Projects
How Effective Is the Metal Laser Cutting Machine in Cutting Metal
Laser cutting has no burrs and high accuracy. Next, we will explain several common metal materials.
Carbon steel. Because carbon steel contains carbon, which does not reflect light strongly and absorbs light beams well, carbon steel is suitable for laser cutting machine processing among all metal materials. Therefore, carbon steel laser cutting machines have an unshakable position in carbon steel processing.
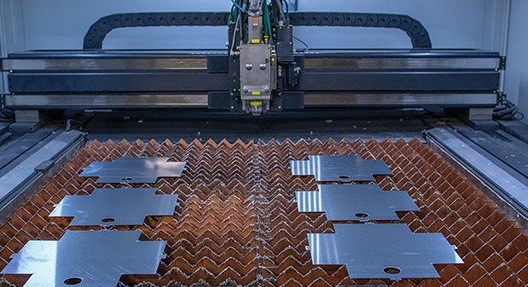
Stainless steel. Laser cutting of stainless steel uses the energy released when a laser beam is irradiated on the surface of the steel plate to melt and evaporate the stainless steel. For the manufacturing industry that uses stainless steel sheets as the main components, laser cutting of stainless steel is a fast and effective processing method. The important process parameters that affect the quality of stainless steel cutting are cutting speed, laser power, air pressure, etc.
Aluminum and alloys. Although laser cutting machines can be widely used in the processing of various metal and non-metallic materials. However, some materials, such as copper, aluminum, and their alloys, have their own characteristics (high reflectivity) that make laser cutting difficult to process.
Copper and alloys. Pure copper (red copper) cannot be cut with CO2 laser beams due to its high reflectivity. Brass (copper alloy) uses higher laser power and auxiliary gases such as air or oxygen, which can cut thinner plates.
Titanium and alloys. The titanium alloy laser cutting commonly used in the aircraft manufacturing industry has good quality. Although there may be a small amount of slag at the bottom of the cutting seam, it is easy to remove. Pure titanium can effectively couple and focus the thermal energy converted by laser beams. When oxygen is used as an auxiliary gas, the chemical reaction is intense and the cutting speed is fast. However, it is prone to generating an oxide layer on the cutting edge, which can cause overheating if not careful. For safety reasons, it is better to use air as an auxiliary gas to ensure cutting quality.
Alloy steel. Most alloy structural steel and alloy tool steel can achieve good edge cutting quality using laser cutting methods. Even for some high-strength materials, as long as the process parameters are properly controlled, a straight and slag free cutting edge can be obtained. However, for high-speed tool steel and hot mold steel containing tungsten, there may be erosion and slag sticking during laser cutting machine processing.
Nickel alloy. There are many varieties of nickel based alloys. Most of them can be oxidized and melted for cutting.
Factors affecting the cutting speed and cutting effect of metal laser cutting machines
- Working power and mode of laser equipment:
After research, it has been proven that the higher the power of laser equipment, the better the effect even when cutting the same sheet metal. The mode of laser cutting has a certain degree of compatibility with the material, and the higher the effect, the better.
- The thickness and roughness of the material:
Laser cutting machines are most suitable for cutting thin plates, with the best thickness being carbon steel below 12mm and stainless steel below 6mm. The processed quality is significantly enhanced, and efficiency is also guaranteed. If cutting<1mm material, the incision will also be extremely smooth. The surface roughness of materials also determines the quality of cutting. Generally, the smoother the material, the better the quality of the cut.
- Cutting speed:
In fact, no matter what type of material it is, it can make the cutting speed extremely consistent with the material, so the cutting effect is the best at this time. If the speed is too fast or too slow, it will have an impact on the cutting quality.
- Focus position:
The focus of the laser cutting machine is aligned, and the accuracy and precision of the cutting can meet the ideal requirements.
- Auxiliary gas pressure and type:
The higher the pressure of the auxiliary gas, the higher the purity of the gas, the less impurities adhered to the material, and the smoother the cutting edge. Generally speaking, the speed of oxygen cutting is the fastest, while the cutting effect of nitrogen is the best and the cost is also low. The cutting effect may vary depending on the gas used.
About HGSTAR: HGSTAR is is a sub-brand of HGTECH.HGTECH the pioneer and leader of laser industrial application in China, and the authoritative provider of global laser processing solutions. We have comprehensively arranged laser intelligent machine, measurement and automation production lines, and smart factory construction to provide overall solutions for intelligent manufacturing.