Projects
Laser Welding of Lithium Battery Poles
Lithium batteries are a type of high energy density battery widely used in electric vehicles, drones, mobile devices, and other fields today. In lithium batteries, the quality and stability of battery poles play an important role in the overall performance of the battery. Therefore, the laser welding process of lithium battery poles is increasingly receiving research and application attention.
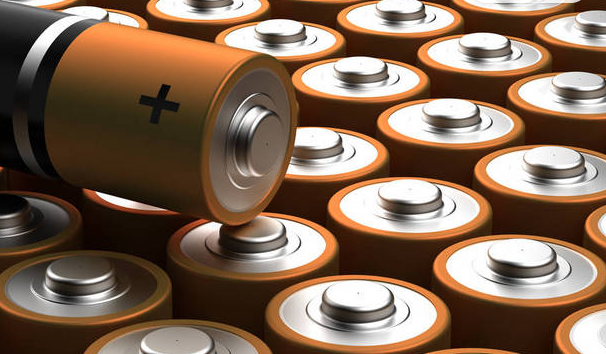
1、 Laser welding process for lithium battery poles
The process of laser welding for lithium battery poles mainly includes metal selection, laser welding parameters, welding forms, and post welding treatment. Reasonable metal selection can ensure the quality and strength of the weld seam; The selection of laser welding parameters is a key factor affecting the formation of weld seams, which needs to be optimized based on the properties and requirements of the welding material; Welding forms include spot welding, transverse welding, and longitudinal welding, and different forms are suitable for different welding materials.
In terms of post welding treatment, it is necessary to ensure the quality and reliability of the weld seam. In actual production, methods such as microscopic observation, mechanical testing, and non-destructive testing can be used to detect and evaluate welding quality.
2、 Laser welding method for lithium battery pole
At present, there are two methods for laser welding of lithium battery poles: traditional direct welding and indirect welding. Direct welding refers to the direct welding of two metal components together, while indirect welding refers to the welding of two components separately onto a middleware, which is then welded together with another component. The use of indirect welding can better control the thickness and position of welding, improve welding quality, and avoid welding cracks. However, indirect welding requires more cost and time, and is still the main method of direct welding.
3、 The Function of Lithium Battery Pole Laser Welding Machine
The lithium battery pole welding machine is the core equipment of laser welding, whose function is to concentrate the laser beam on the welding point, generate high temperature, melt and solidify the welding material. This equipment has the advantages of high efficiency, precision, and low pollution, which can meet the needs of high-precision and high-quality welding. At present, major lithium battery manufacturers both domestically and internationally have started using lithium battery pole laser welding machines for production.
4、 Future Development Prospects of Lithium Batteries
Lithium batteries, as a high energy density battery, have the advantages of lightweight, high efficiency, and environmental protection, and have been widely used in fields such as mobile devices and electric vehicles. With the continuous progress of technology and the continuous development of the industry, lithium batteries will play an increasingly important role in the future energy field. In the future, with the increasing demand for energy security and environmental protection, lithium batteries will face broader and deeper market and technological challenges, as well as more opportunities and development space.
Laser welding of lithium battery poles is one of the key welding processes in the production of lithium batteries, and its quality and stability have a significant impact on the overall performance of the battery. With the continuous development and maturity of technology, the future development prospects of lithium batteries are very broad, and we have reason to expect them to demonstrate stronger capabilities and performance in a wider range of applications.
About HGSTAR: HGSTAR is is a sub-brand of HGTECH.HGTECH the pioneer and leader of laser industrial application in China, and the authoritative provider of global laser processing solutions. We have comprehensively arranged laser intelligent machine, measurement and automation production lines, and smart factory construction to provide overall solutions for intelligent manufacturing.