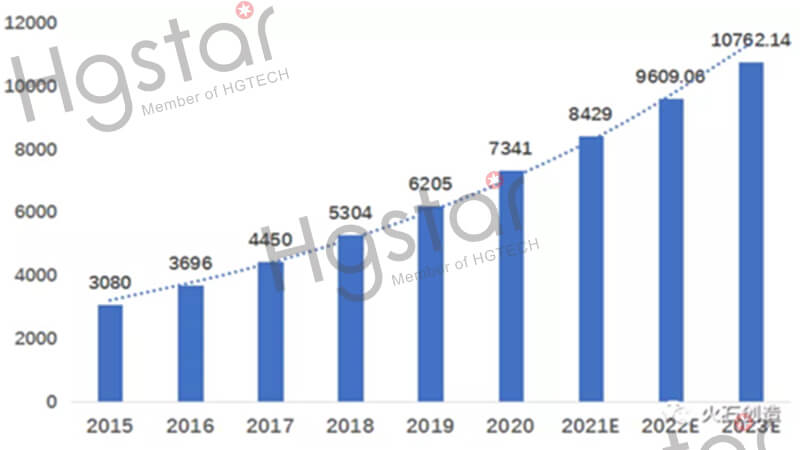
The segmented development of the medical device industry, technological iteration, and industrial upgrading have raised the bar for device manufacturing and processing capabilities: it must not only meet the demand for high-end medical devices, but also reduce production costs and personnel input via intelligent processing equipment.
Laser processing has the benefits of high precision, flexible processing, energy savings, environmental protection, safety, and cleaning, and it can perform a variety of processes such as marking, cutting, welding, and cleaning on a variety of materials. As a result, laser processing is “blowing up everywhere” in the medical device industry.
In the medical industry, there are numerous applications for lasers.
1. Laser welding
Medical + Laser Welding Pain Points
- Difficulty in welding dissimilar materials due to differences in melting point, coefficient of expansion, thermal conductivity, and specific heat capacity, as well as differences in material structures.
- The product has a small fine size, high precision requirements, and enlargement requires a high-magnification visual aid.
2. Laser cutting
Medical + Laser Cutting Pain Points
- The material is easily deformed, the thermal influence is too great, the edges are severely carbonized, there are burrs, the cutting gap is large, and the precision is low when cutting ultra-thin materials (generally refers to thickness 0.2mm).
- Biodegradable materials have a low thermal melting point and are temperature sensitive.
- Brittle materials are prone to edge chipping, surface microcracks, and residual stress issues, resulting in low product yield.
3. Laser surface treatment
Medical + Laser Surface Treatment Pain Points
The thickness of the oxide layer on the metal surface varies, resulting in inconsistent marking effects or the breakdown of the oxide layer, resulting in salt spray and anti-corrosion test failure.
- The product size has been reduced, and the graphic size of the logo is extremely small.
- Micropores in metals, ceramics, and other materials are difficult to process.
- Difficulty in microprocessing biocompatible component surfaces.
Ultrafast lasers bridge the gap in medical applications.
Ultrafast Laser
Ultrafast laser refers to a pulsed laser whose output laser pulse width is 10-12s (ie picosecond level) or less than picosecond level.
Advantage:
- “Cold working” reduces melt zone and heat affected zone, no recast layer.
- No microcracks, better surface quality.
- Less energy absorption by wavelengths and materials.