Projects
Interpretation of Standard Terms for Precision Testing of Laser Tube Cutting
The development of laser tube cutting equipment in China is rapid. According to statistics, in 2020, the cumulative sales volume of high-power CNC laser tube cutting equipment in China reached about 5000 units (sets), with a growth rate of 20% to 30%. However, there are no corresponding national or industry standards, and there are no specific technical conditions and accuracy inspection specifications for laser tube cutting equipment abroad. This poses great difficulties for manufacturers and consumers in shipping and purchasing, and can easily cause some low-quality products that endanger user safety to flood the market, which is very unfavorable for the development of the industry.
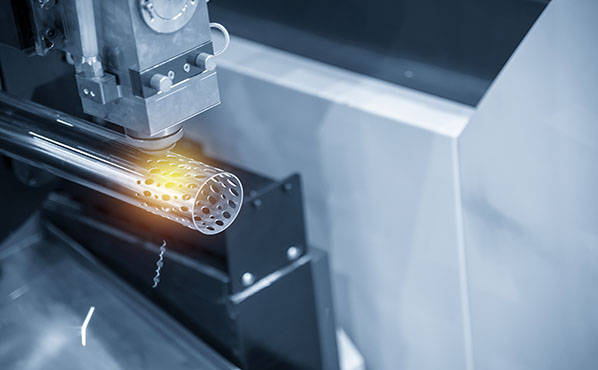
Therefore, it is necessary to establish standard specifications for the accuracy and technical requirements of laser tube cutting equipment. This is of great significance for promoting the standardization of laser tube cutting equipment design and inspection, effectively improving the manufacturing quality of the equipment, and ensuring the personal safety of users.
2.1 Geometric accuracy inspection
The geometric accuracy of a machine tool is the basic indicator for judging the quality of the machine tool. To ensure the working accuracy of the machine tool, relevant accuracy experience and testing of the main technical indicators should be conducted during production, purchase acceptance, regular inspection, repair, and when there are doubts about accuracy issues during use. The geometric accuracy inspection of the laser pipe cutting machine consists of 8 inspection items, namely: (1) the straightness of the X axis moving in the XY horizontal plane; (2) The straightness of the Y-axis movement in the XY horizontal plane; (3) The parallelism of the Y-axis motion to the XY horizontal plane; (4) The perpendicularity of the Z-axis movement to the XY horizontal plane; (5) The radial runout of the A2 axis; (6) The parallelism of the A2 axis with respect to the X axis movement; (7) Parallelism between the end face of chuck 1 chuck seat and the Y/Z axis; (8) The relative radial runout of A1 axis and A2 axis synchronous drive. The inspection tools mainly include autocollimators, rulers, angle rulers, indicators, micrometers, measuring blocks, etc. The inspection should also comply with the relevant provisions of GB/T 17421.1-1998.
2.2 Positioning accuracy inspection
Like geometric accuracy, positioning accuracy has a significant impact on the machining accuracy of machine tools, which is an important indicator of customer concern and requires shipment inspection and testing. This section specifies the inspection methods and allowable values for the positioning accuracy, repeated positioning accuracy, and reverse positioning difference of the X-axis, Y-axis, Z-axis, A1 axis, and A2 axis of the pipe cutting machine tool. The inspection tool mainly uses a laser interferometer, which places the moving parts of the non detection axis in the middle of their stroke for inspection. The inspection should also comply with the provisions of 4.3 in GB/T 17421.2-2016.
2.3 Processing inspection
For the cutting of thin-walled pipes, the industry mainly focuses on the dimensional accuracy of the cutting workpiece. The standard uses carbon steel (Q235B), which is the most commonly used material in the industry, as the processing material. A circular tube with a thickness of 3 mm and a diameter of 100 mm or a square tube with a side length of 100 mm is used. The cutting speed is selected according to 50% of the maximum allowable cutting speed for 3 mm carbon steel given in the user manual. A sample workpiece is cut and the dimensional accuracy of the cutting is checked using a vernier caliper and a tool microscope as measuring instruments, with a tolerance of ± 0.15 mm, The tolerance for positional accuracy is 0.4 mm.
For the accuracy inspection of cutting medium to high thickness pipes (with a standard thickness of 8 mm as an example), in addition to checking the dimensional accuracy of the laser pipe cutting machine, it is also necessary to check the inclination and surface roughness of the cutting surface. This is because the inclination and surface roughness of the cutting surface will affect the subsequent processing effect of the workpiece, so these two indicators are the key points for evaluating the cutting quality of medium thick pipes.