Projects
Laser Glass Cutting Solution: Detonate the Revolution of Glass Camera Industry
Under the current development trend, the market’s demand for mobile phone functions tends to be diversified, especially in terms of cameras. Good requirements for photography, sensitivity, depth focus and so on have made three cameras and four cameras popular. Moreover, the short board of CNC (Computer numerical control) processing has become increasingly prominent, and laser replacing CNC has become an inevitable trend.
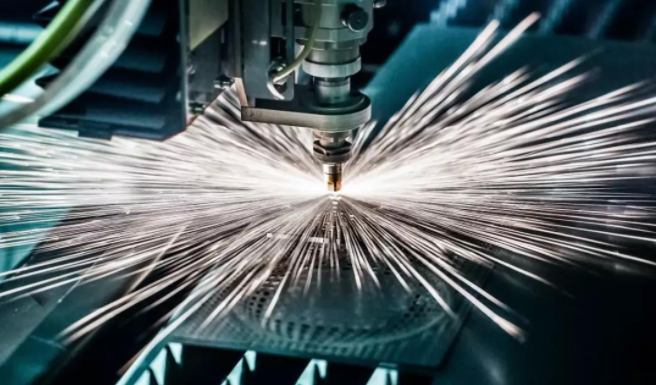
The mobile phone glass camera industry has a strong market demand, and the price is generally low due to fierce competition. In the actual production process of traditional CNC manufacturing technology, there are problems such as low processing efficiency and yield, frequent replacement of cutter wheel, and bad processing environment, which make the industry enter the Red Sea. The process validation of laser replacing CNC is in full swing. From the process validation, we can see that laser is a subversive process revolution in the glass camera industry, which can bring 10-15 points of yield improvement to customers, simplify the process by 1/3, reduce personnel by 40%, reduce the process cost by more than 30%, significantly improve profits, and improve the working environment.
Process principle of laser cutting glass
The ultra-fast laser beam, which is focused by the focusing head, has a peak power density. When the beam acts on the glass material, the central light intensity of the beam is lower than the edge, which makes the central refractive index of the material change more than the edge, and the propagation speed of the light center is slower than the edge. The beam has nonlinear optical Kerr effect to produce self-focusing, and continues to improve the power density. Until a certain energy threshold is reached, the material will produce low density plasma, reduce the central refractive index of the material, and realize beam defocus. In the actual cutting of glass, the focusing system and focal length can be optimized to realize the repetitive focusing/defocusing process and form a stable perforation.
Wire cutting is a feasible process. The laser industry has its own solution. At the same time, it has been widely used in the display industry. When the ultra-fast laser beam propagates through the glass material, there are Kerr self-focusing and plasma defocusing at the same time. The laser beam can realize long-distance propagation in the dynamic balance of the two, and form micron-sized wire holes in the material, which can extend several millimeters in depth in the glass. Linear motor controls the glass workpiece to move relative to the laser beam to generate a number of wire holes with equal spacing, and micro-cracks along the diameter direction are generated by optimizing the wire hole spacing. Applying special action to the glass with microcracks can increase the stress at the microcracks, make the glass break along the microcracks, and achieve the purpose of cutting.
For glass processing, the laser spot can be shaped into a “long filament” through optical diffraction devices. According to different glass thickness, a cutting head with corresponding focal depth length is required. Adjust the laser focus position through the Z axis of the device to confirm the focus of the laser cutting glass sample; The cutting drawing file is generated by software, and the glass sample is moved along the path of the drawing file by linear motor motion for laser cutting, so as to obtain the large glass cutting sample under the corresponding graphics; Then carry out glass post-processing processes such as full-plate cleaning, strengthening and screen printing for full-plate glass cutting products, and finally obtain small pieces of glass with a certain shape by using a specific split method. In addition, after product debugging, the parameters can be directly saved to the software parameter library, and then can be directly called according to the type and thickness of the corresponding glass sample to cut the product.
Glass cutting application solution
In 2019, under the influence of many disadvantages of traditional CNC processing and the continuous strong impact of laser applications, laser equipment emerged in the glass camera industry, realizing partial replacement of traditional applications. In view of the extremely advantageous input-output ratio of laser equipment processing, end customers and processing manufacturers have gradually recognized the influx of this application.
The continuous growth of the market capacity of laser equipment has brought a good momentum for high-end intelligent manufacturing. Not only in the existing camera industry, but also in other industries such as display, vehicle, semiconductor, and so on, have also been enhanced by the increase of laser equipment. The market is also enjoying the huge benefits of laser manufacturing. Despite the impact of the epidemic in 2020, the economic system has changed to some extent, but this is always temporary. With the good control of the epidemic, the laser application will certainly complete the perfect takeover of traditional industries. In the process of moving towards high-end intelligent manufacturing, it will play its unique charm and help technology move forward.
About HGSTAR: HGSTAR is is a sub-brand of HGTECH.HGTECH the pioneer and leader of laser industrial application in China, and the authoritative provider of global laser processing solutions. We have comprehensively arranged laser intelligent machine, measurement and automation production lines, and smart factory construction to provide overall solutions for intelligent manufacturing.