Projects
Problems with Laser Welding of Explosion-Proof Valves For Power Batteries
Power batteries are one of the core components of new energy vehicles, so the safety and performance of power batteries are also of great concern. Among them, explosion-proof valves are key components used to control the overcharging pressure and temperature of batteries. In order to ensure the safety and stability of the battery, the explosion-proof valve in the power battery is usually connected using laser welding technology. This article will comprehensively analyze the common problems and solutions of laser welding for explosion-proof valves, including the principle of laser welding, the welding method of explosion-proof valves, and the problem of explosion points when welding explosion-proof valves.
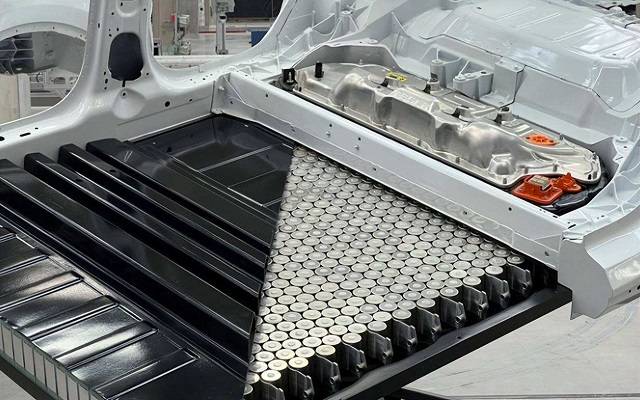
1、 The principle of laser welding
Laser welding is a method of using a laser beam to melt the surface of a welded joint and connect the welded parts. The principle is to apply a high-energy laser beam to instantly melt the surface of the welding material at the welding joint, achieving the purpose of bonding. Due to the advantages of small focus, high energy density, and high single vibration rate, laser beams are widely used in the welding of battery components.
2、 Welding method for explosion-proof valve of power battery
In power batteries, explosion-proof valves are usually connected together by several welding points. Laser welding is one of the preferred methods for connecting explosion-proof valves. Usually, there are two main methods of laser welding. One is laser transfer welding, which means that the laser beam is transmitted from the optical fiber for welding; Another method is handheld laser welding, which uses a laser pistol to manually control the welding points.
3、 Reasons for explosion points during welding of explosion-proof valves for power batteries
In the actual laser welding process of explosion-proof valves, there is always a situation of welding explosion points, which is caused by the current generated during the welding process. During the laser welding process, it is necessary to heat the solder joints on the explosion-proof valve and provide current to ensure the depth and breadth of melting. If the current is too high, the valve and separation membrane inside the explosion-proof valve will be torn, leading to the occurrence of explosion points.
4、 How to solve the problem of explosion point of explosion-proof valve for welding power batteries
Preventive measures should be taken to address the issue of welding explosion points in laser welding of explosion-proof valves for power batteries.
Based on the causes of this problem, it can be mainly solved through three aspects:
Control the size of welding current
The welding current should be controlled reasonably, and it is better to use sequential spot welding for welding.
Improve the quality of explosion-proof valves
To prevent problems with explosion-proof valves, it is recommended to improve the material selection, quality control, and welding process of explosion-proof valves to improve their quality and performance.
Standardized operation
In the actual welding process, standardized operations and improved welding techniques can be used to ensure welding quality and reduce the occurrence of explosion points in power battery explosion-proof valves.
In summary, laser welding technology is one of the preferred methods for welding explosion-proof valves in power batteries, but explosion points often occur during the welding process of explosion-proof valves. Therefore, in practical application, we need to have a certain understanding of the principle and method of laser welding, and take relevant preventive measures in the material selection, quality control and welding process of the explosion-proof valve to ensure the welding effect and battery safety.
The higher the pressure of the auxiliary gas, the higher the purity of the gas, the less impurities adhered to the material, and the smoother the cutting edge. Generally speaking, the speed of oxygen cutting is the fastest, while the cutting effect of nitrogen is the best and the cost is also low. The cutting effect may vary depending on the gas used.
About HGSTAR: HGSTAR is is a sub-brand of HGTECH.HGTECH the pioneer and leader of laser industrial application in China, and the authoritative provider of global laser processing solutions. We have comprehensively arranged laser intelligent machine, measurement and automation production lines, and smart factory construction to provide overall solutions for intelligent manufacturing.